As a mainstay of many enterprises and homesteads, air compressors offer an incredible amount of power to carry out tasks and drive machinery. Despite their capability, these machines can suffer from a selection of issues due to their complex arrangement – but don’t worry! In this piece, we’re going over some of the most commonly encountered issues with air compressors and techniques to address them.
The air pressure generated by an air compressor is sometimes too low for tools and machinery to work effectively. The simplest way to address this would be to inspect the air pressure regulator. If it’s set too low, then it can be adjusted to a more suitable level. But if the pressure remains inadequate, the intake filter and check valve may not be functioning properly, thus necessitating a professional repair job.
An air leak from the compressor can have many origins – which might include faulty gaskets, a worn hose connection, or a broken compressor head. To take care of this problem, the user needs to inspect all hoses and connections for any possible wear and tear. Alternatively, if it turns out that the compressor head has cracked, then it must be replaced.
The third concern could be the humming from a worn compressor. This can be attributed to defective components or a possible snag with the motor. People should assess the motor and change any dilapidated parts to fix this hitch. Noises coming from the compressor itself may be due to an excess of debris and dust. In this scenario, people should remove contaminants inside the compressor and latch on fresh components if needed.
If the compressor is heating up, the air intake filter might be blocked or it might be lacking in lubrication. To resolve the issue, inspect the air filter and replace it if required. Additionally, ensure any necessary lubricants are topped off to avoid further overheating.
The fifth issue points to inadequate oil supply. This deficiency may happen due to a crack in the oil system or an absence of grease. To rectify the problem, the person must monitor the oil level and augment if it is beneath than the average. Same goes for the lubricant – one should observe the amount and fill if it does not suffice.
A conundrum of a faulty compressor hitting the brick wall of a non-starting system could be attributed to several underlying causes. It’s possible that a lack of power, an inoperative switch, or hitches in the motor may be behind the issue. For a successful resolution, one should initially scope out the power source, the switch, and the motor for any malfunctions. In the event of any of these components demonstrating signs of distress, they should immediately be changed out with new ones.
Your air compressor should be ready to serve you faithfully for years, given proper care and regular maintenance. If you are dealing with any issues related to your compressor in the meantime, engaging the expertise of a qualified technician is often the best way to go. They can accurately identify what the root of the issue is and suggest the most beneficial approach to its resolution. Here are a few of the most usual air compressor predicaments and solutions to keep in mind.
The reliability of air compressors is undeniably important for many businesses and industries due to the wide range of tasks these machines offer compressed air to. Unfortunately, several problems can arise, resulting in costly repairs or even requiring a full replacement. Here, we will explore these common air compressor issues and possible solutions.
If you’ve noticed a decrease in air pressure coming from your compressor, one of the primary issues to be aware of is a potential leak. Don’t hesitate to investigate further, as air can easily escape from the systems hoses or even the compressor itself. To begin, check for any worn, damaged, or faulty parts. Gaskets, hoses, and seals are usually first to be inspected and replaced if needed. For more serious leaks, you may need to take the compressor apart entirely to locate the source.
An overactive compressor can cause a host of issues, from debilitating equipment to hazardous scenarios. The origin of the excessive pressure can range from faulty pressure switches to blocked air filters. Resolve the problem by assessing its source and completing the required repairs.
When air compressors start losing oil, it’s important to take this seriously and take action fast. From worn gaskets to cracked piston seals, these machines can suffer from many different types of leaks. To get them running properly once more, the only option is to find the root of the problem and carry out repairs as quickly as possible.
Pressure-Sensitive Shortcomings
Problems with your air compressor turning on and off when it shouldn’t be? Chances are, it’s due to a faulty pressure switch. This piece of equipment is in charge of monitoring the compressor’s activity, so if it’s malfunctioning, you’ll experience a variety of complications. Fortunately, a new pressure switch should do the trick – all you need to do is switch out the faulty unit for a new one!
Air compressors may be prone to overheating, which can put them in a precarious situation if left unaddressed. Not only can this issue lead to damage of the machine, but it can also potentially create a hazardous situation. To resolve the problem, you must pinpoint the root cause and take steps towards repairing it.
Could your air compressor be malfunctioning? Most problems can be swiftly addressed if you catch them early. If you’ve been noticing some concerning issues, don’t wait – take action to protect yourself and your machinery from further suffering. Still stumped? Consult a seasoned technician for the help you need.
Post time: 2023-08-02Related Product
Warning: Use of undefined constant rand - assumed 'rand' (this will throw an Error in a future version of PHP) in /www/wwwroot/www.sunritamachinery.com/wp-content/themes/msk5/single.php on line 69
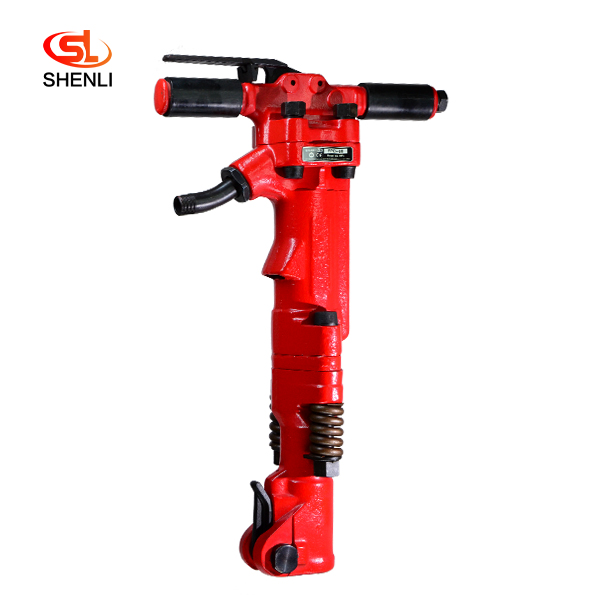
TPB6 Air Concrete Breaker Pneumatic Pick
Product introduction: TPB-60 crusher adopts the mature technology of TOKU Group, Is compressed air as the power of the crushing tool, can efficiently complete the reinforced concre […]
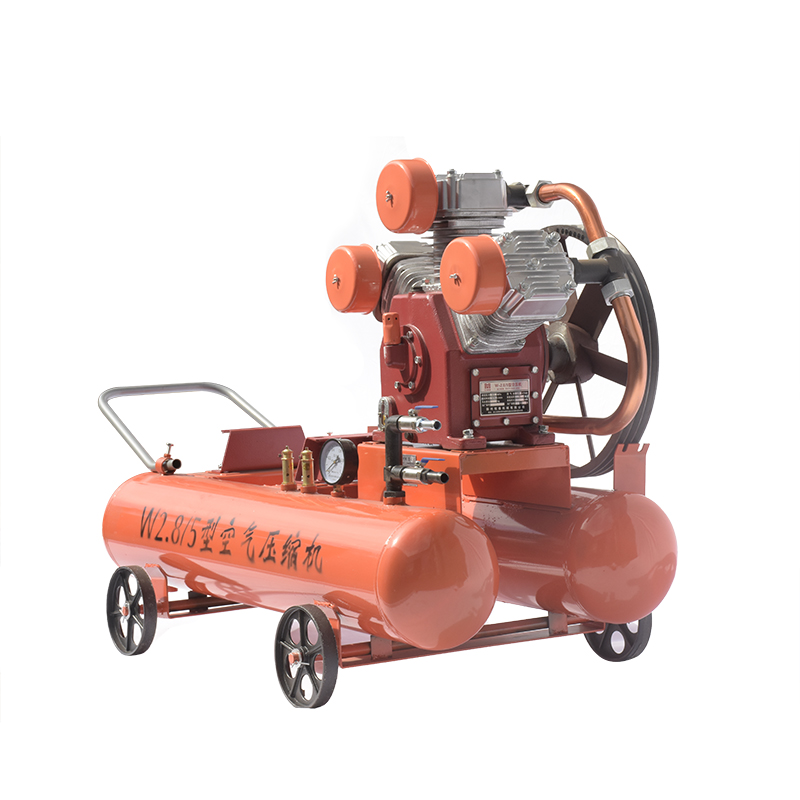
15KW Mining Diesel Piston Air Compressor W2.8-5
Diesel Portable Piston Air Compressor Mobile for Jack Hammer / Mining 1.Simple structure,light weight,easy to move . 2.Easy operating and maintenance. 3.High quality air delivery. […]
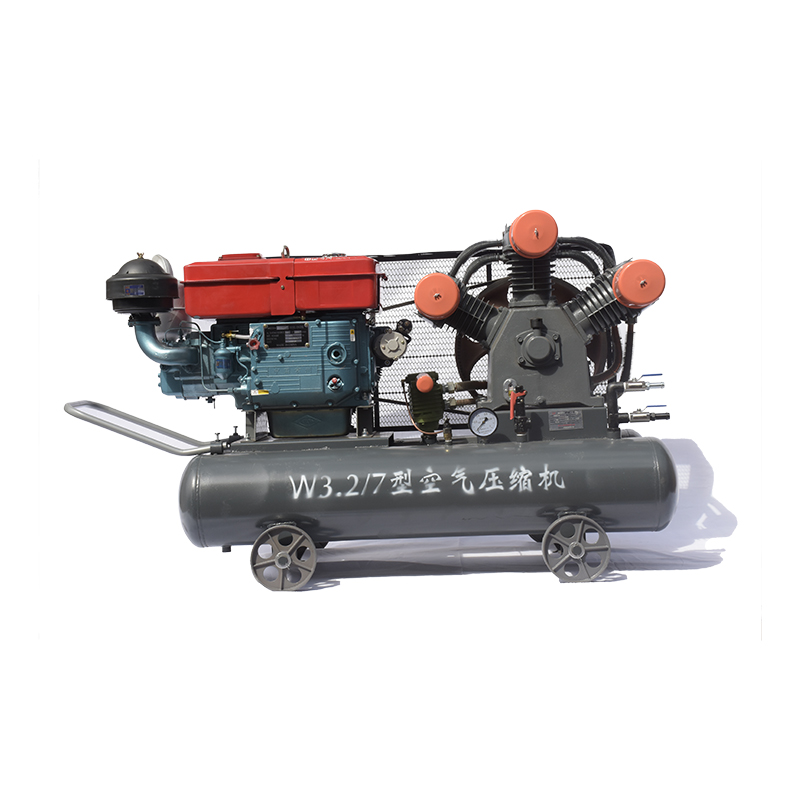
20KW Mining Diesel Piston Air Compressor W3.2-7
Advantages Small in size,light in weight, easy to move Top material and superior technology Simple structure, high efficiency, good performance, and low price Adopt the most popula […]
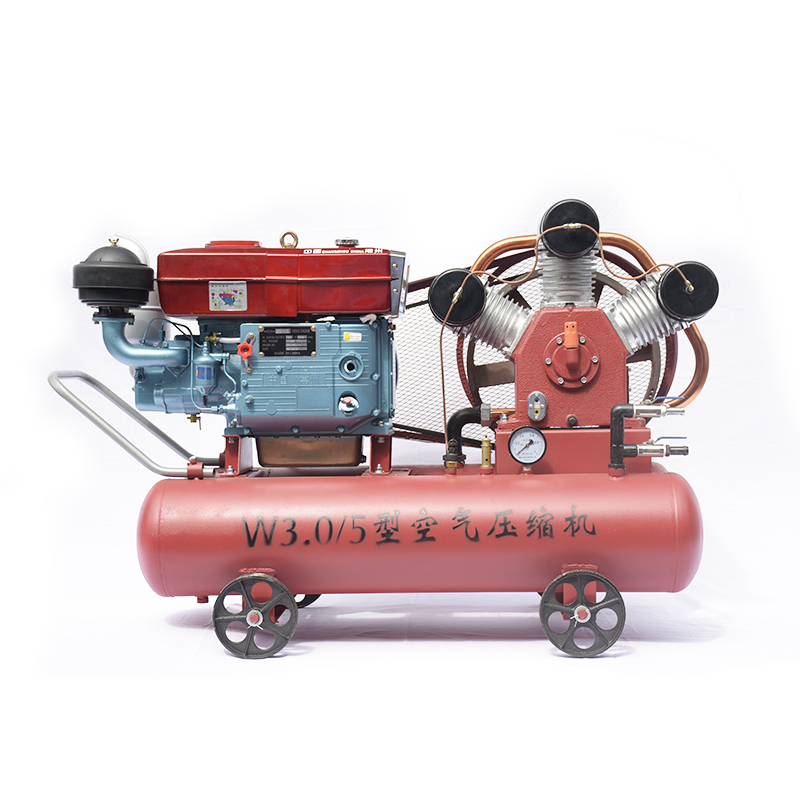
15kW Mining Diesel Piston Air Compressor W3.0-5
Diesel Portable Piston Air Compressor Mobile for Jack Hammer / Mining 1.Simple structure,light weight,easy to move . 2.Easy operating and maintenance. 3.High quality air delivery. […]
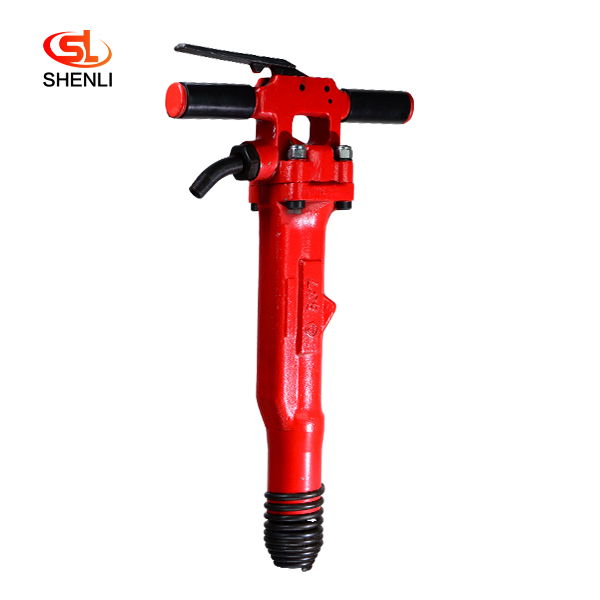
B37 Pneumatic Pick Air Shovel Cement Crusher Pneumatic Chipping Hammer
Product Description: B37 pneumatic crushing pick is a tool powered by compressed air. The compression the air is distributed to the two ends of the cylinder block in turn, so that […]
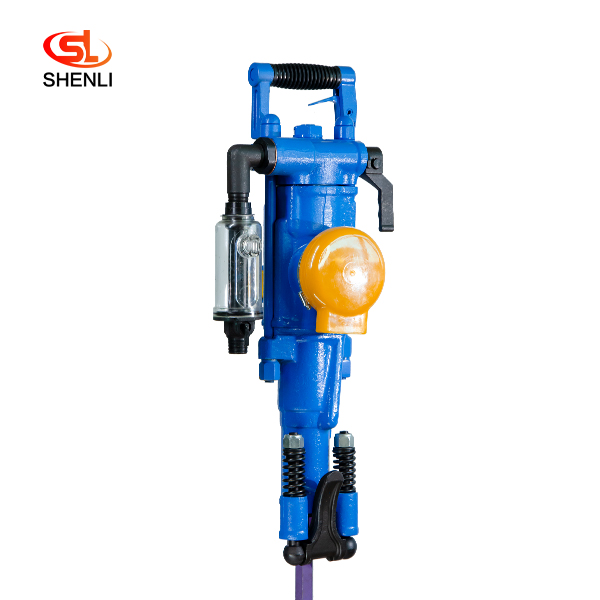
YT28 Pusher Leg Rock Drill
Short Description: The YT28 air-leg rock drill is a kind of high-efficiency, energy-saving and environmentally friendly rock drilling equipment. Compared with similar pneumatic pro […]
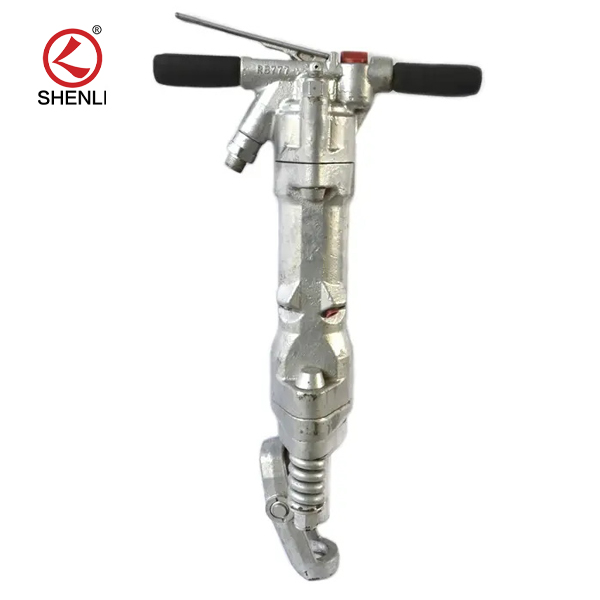
RB777 Pneumatic Pick Air Shovel Cement Crusher Pneumatic Chipping Hammer
Product description: RB777 pneumatic picks are used to build roads, install works of broken concrete and other hardens Hard object tools, the machine structure is simple, high effi […]
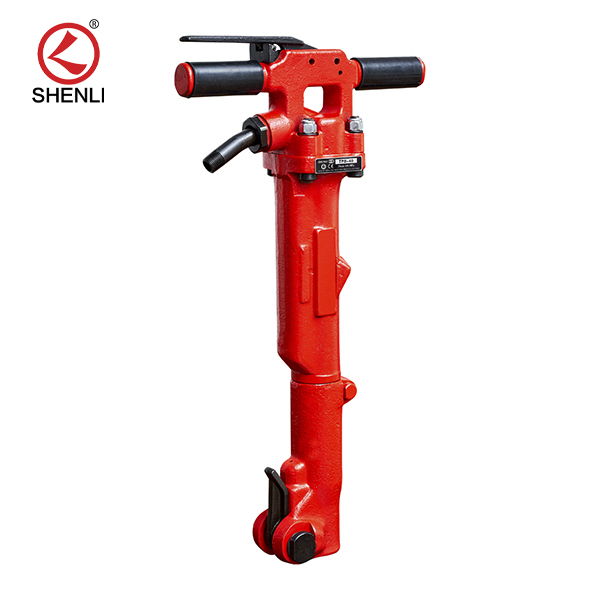
TPB40 Air Breaker Pavement Paving Breaker
Product introduction: Tpb-40 pneumatic crushing pick is a tool powered by compressed air.The compressed air is distributed to both ends of the cylinder block in turn to make the ha […]
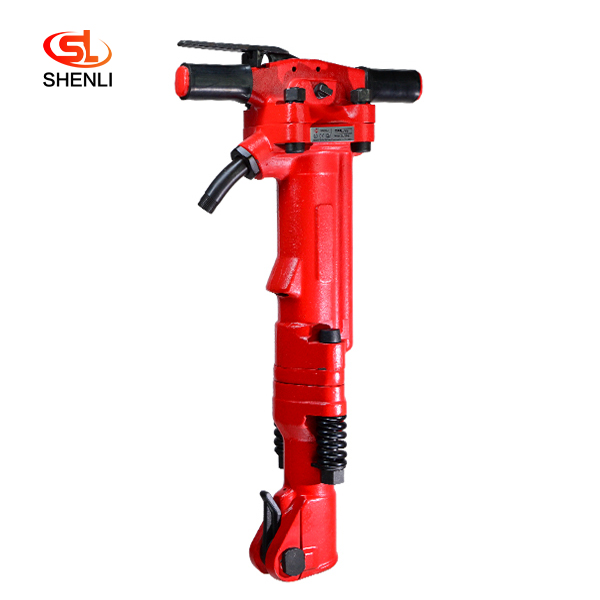
TPB90 Air Breaker Pavement Paving Breaker
Product introduction: TPB-90 crusher adopts the mature technology of TOKU Group, Is compressed air as the power of the crushing tool, can efficiently complete the reinforced concre […]