An electrical motor powers an ingenious machinery called a rigid gas air compressor. Inside the contraption, a crankshaft is connected to a piston, creating movement as the motor rotates. This action forces air through a cylinder, increasing the air pressure in the process. In this way, the rigid gas air compressor is equipped to maintain optimal air pressure within its system.
For many sectors, the air compressor is considered necessary hardware. Its uses are varied – from propelling air tools, inflating tires, empowering other pieces of equipment and circulating air in the HVAC arena.
Compressors are best described as two variants: positive displacement and negative displacement. A positive displacement compressor works by creating a pocket of air within a designated chamber and subsequently compressing the airtight space. This surge in force diminishes the amount of space within the chamber – thus increasing the density of the air particles – and in turn propelling them into an even smaller region, such as a hose or portable air tool.
An airtight chamber acts as the epicenter of negative displacement compressors as it takes in air and then compresses it while expelling it from the chamber. Unlike positive displacement compressors, these are far more efficient as they are adeptly able to avoid the loss of any air during compression.
An array of rigid air compression systems come in an extensive selection of sizes and structures. Picking the right one relies on the amount of pressurised air that will be necessary and the use it will be put to.
To measure a compressor’s performance, its air flow rate and maximum pressure level are taken into account. The air flow rate is the amount of air that the device is able to output over a specific duration, while maximum pressure denotes the peak pressure that the compressor can generate.
Compressors are divided into two categories, based on the number of cylinders involved in their processes. A single-stage compressor uses just one chamber, while a two-stage device has two. The air is first compressed to a lower pressure level in the first cylinder and continues to be reduced to an even more extreme pressure in the second.
Gas-powered air compressors come in two varieties – oil-lubricated and oil-free. While you need to replenish the oil in the former regularly, no such effort is required with the latter though it may require different kinds of maintenance.
For a plethora of needs and demands, rigid gas air compressors are the steadfast solution. From driving powerful air driven tools, such as nail guns and impact wrenches, to inflating tires and running other machinery – these machines are essential to the process.
Compressing air necessitates multiple sizing and configuration capabilities, thus rigid gas air compressors can offer a diverse range of solutions. The correct size of the compressor is contingent on the quantity of air that needs to be squeezed, whereas the configuration depends on the specific purpose or application.
Post time: 2023-06-21Related Product
Warning: Use of undefined constant rand - assumed 'rand' (this will throw an Error in a future version of PHP) in /www/wwwroot/www.sunritamachinery.com/wp-content/themes/msk5/single.php on line 69
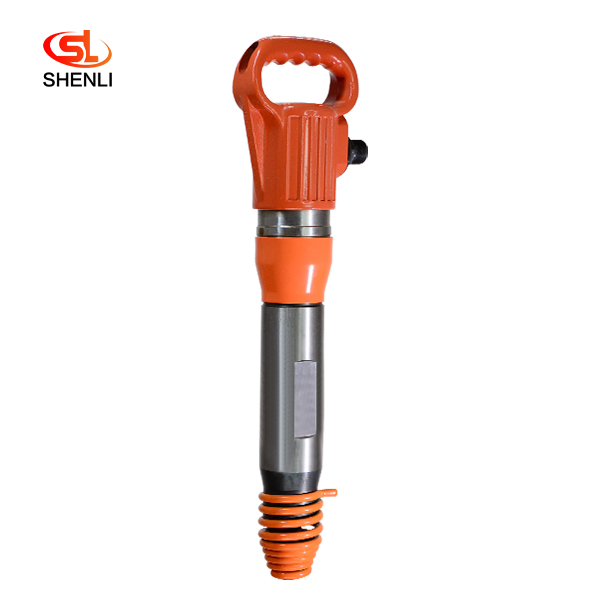
G10 Pneumatic Pick Air Shovel Cement Crusher
Product Description: The G10 air pick uses compressed air as the power tool, and the compressed air is distributed in two sections of the cylinder by the tubular distribution diver […]
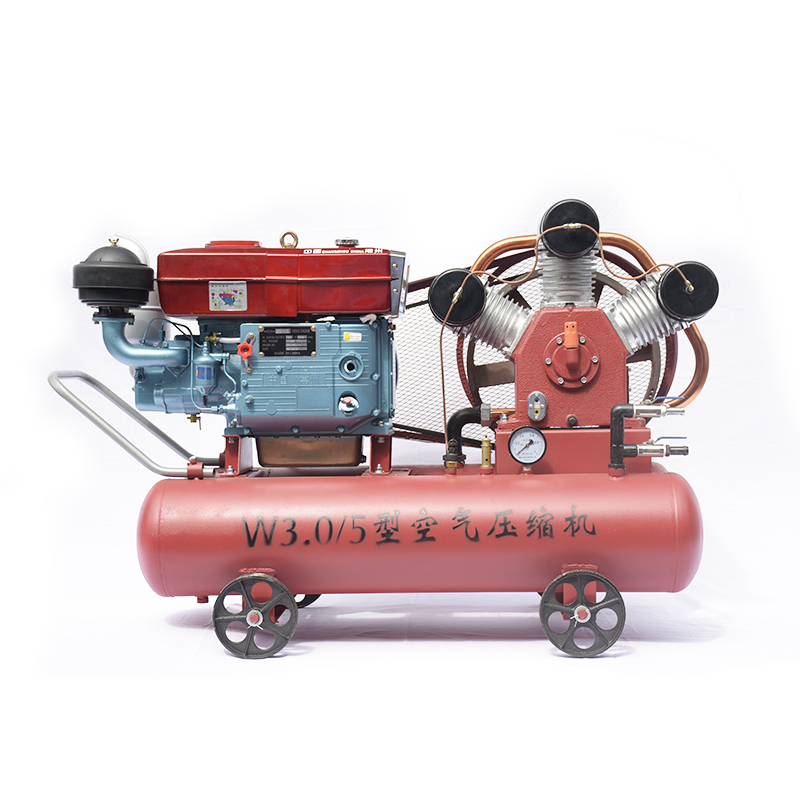
15kW Mining Diesel Piston Air Compressor W3.0-5
Diesel Portable Piston Air Compressor Mobile for Jack Hammer / Mining 1.Simple structure,light weight,easy to move . 2.Easy operating and maintenance. 3.High quality air delivery. […]
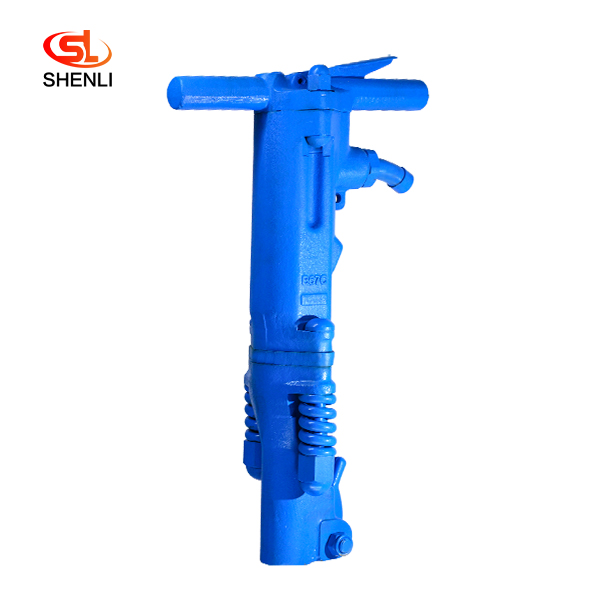
B67C Pneumatic Chipping Hammer
Product description: The B67C crusher is made from Canada. Denver pneumatic Group company mature technology, with compressed air as a power crushing tool, can efficiently complete […]
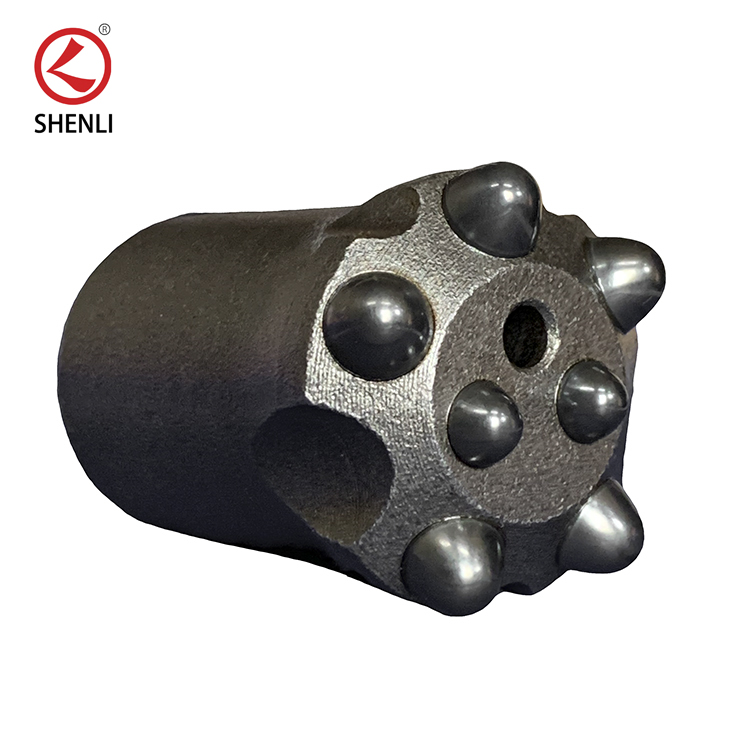
Rock Drill Button Bit
Product introduction: Taper bits, especially Tapered button bits are the most popular tapered drill bits with a wide selection of head diameters from 26mm to 48mm. With carbide but […]
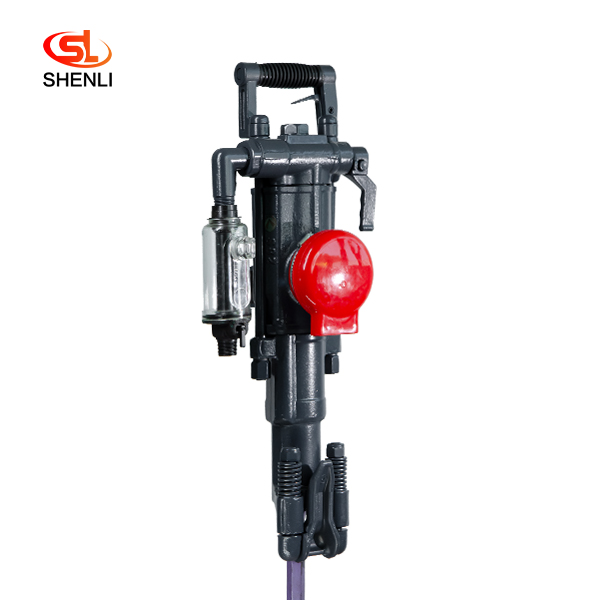
S82 Air Leg Pneumatic Rock Drill Pusher Leg Rock Drill
Scope of application: Model S82 air-legged rock drills are heavy-duty air-legged rock drills with high efficiency and low consumption, which are especially suitable for use in the […]
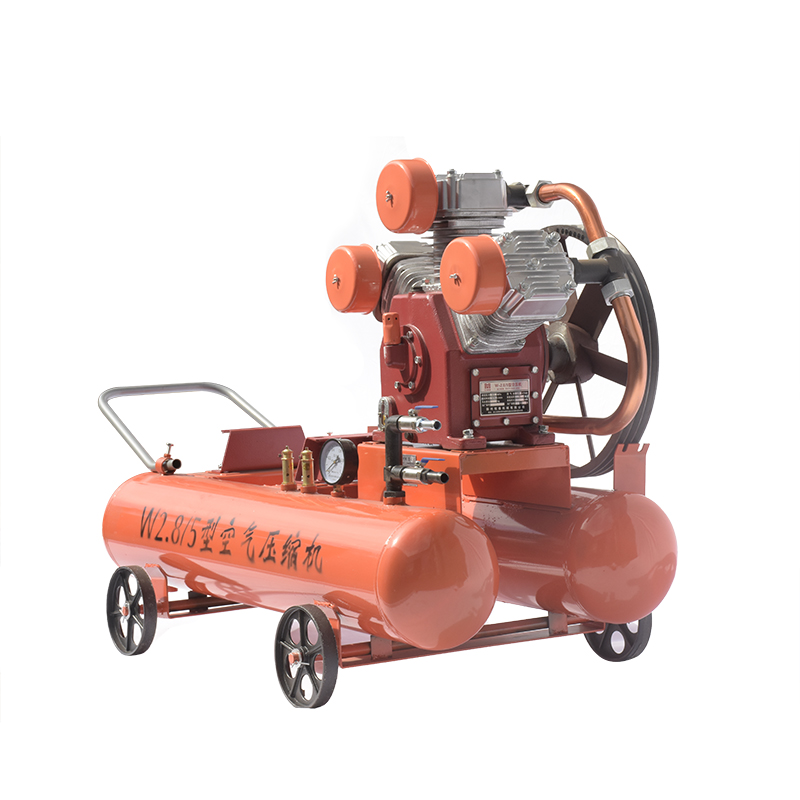
15KW Mining Diesel Piston Air Compressor W2.8-5
Diesel Portable Piston Air Compressor Mobile for Jack Hammer / Mining 1.Simple structure,light weight,easy to move . 2.Easy operating and maintenance. 3.High quality air delivery. […]
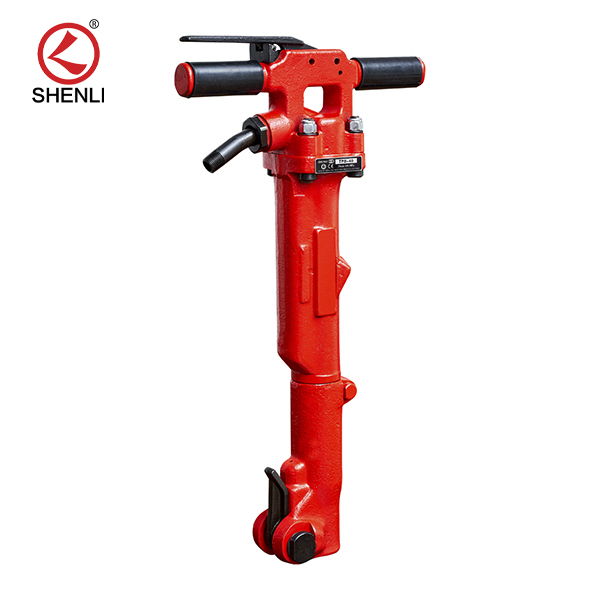
TPB40 Air Breaker Pavement Paving Breaker
Product introduction: Tpb-40 pneumatic crushing pick is a tool powered by compressed air.The compressed air is distributed to both ends of the cylinder block in turn to make the ha […]
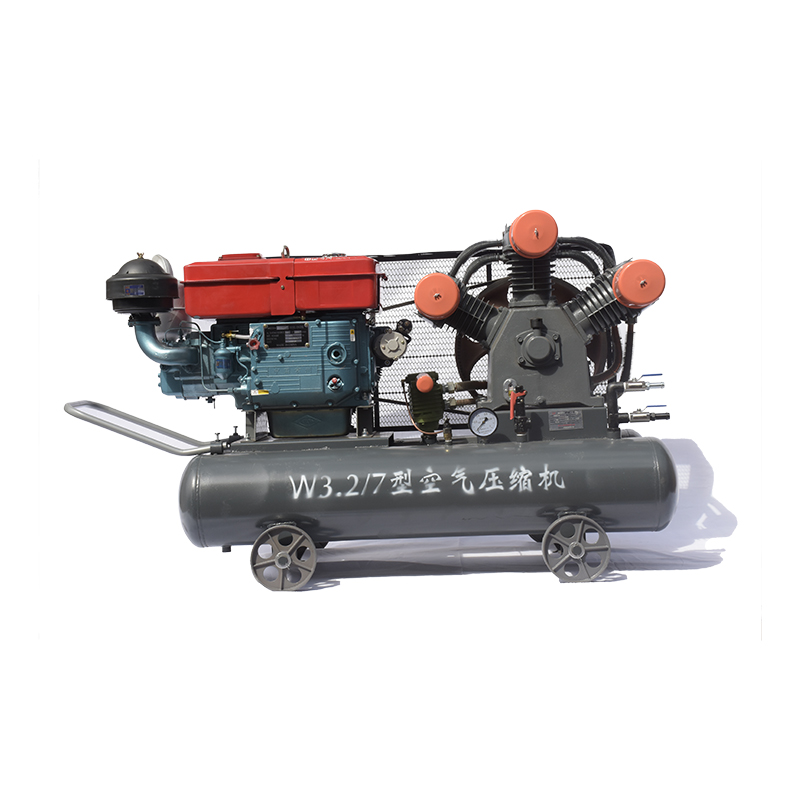
20KW Mining Diesel Piston Air Compressor W3.2-7
Advantages Small in size,light in weight, easy to move Top material and superior technology Simple structure, high efficiency, good performance, and low price Adopt the most popula […]
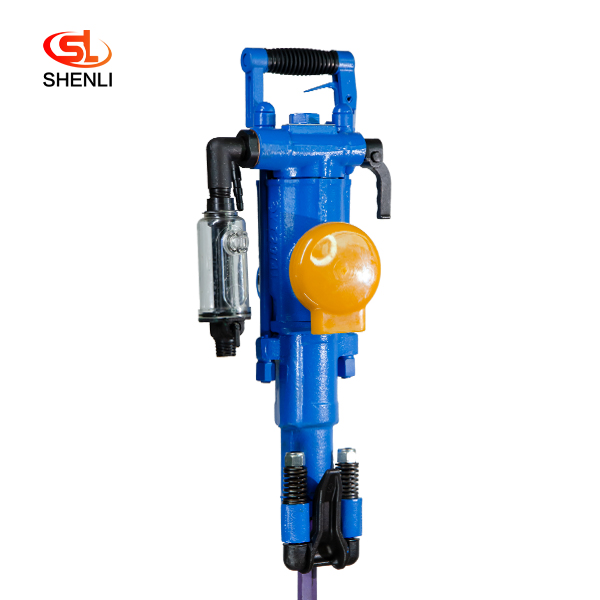
YT29A Air Leg Pneumatic Rock Drill
Short Description: YT29A air-legged rock drills are heavy-duty push-leg (air-legged) rock drills with low energy consumption, which are more suitable for drilling horizontal or inc […]