A compressed air system requires an air dryer, a device that works to decrease the moisture content in the air. By minimizing moisture, there is less risk of corrosion, cross-contamination, and equipment dysfunction. The dryer has the ability to manipulate the dew point of the compressed air, making it suitable for a variety of industrial processes.
For those seeking drier air, the most frequent answer is a refrigerated air dryer. These systems use refrigerant to lower the temperature of the air, thus causing the water droplets to condense and drain off. Then, to restore the original heat level of the air, it is heated back up before it is released. This process is often utilized for compressed air systems requiring a surprisingly profound dew point.
For environments demanding a low-dew point air source, desiccant air dryers offer an effective solution. These devices employ a desiccant, such as silica gel, to absorb moisture out of the air. Once charged with moisture, the desiccant is heated to release the water vapor into the surrounding atmosphere – which is then typically drained away.
A quick way of lessening the pressure of condensed air is by using an air dryer. By allowing some air to escape, the remaining air will force through its compression, leaving a steady low-pressure flow that can be harnessed for industrial needs.
When selecting an air dryer, you must take into account the kind of compressor in use. Desiccant dryers are suitable for oil-lubed compressors, while refrigerated ones are necessary for oil-free models. Likewise, the size of the air dryer should match the size of the compressor; opting for a bigger air dryer if you want greater efficiency from a larger compressor.
When considering an application, it is essential to consider the dew point as needed. Refrigerated air dryers commonly reach dew points extending from -40F to -100F, while desiccant air dryers can achieve dew points in the range between -20F and -100F.
All things considered, the energy efficiency of an air dryer should definitely be taken into account. Even though purchasing an air dryer in the first place is a rather considerable investment, you could end up saving quite a bit with a higher efficiency model in the long run, as they require substantially less energy to operate. Though the more efficient ones can cost extra, this fee is more than made up for in energy cost savings.
Ultimately, an air dryer is essential for any compressed air system. To ensure efficiency and reliability of the compressed air system, the right type of air dryer should be selected with regards to its dew point requirements, energy efficiency, as well as the size of the system. When all criteria are matched correctly, machinery and any connected products will remain safeguarded against contamination while keeping the system operating correctly.
All manner of compressed air systems rely on an Air Dryer for Compressor to safeguard efficiency by eliminating moisture and other impurities. This results in a purer source of air, enhancing the longevity of the compressor and keeping it in optimal condition. In this article, we will analyze different varieties of compressor air dryers and how they operate, allowing us to enjoy a high-quality, purified air supply.
A wide range of air dryers exist, with desiccant, regenerative, and membrane drying systems being the main types. Desiccant breathing systems are the most popular and employ a desiccant substance to extract moisture from the air. This is done by subjecting it to intense heat which causes the vaporized dampness to detach from the material and dissipate through the atmosphere. When it reaches the optimal temperature, it cools down before being released for use. Because of its ability to create sterile and moisture-free air, this sort of dryer is often employed in medical facilities as well as industrial settings.
Passing through a filter warmed by the heat, moisture is extracted from the air by the filter media of a regenerative air dryer. This removes impurities and leaves only the dry air, suitable for use in industrial and commercial settings. The result is high-quality, hygienic air that keeps machinery running smoothly.
To condition the air for certain purposes, a membrane air dryer is often employed. Water molecules are passed through a semi-permeable membrane to create a clean, moisture-free atmosphere, allowing only the water particles to go through. A dry state is thus produced in seconds, ready for use and fit for medical and industrial contexts when it is essential to have a dry environment.
In order to choose the correct air dryer for a compressor, certain factors must be taken into account, for example, the dimensions of the compressor, the kind of air that will be employed, and the environment it is being situated in. Furthermore, the cost of the air dryer itself must also be considered, as it tends to be costly both to buy and maintain. Ultimately, however, deciding on an appropriate model should come down to what is needed for the specific application in question and the type of air supplied.
From desiccant to regenerative and membrane, air dryers come in a range of different types and are an unavoidable component of any condensed air system. Selecting the most suitable model is critical for not only maximizing compressor operation efficacy but also lengthening its life-span. After all, the correct air dryer permits the compressor to provide a cleancut, dry air supply at optimal performance over prolonged periods.
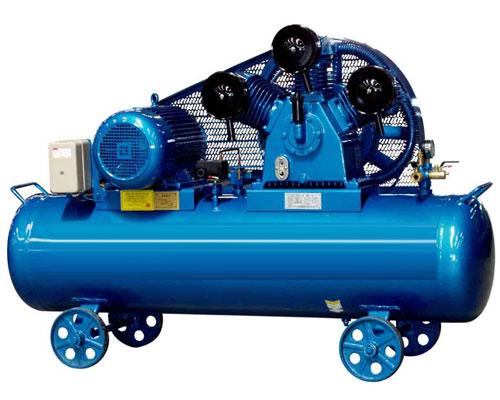
Related Product
Warning: Use of undefined constant rand - assumed 'rand' (this will throw an Error in a future version of PHP) in /www/wwwroot/www.sunritamachinery.com/wp-content/themes/msk5/single.php on line 69
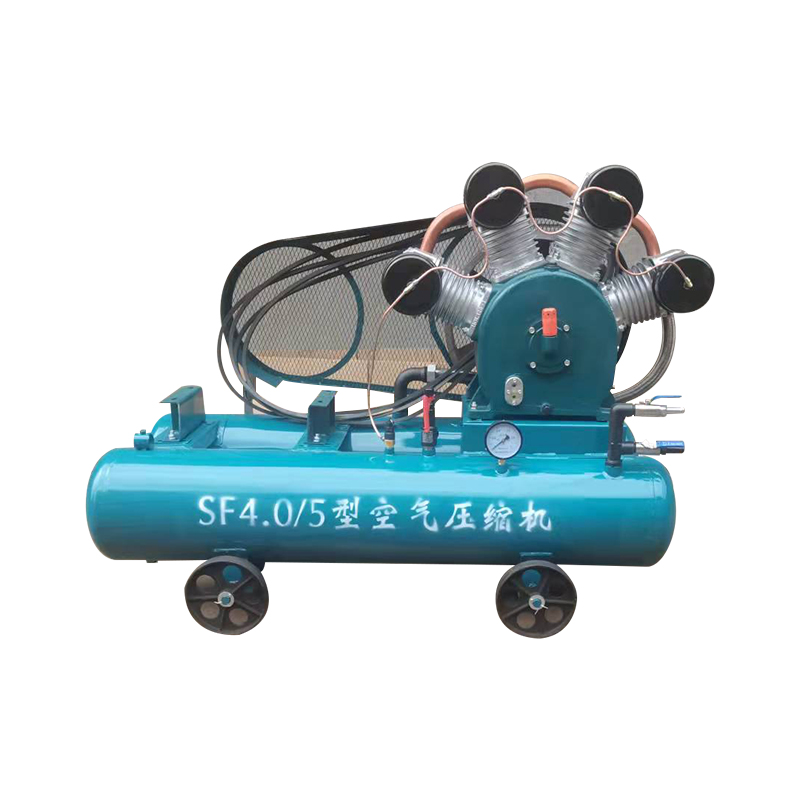
20KW Mining Diesel Piston Air Compressor SF4.0-5
Advantages Small in size,light in weight, easy to move Top material and superior technology Simple structure, high efficiency, good performance, and low price Adopt the most popula […]
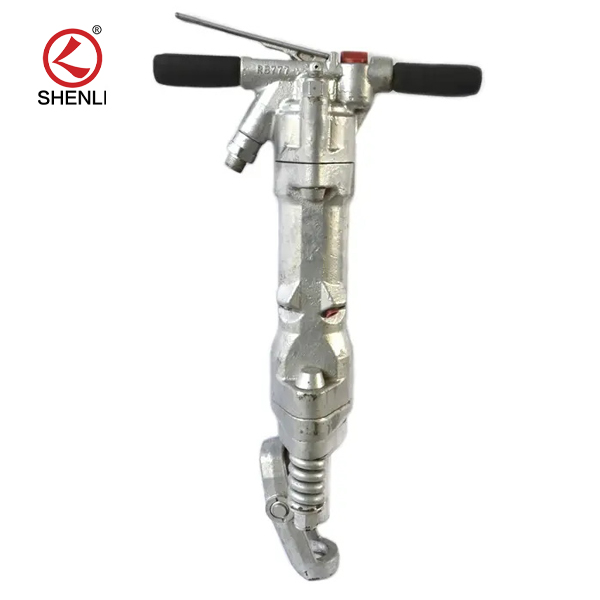
RB777 Pneumatic Pick Air Shovel Cement Crusher Pneumatic Chipping Hammer
Product description: RB777 pneumatic picks are used to build roads, install works of broken concrete and other hardens Hard object tools, the machine structure is simple, high effi […]
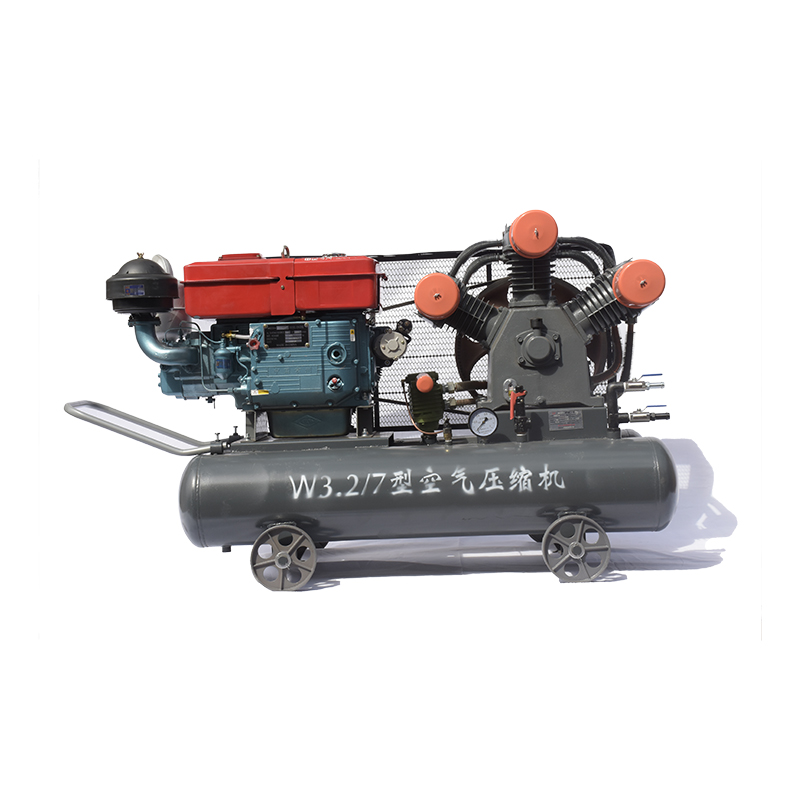
20KW Mining Diesel Piston Air Compressor W3.2-7
Advantages Small in size,light in weight, easy to move Top material and superior technology Simple structure, high efficiency, good performance, and low price Adopt the most popula […]
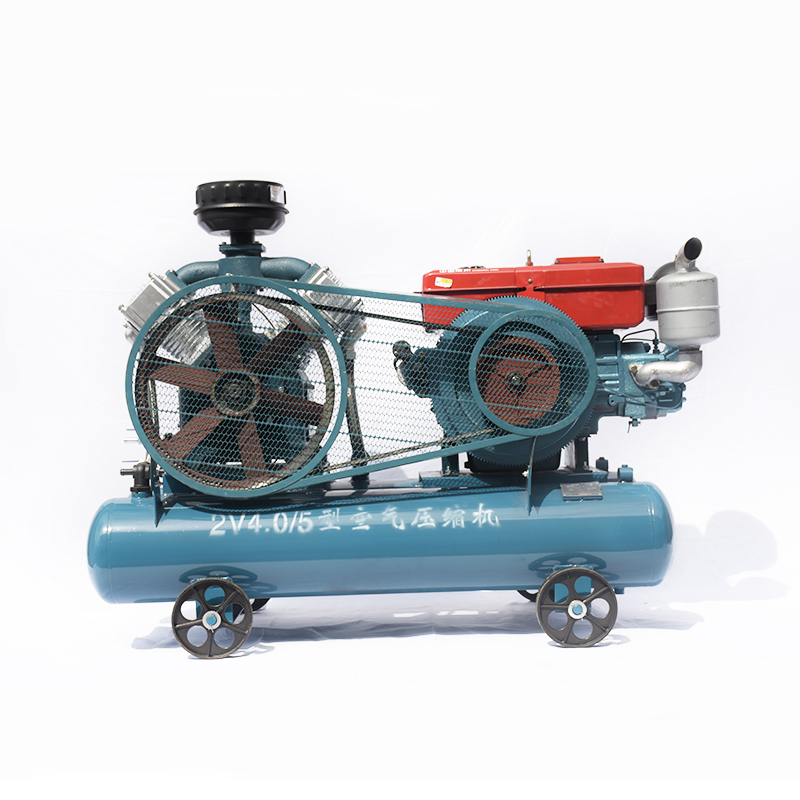
20KW Mining Diesel Piston Air Compressor 2V4.0-5
Double Air Tank Diesel Portable Best-Selling Engine Oil Piston Air Compressor are mainly used to supply stable and clean compressed air to the pneumatic tools and keep them working […]
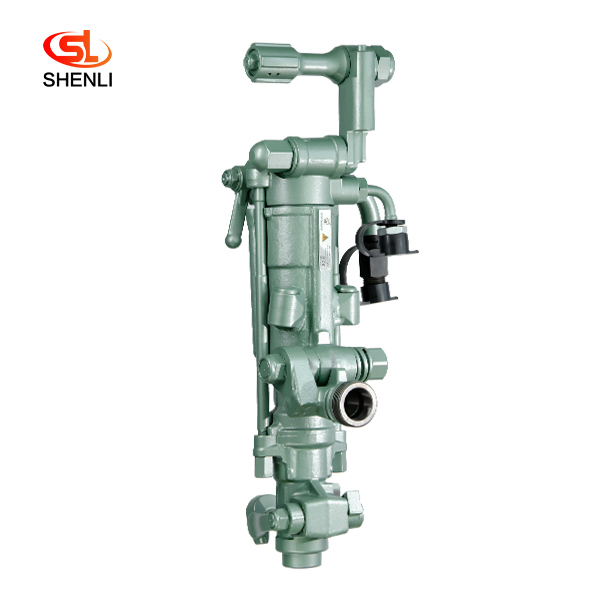
S250 Air Leg Pneumatic Rock Drill Pusher Leg Rock Drill
Product description: (S250 jackleg Drill) has been the preferred choice of miners who demand high performance, superior control and lasting reliability. the S250 jackleg allows ope […]
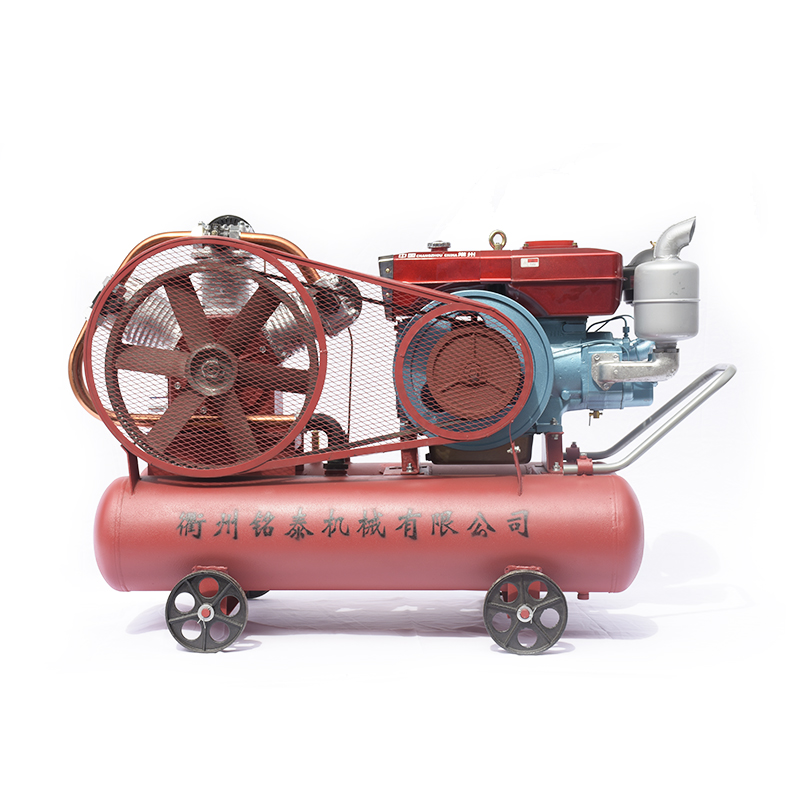
18.5KW Mining Diesel Piston Air Compressor W3.0-5
Advantages Small in size,light in weight, easy to move Top material and superior technology Simple structure, high efficiency, good performance, and low price Adopt the most popula […]
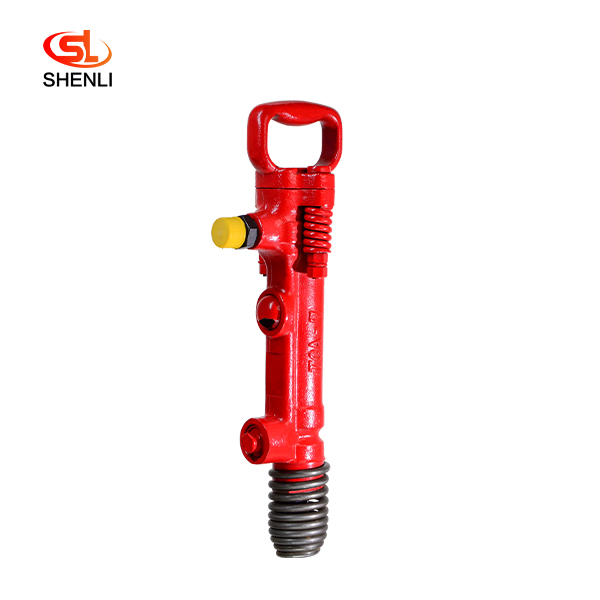
TCA7(G7)Pneumatic Pick Air Shovel Cement Crusher Pneumatic Chipping Hammer
Product introduction: Adopted Japan’s Toku technology, the air picks with proven forging technology are durable, lightweight and good performance, and easy to operate. Mainly […]
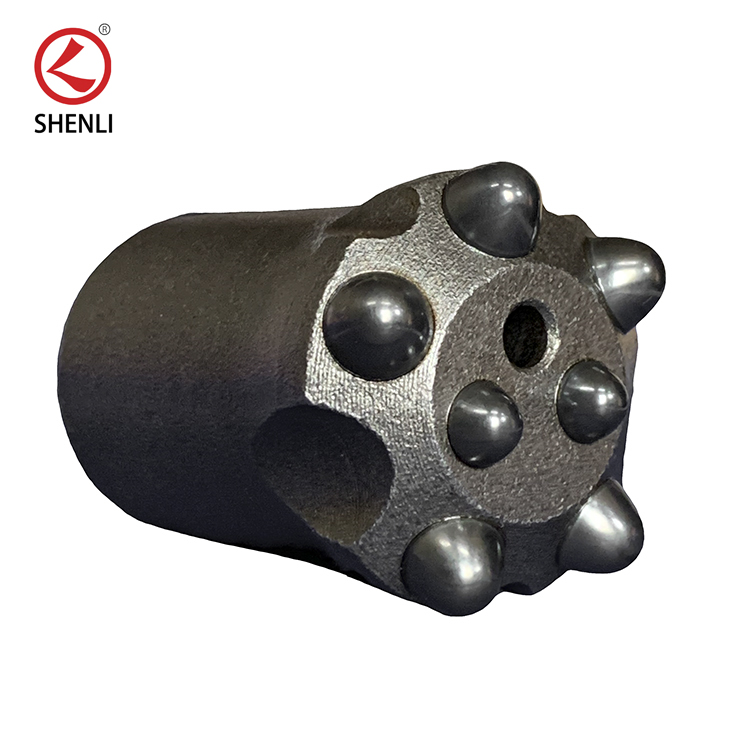
Rock Drill Button Bit
Product introduction: Taper bits, especially Tapered button bits are the most popular tapered drill bits with a wide selection of head diameters from 26mm to 48mm. With carbide but […]
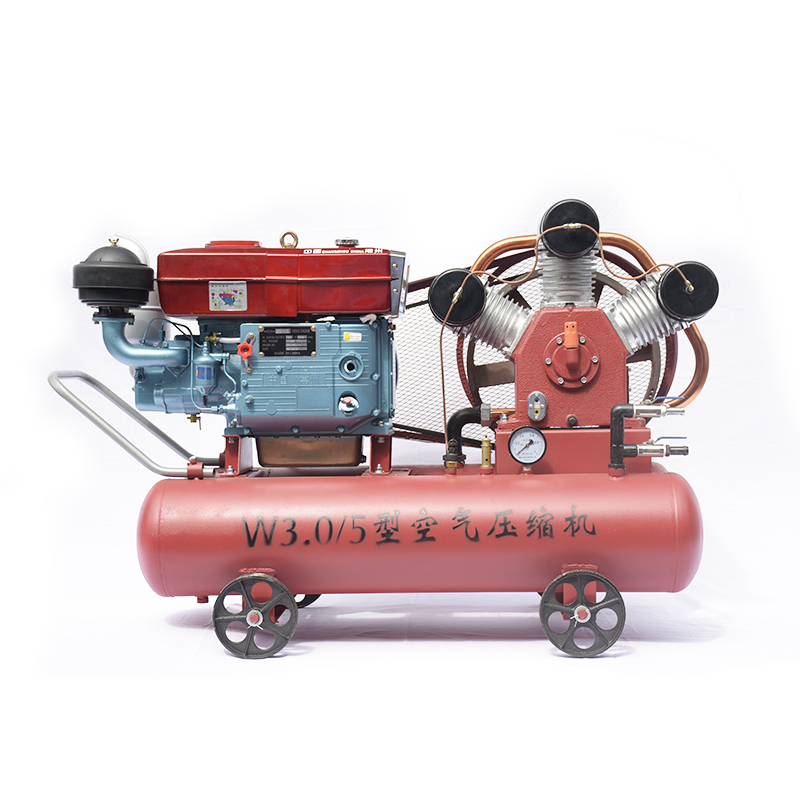
15kW Mining Diesel Piston Air Compressor W3.0-5
Diesel Portable Piston Air Compressor Mobile for Jack Hammer / Mining 1.Simple structure,light weight,easy to move . 2.Easy operating and maintenance. 3.High quality air delivery. […]