Air compressors are widely employed across industries for their ability to help with tasks like providing air pressure for pneumatic tools, driving industrial processes, or quickly filling up tires. Although these useful machines have significant energy requirements, installing capacitors can help minimize energy consumption while also boosting the equipment’s efficiency. Doing so can reduce the impact electricity bills and conserve energy in the long run.
A capacitor acts as an electrical powerhouse, harboring a supply of electric charge and voltage until its activation. By connecting to an electrical circuit, the capacitor can open and close based on voltage fluctuations – essentially granting the circuit the ability to store energy. A compressor utilizing capacitors can collect the energy necessary for startup without relying on the power supply – ultimately conserving energy and extending its motor’s lifespan. With this strategy in play, expending energy from the power source to commence is no longer a requirement, with the stored capacitor energy providing an optimized solution that refrains from wasting precious electricity.
Switching on a compressor equipped with capacitors allows electrical current to enter, consequently charging their plates. The capacitors contain this electrical energy for release when an adequate amount of power is amassed. The compressor’s motor needs a burst of energy at the outset of working, which capacitors provide, boosting the motor’s performance while ensuring energy efficiency. The potential difference between the two conductive plates store and sustain the necessary energy burst needed to start the compression and expel air from the system.
Unlock the Benefits of Energy Conservation
The installation of capacitors on an air compressor isn’t only useful for providing reliability; it also helps improve the overall performance. Startup time is decreased thanks to the reduction in electrical load, while still preserving the same standard of energy use.
A Pathway to Lower Electricity Expenses
Despite their additional expense, capacitors prove to be money-savers in the long-run, as they can dramatically reduce electricity costs. When placed on the compressor, their presence will show in reduced energy expenses, thus allowing for a quick restitution of any capital spent.
Magnetic Field Boosts Motor Functionality
Through the dependable protection and increased efficiency bestowed by capacitors, motor components are relieved of strain and maintenance needs are minimized. Furthermore, these capacitors guard the compressor motor from an untimely burnout, providing it with a longer life.
Mitigating Voltage Drops – A Necessary Consideration
Through their continual charge of voltage, capacitors safeguard the compressor’s operation from both fluctuating load conditions and abrupt voltage decreases which could be destructive. This sustained maintenance of electrical energy ensures a steady performance that maximizes the device’s effectiveness.
Air compressors powered with capacitors are a smart investment that yields impressive returns, extending their life expectancy, escalating energy efficiency, and cutting energy-related costs. Being affordable and requiring minimum upkeep, capacitors prove to be a worthwhile upgrade that benefits a diversity of consumers in the manufacturing, mechanical workshop, and other industries. Not only do they provide personal advantages, but also reduce the impact of our activities on the environment while curbing overall carbon output.
Post time: 2023-06-09Related Product
Warning: Use of undefined constant rand - assumed 'rand' (this will throw an Error in a future version of PHP) in /www/wwwroot/www.sunritamachinery.com/wp-content/themes/msk5/single.php on line 69
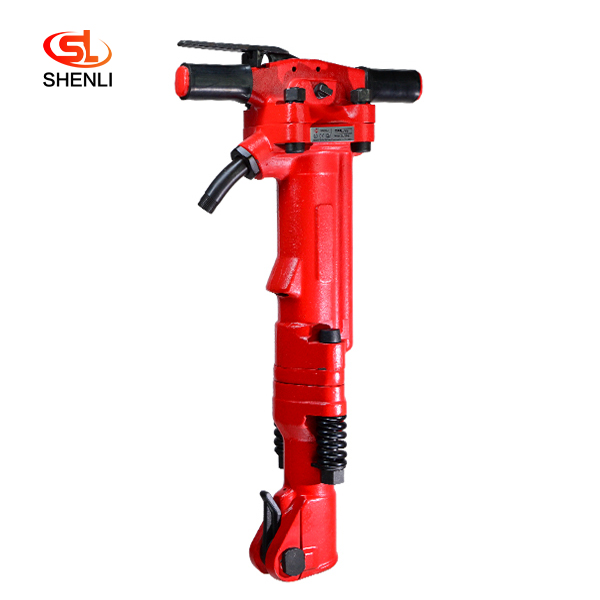
TPB90 Air Breaker Pavement Paving Breaker
Product introduction: TPB-90 crusher adopts the mature technology of TOKU Group, Is compressed air as the power of the crushing tool, can efficiently complete the reinforced concre […]
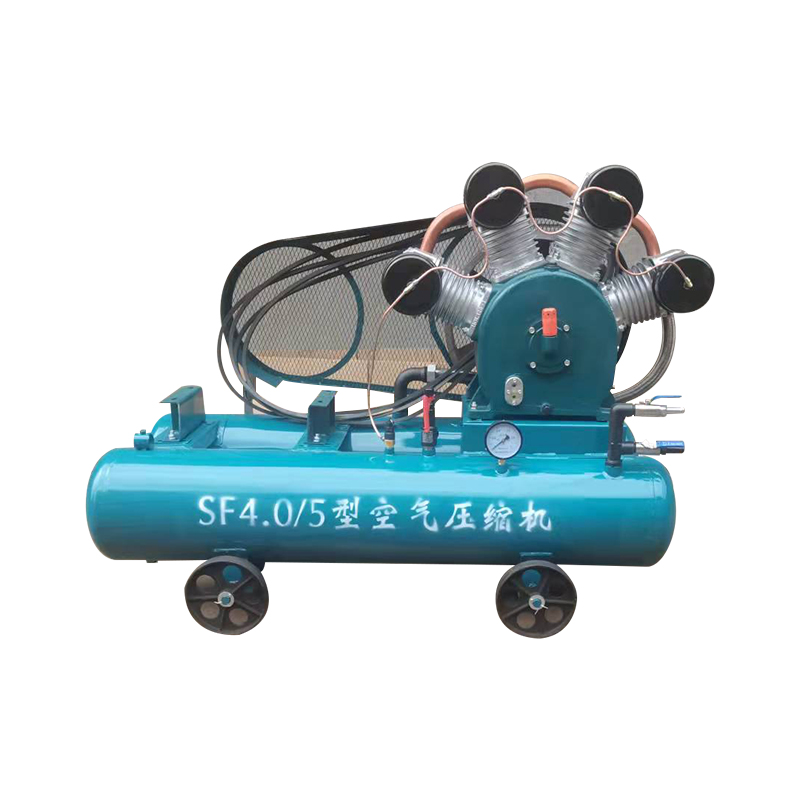
20KW Mining Diesel Piston Air Compressor SF4.0-5
Advantages Small in size,light in weight, easy to move Top material and superior technology Simple structure, high efficiency, good performance, and low price Adopt the most popula […]
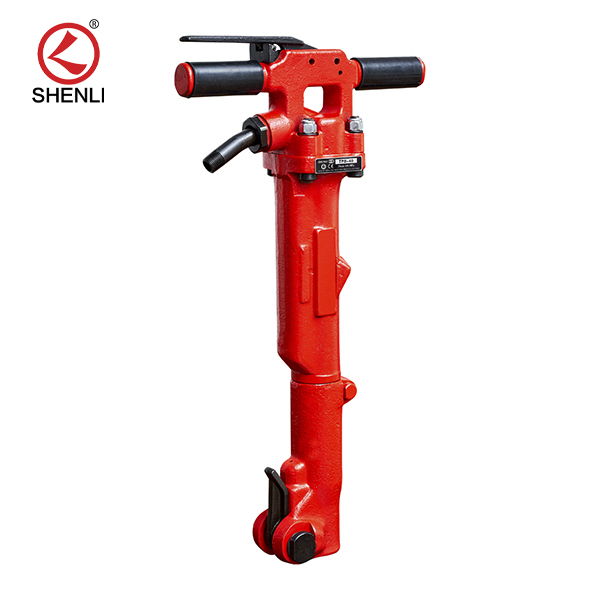
TPB40 Air Breaker Pavement Paving Breaker
Product introduction: Tpb-40 pneumatic crushing pick is a tool powered by compressed air.The compressed air is distributed to both ends of the cylinder block in turn to make the ha […]
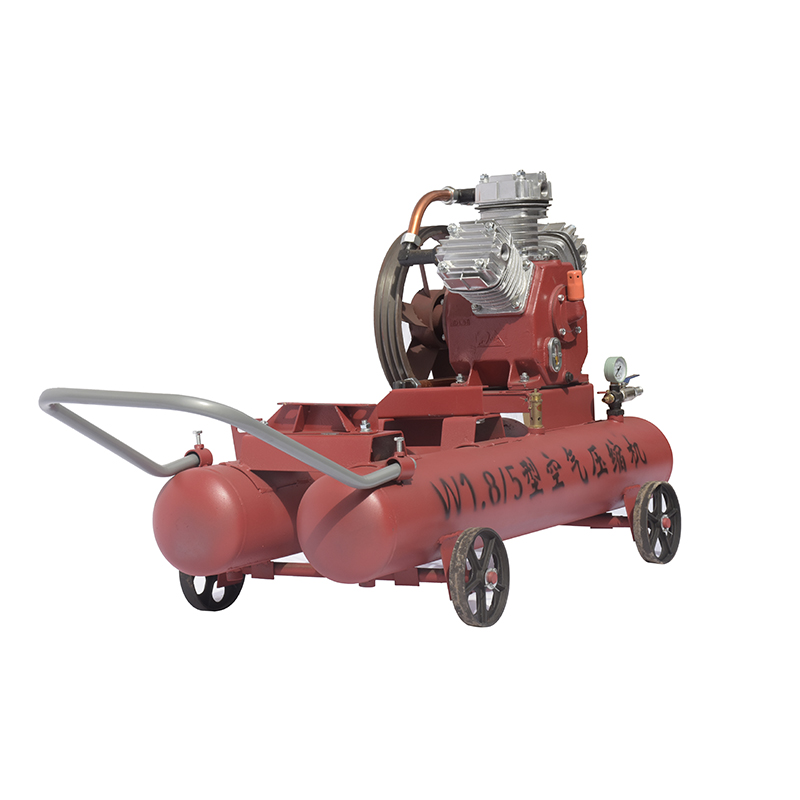
11KW Mining Diesel Piston Air Compressor W1.8-5
Diesel Portable Piston Air Compressor Mobile for Jack Hammer / Mining1.Simple structure,light weight,easy to move .2.Easy operating and maintenance.3.High quality air delivery.4.Su […]
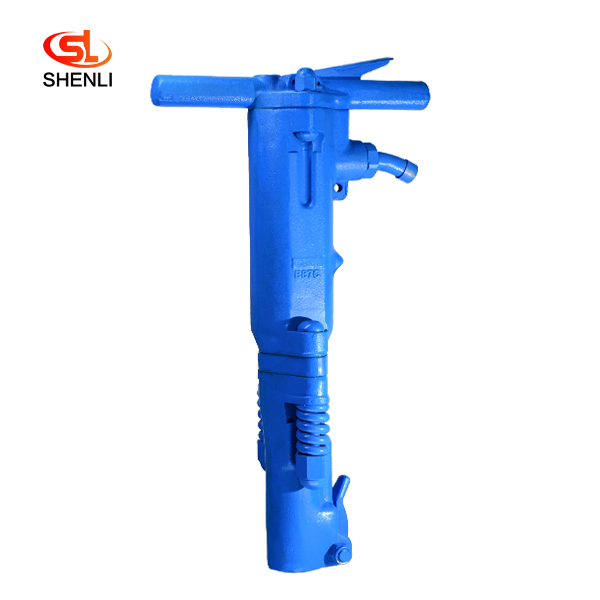
B87C Pneumatic Pick Air Shovel Cement Crusher
Product Description: The B87C crusher is made from Canada. Denver pneumatic Group company mature technology, with compressed air as a power crushing tool, can efficiently complete […]
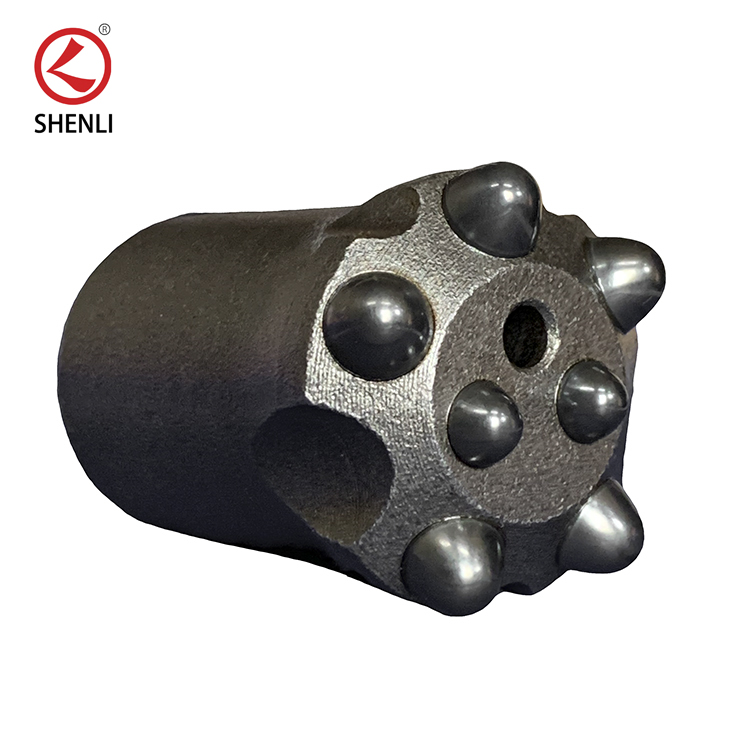
Rock Drill Button Bit
Product introduction: Taper bits, especially Tapered button bits are the most popular tapered drill bits with a wide selection of head diameters from 26mm to 48mm. With carbide but […]
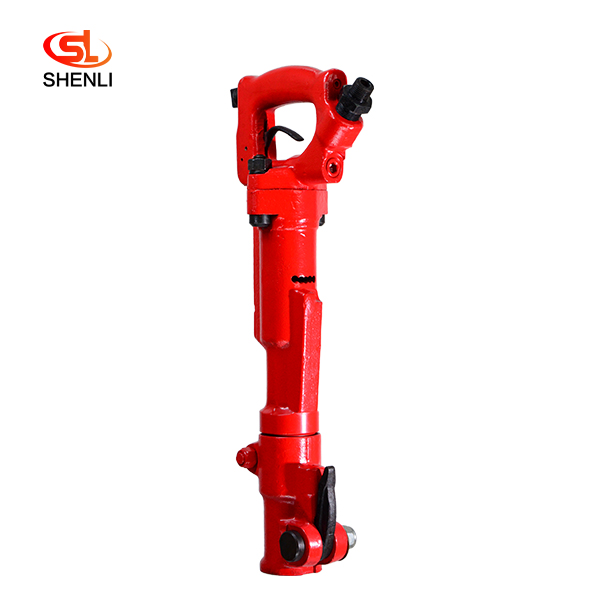
TCD20 Pneumatic Pick Air Shovel Cement Crusher Pneumatic Chipping Hammer
Product description: The TCD-20 pneumatic pick is powered by compressed air using Japan’s TOKU technology Crushing tools, features: lightweight, small size, large strike ener […]
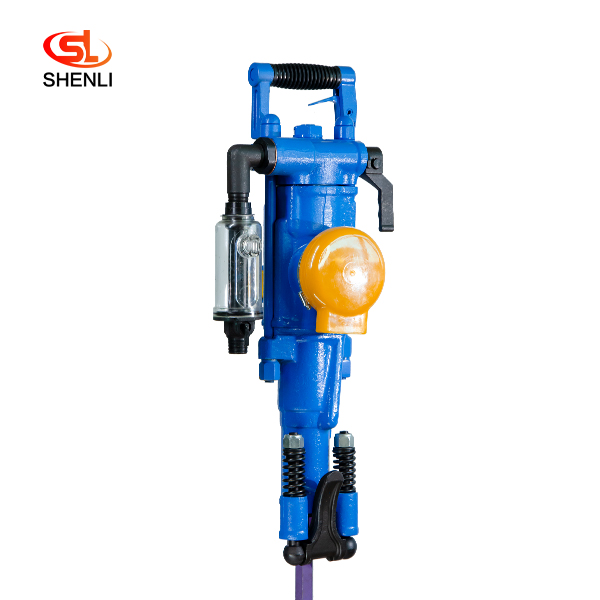
YT28 Pusher Leg Rock Drill
Short Description: The YT28 air-leg rock drill is a kind of high-efficiency, energy-saving and environmentally friendly rock drilling equipment. Compared with similar pneumatic pro […]
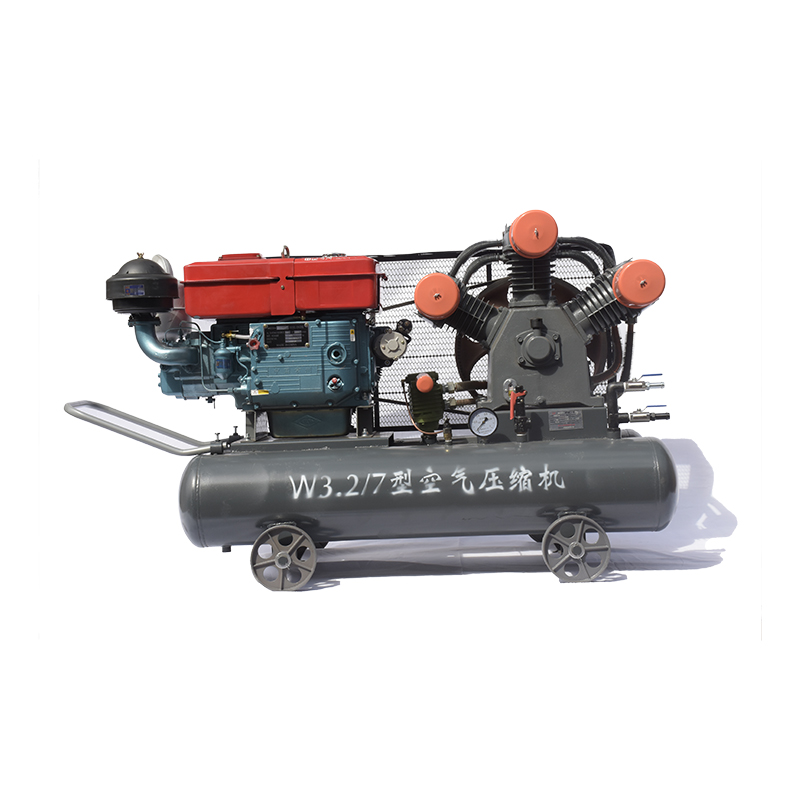
20KW Mining Diesel Piston Air Compressor W3.2-7
Advantages Small in size,light in weight, easy to move Top material and superior technology Simple structure, high efficiency, good performance, and low price Adopt the most popula […]