An air compressor is an ingenious device which takes power from sources like electric motors, diesel or gasoline engines and converts it to pressurized air – essentially, potential energy stored for later use. This is accomplished by pumping air in stages until the pressure within the vessel reaches its optimal high. When the marker is reached, the compressor stops functioning, keeping the force of the air contained until it is needed.
Pressure relief valves make it possible to disperse the gathered compressed air back into the outside world, or alternatively, the pressurized air can be channelled to a pneumatic device, for example a nail gun or air ratchet. Compressors operate in a manner that is akin to pumps; they amplify the pressure of a fluid and allow it to be transported via a pipe. Gases are conveniently compressible, making them ideally suited for the application of compressors, which act to decrease the size of such substances. Liquids have low compressibility, so while certain liquids may be suitable for compression, this form of technology is generally used for handling gases.
Five distinct varieties of air compressors exist in today’s market. From reciprocating piston compressors to rotary vane, screw, centrifugal and scroll systems – the selection ranges in terms of design, application, and performance.
With their piston-powered up and down motions, reciprocating/piston air compressors are the most widely employed type of pressurised air system. Air is drawn into the chamber via an intake valve and is then compressed by the piston and released through an exit valve. As such, a crankshaft drives the piston to successfully achieve this pressurising process.
Two specifically crafted screws, known as rotors, rotate in unison to compress the air when a drive shaft is activated. As they rotate, the size of the chamber gradually decreases, pushing the air particles backwards and compressing them in the process. The screws are soaked in oil and travel through the oil’s layers, which subsequently cools the tightly compressed air.
As the rotor rotates, vanes mounted onto it move in and out, decreasing the size of the chamber, effectively compressing the air within. This is the basis of how rotary vane air compressors operate.
An impeller sits at the heart of a centrifugal compressor and pulls air into its center, before sending it hurtling outwards inward towards the edges. As the air accumulates around the circumference of the compressor, it experiences a pressing on through centrifugal force, thus compressing it.
The technology of scroll air compressors involves an inner scroll which remains stationary, while an outer scroll circles around it. These rotations lead to a reduction in the interior volume of the chamber, consequently effectuating a compression of the air.
Post time: 2023-06-12Related Product
Warning: Use of undefined constant rand - assumed 'rand' (this will throw an Error in a future version of PHP) in /www/wwwroot/www.sunritamachinery.com/wp-content/themes/msk5/single.php on line 69
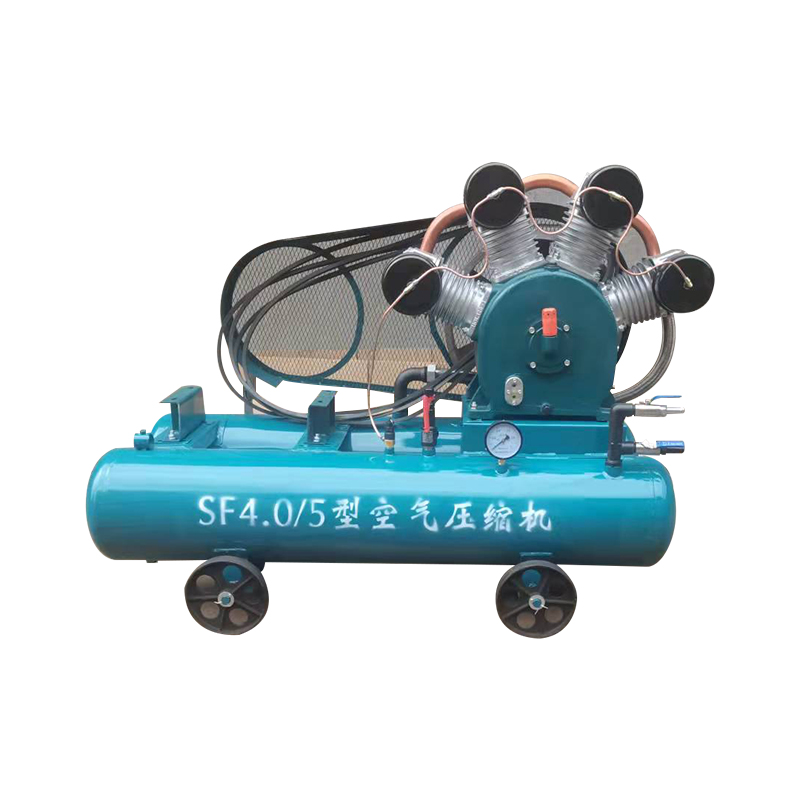
20KW Mining Diesel Piston Air Compressor SF4.0-5
Advantages Small in size,light in weight, easy to move Top material and superior technology Simple structure, high efficiency, good performance, and low price Adopt the most popula […]
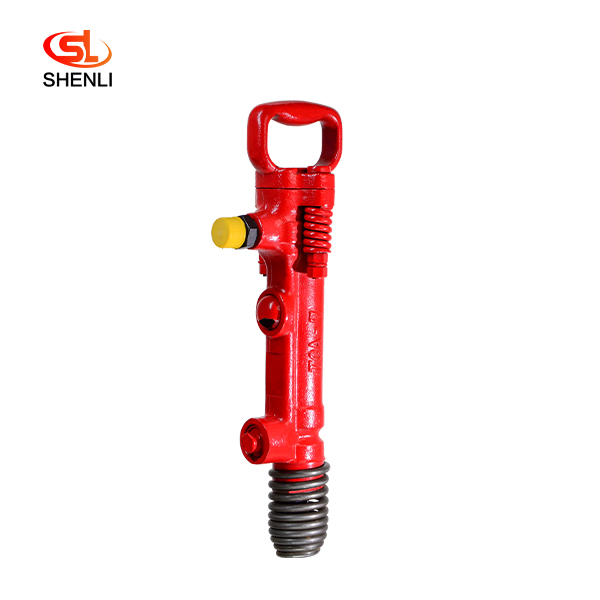
TCA7(G7)Pneumatic Pick Air Shovel Cement Crusher Pneumatic Chipping Hammer
Product introduction: Adopted Japan’s Toku technology, the air picks with proven forging technology are durable, lightweight and good performance, and easy to operate. Mainly […]
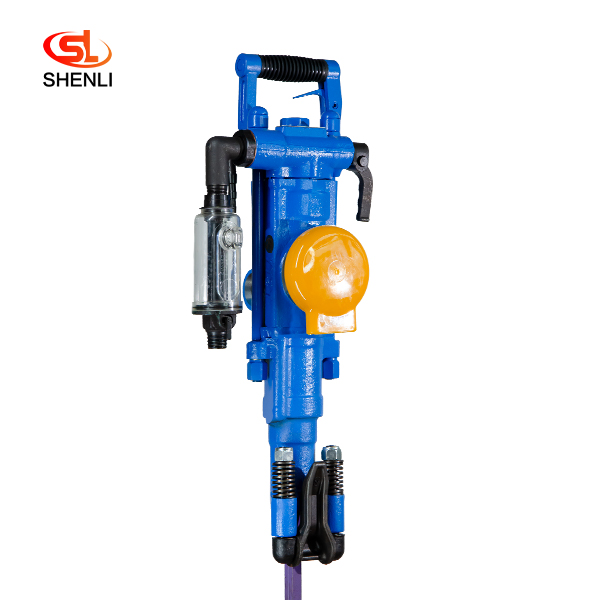
YT27 Air Leg Pneumatic Rock Drill
Short Description: The YT27 air-legged rock drill is a highly efficient lightweight rock drill suitable for downward or inclined drilling in medium-hard or hard (f=8 – 18) ro […]
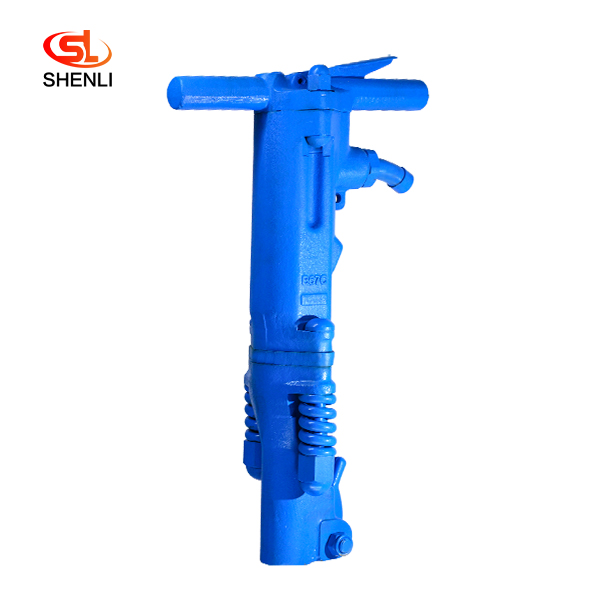
B67C Pneumatic Chipping Hammer
Product description: The B67C crusher is made from Canada. Denver pneumatic Group company mature technology, with compressed air as a power crushing tool, can efficiently complete […]
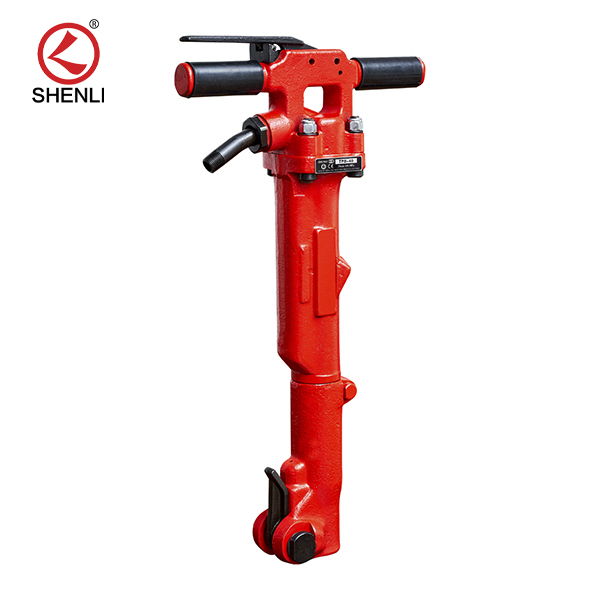
TPB40 Air Breaker Pavement Paving Breaker
Product introduction: Tpb-40 pneumatic crushing pick is a tool powered by compressed air.The compressed air is distributed to both ends of the cylinder block in turn to make the ha […]
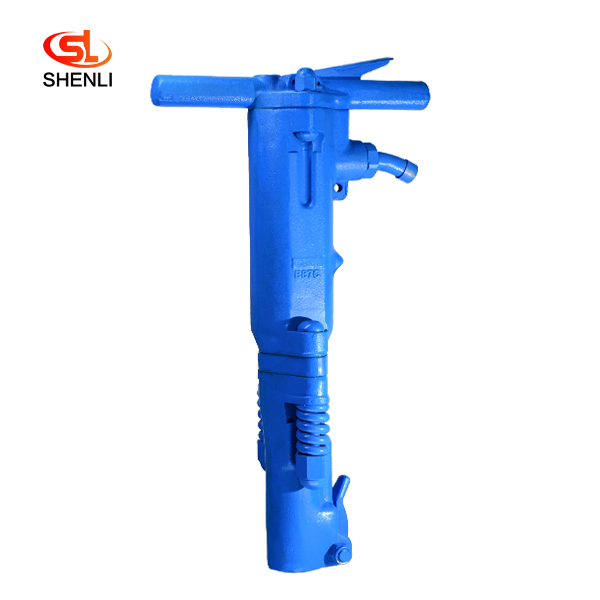
B87C Pneumatic Pick Air Shovel Cement Crusher
Product Description: The B87C crusher is made from Canada. Denver pneumatic Group company mature technology, with compressed air as a power crushing tool, can efficiently complete […]
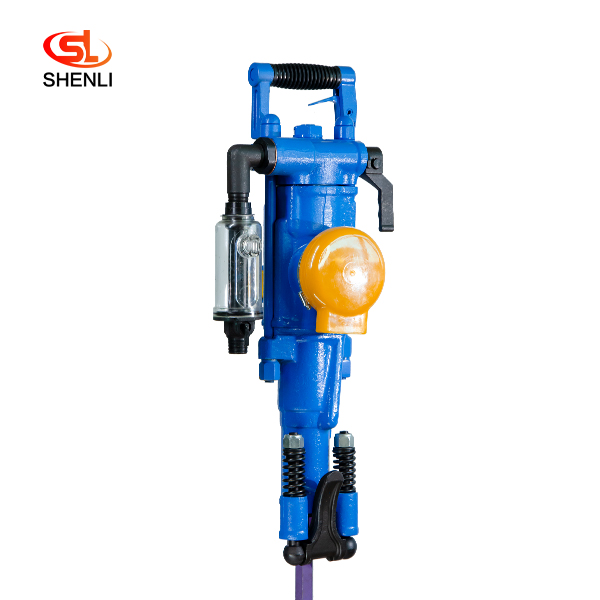
YT28 Pusher Leg Rock Drill
Short Description: The YT28 air-leg rock drill is a kind of high-efficiency, energy-saving and environmentally friendly rock drilling equipment. Compared with similar pneumatic pro […]
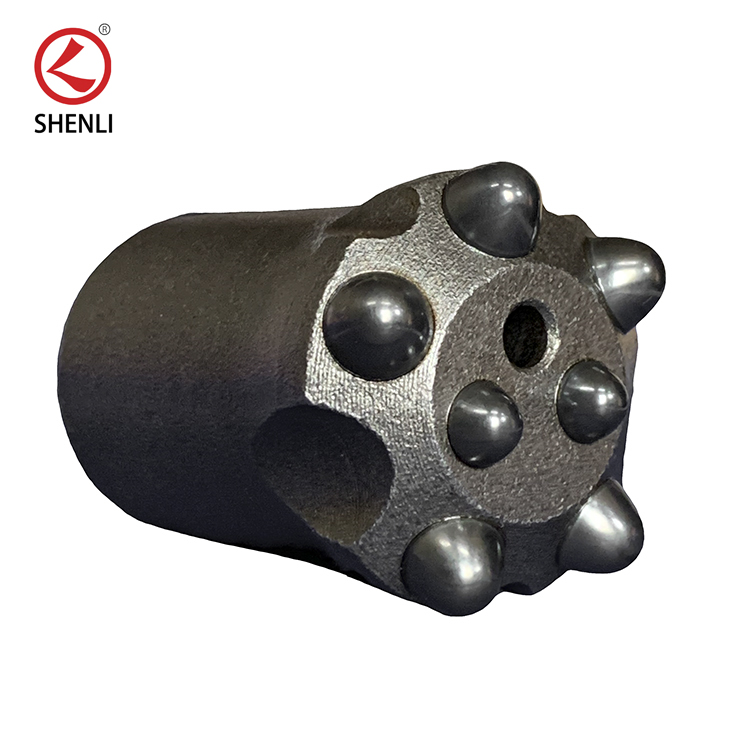
Rock Drill Button Bit
Product introduction: Taper bits, especially Tapered button bits are the most popular tapered drill bits with a wide selection of head diameters from 26mm to 48mm. With carbide but […]
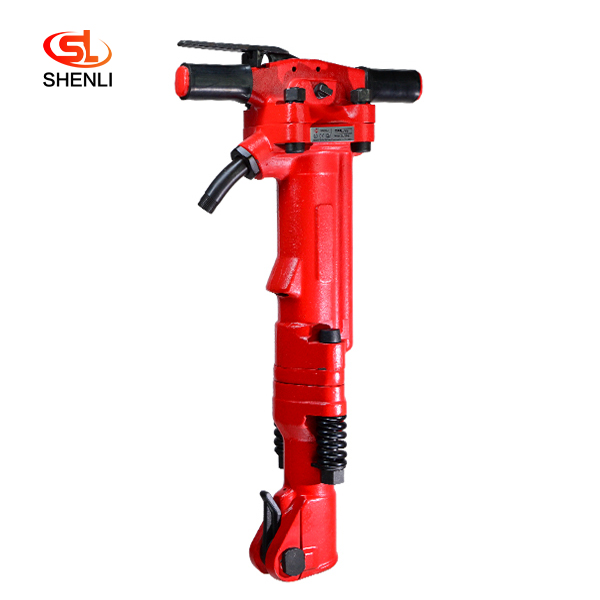
TPB90 Air Breaker Pavement Paving Breaker
Product introduction: TPB-90 crusher adopts the mature technology of TOKU Group, Is compressed air as the power of the crushing tool, can efficiently complete the reinforced concre […]