An air compressor is a workhorse, using an impressive motor to power its signature tool – one that sucks in air and compresses it. This compressed air is then stored in a tank for later use, supplying pressurized energy to power various devices and tools when the user requires it.
From a paint-sprayer to an impact wrench and beyond, compressed air is known to power an array of tools. To make the most of these tools, however, it is essential to invest in a properly-constructed piping system.
When crafting a piping system for an air compressor, one must weigh certain considerations. For example, it is important to think about the materials employed in the project, the layout of the installation, and any potential hose fittings necessary to complete the job. Additionally, the necessary pumping power to ensure smooth operation must be determined, as well as the safety precautions needed for a safe result. Lastly, the quality of components should be examined to guarantee a successful outcome. Crafting an efficient and reliable air compressor piping system is within reach with the right tools and resources.
1. To realize optimal efficiency of the compressor, ensure that the piping is of appropriate sizing. Its dimensions ought to be sufficient enough to manage the highest rate of CFM (cubic feet per minute) that the compressor is able to produce. Otherwise, if it is too tiny, a constricted air current will diminish machine performance.
If you’re seeking durable piping for your air compressor, copper, steel, and aluminum should be at the top of your list. These materials are capable of tolerating the powerful pressures and temperatures created by the compressor, so making use of any of them will be sure to secure your setup.
When it comes to air compressor systems, never underestimate the importance of proper fittings. These components are essential in maintaining the high temperatures and pressures generated by the compressor, and adequately connecting pipelines. Examples of fittings that are commonly used include elbow fittings, tee fittings, and union fittings.
For maximum durability and longevity, ensure that the piping for your air compressor system is suitably supported. You’ll need a variety of components, such as hangers, clamps, and brackets, to hold the system in place. This will guarantee that it won’t bow or break under its own weight.
Protect and preserve heat within the piping of your home by ensuring it is properly insulated. A combination of fiberglass and foam work well for this, serving as a barrier to deter any waning warmth or condensation.
To assure uncontaminated air is sent through the compressor, the piping must be kept as pristine as possible. To accomplish this, each air compressor system needs to have a filter put in place in order to eliminate the presence of any impurities.
For the preservation of your own safety, proper safety measures should be taken when constructing a piping system. Make sure its design allows it to run securely and without danger. Additionally, a safety valve is crucial for any air compressor piping system; if a malfunction were to occur, the valve is able to promptly release the built-up pressure.
To ensure sustained functionality, your compressor piping apparatus must have an established maintenance regimen that is rigorously adhered to. Albeit tedious, regular inspection and maintenance of the system is vital in order to avoid any unfortunate incidents or unforeseen trouble.
The installation of an air compressor piping system can range from basic to intricate, depending on the demands of the intended use. To guarantee an uninterrupted, efficient experience, ensure that your air compressor piping system is installed correctly following these pointers. This will ensure years of flawless performance.
Post time: 2023-06-22Related Product
Warning: Use of undefined constant rand - assumed 'rand' (this will throw an Error in a future version of PHP) in /www/wwwroot/www.sunritamachinery.com/wp-content/themes/msk5/single.php on line 69
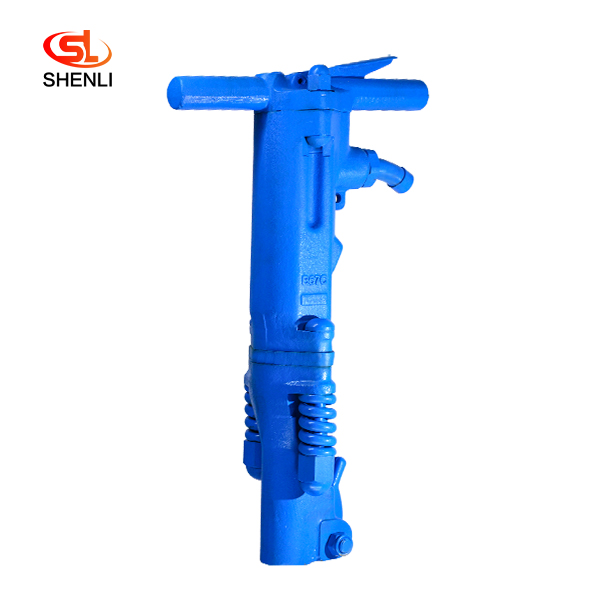
B67C Pneumatic Chipping Hammer
Product description: The B67C crusher is made from Canada. Denver pneumatic Group company mature technology, with compressed air as a power crushing tool, can efficiently complete […]
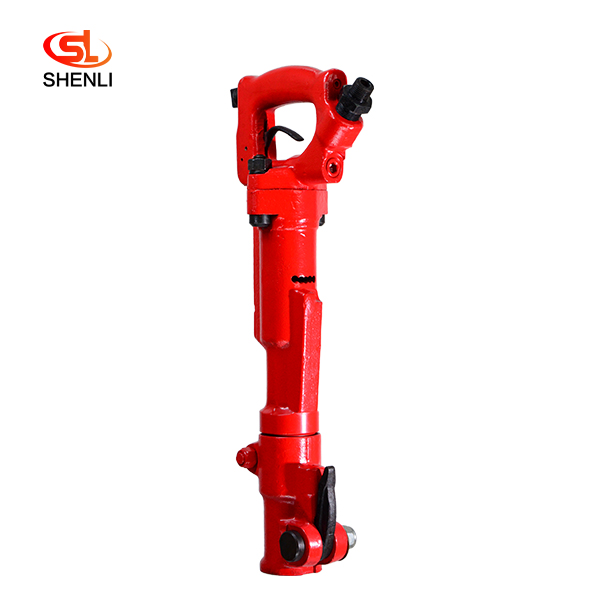
TCD20 Pneumatic Pick Air Shovel Cement Crusher Pneumatic Chipping Hammer
Product description: The TCD-20 pneumatic pick is powered by compressed air using Japan’s TOKU technology Crushing tools, features: lightweight, small size, large strike ener […]
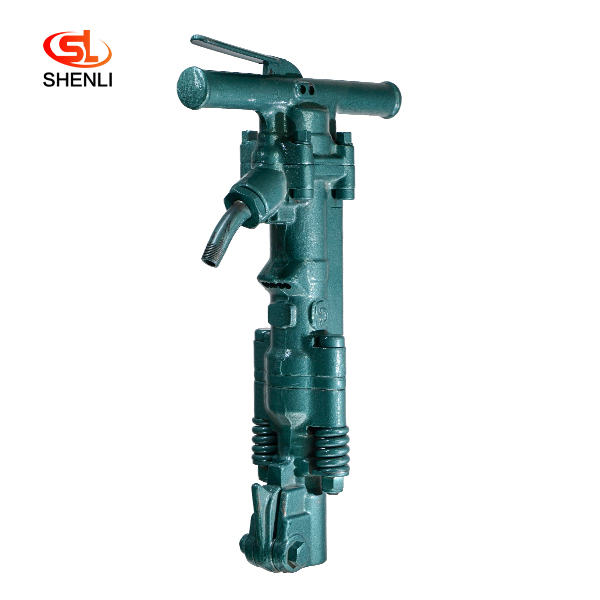
B47 Pneumatic Pick Air Shovel Cement Crusher Pneumatic Chipping Hammer
Product Description: B47 crusher adopts the mature technology of American Gardner Denver Pneumatic Group Company,It is a crushing tool powered by compressed air, which can finish r […]
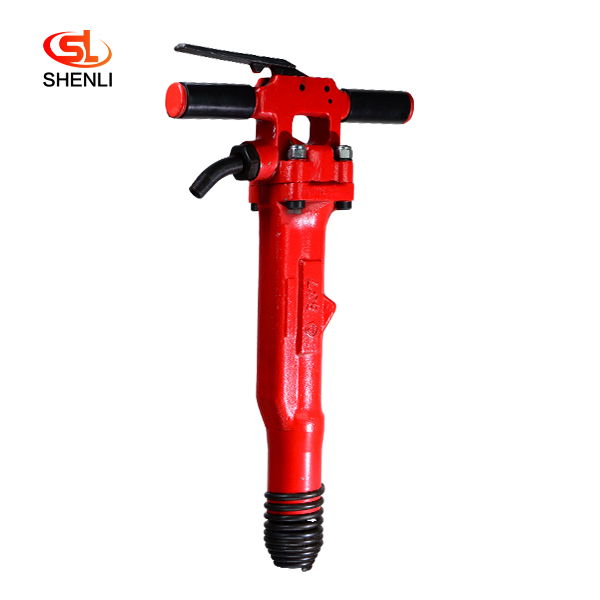
B37 Pneumatic Pick Air Shovel Cement Crusher Pneumatic Chipping Hammer
Product Description: B37 pneumatic crushing pick is a tool powered by compressed air. The compression the air is distributed to the two ends of the cylinder block in turn, so that […]
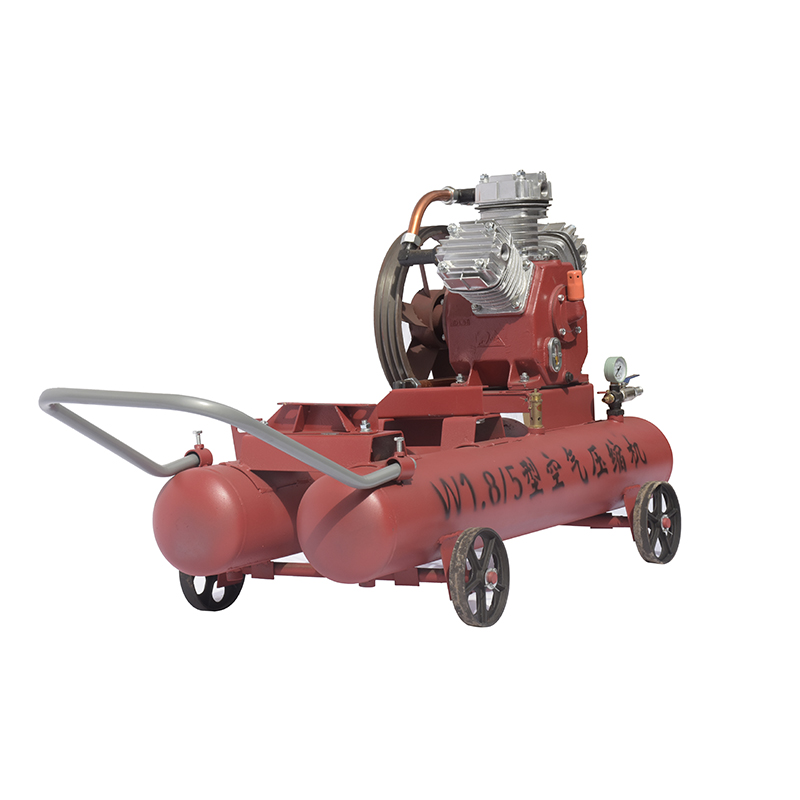
11KW Mining Diesel Piston Air Compressor W1.8-5
Diesel Portable Piston Air Compressor Mobile for Jack Hammer / Mining1.Simple structure,light weight,easy to move .2.Easy operating and maintenance.3.High quality air delivery.4.Su […]
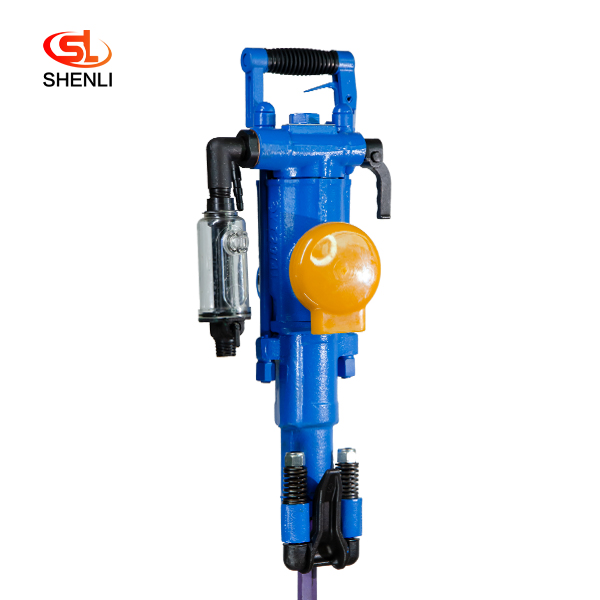
YT29A Air Leg Pneumatic Rock Drill
Short Description: YT29A air-legged rock drills are heavy-duty push-leg (air-legged) rock drills with low energy consumption, which are more suitable for drilling horizontal or inc […]
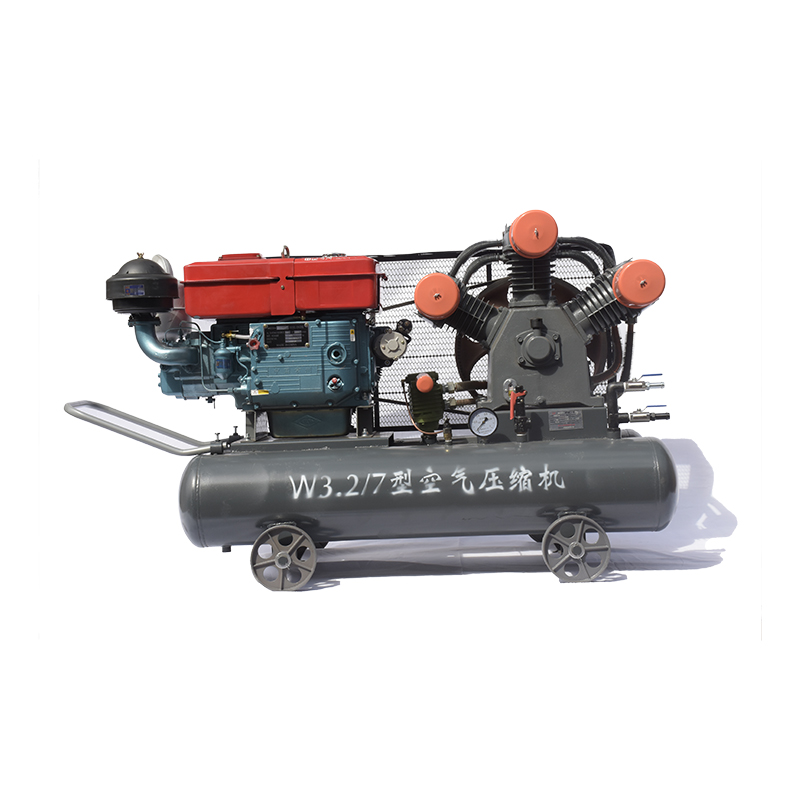
20KW Mining Diesel Piston Air Compressor W3.2-7
Advantages Small in size,light in weight, easy to move Top material and superior technology Simple structure, high efficiency, good performance, and low price Adopt the most popula […]
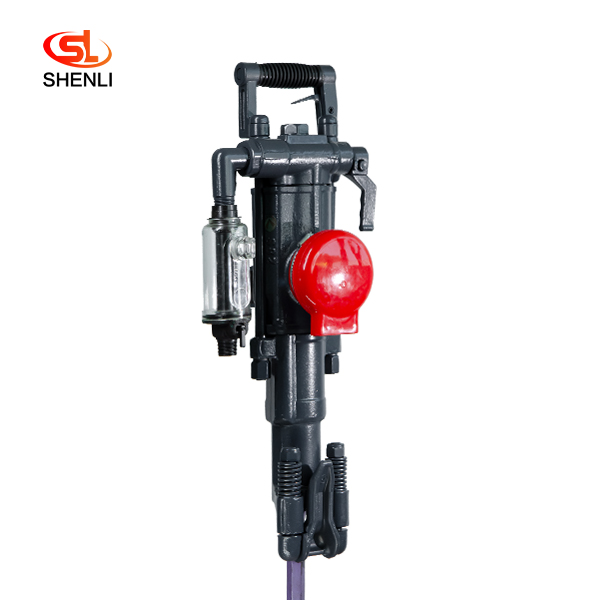
S82 Air Leg Pneumatic Rock Drill Pusher Leg Rock Drill
Scope of application: Model S82 air-legged rock drills are heavy-duty air-legged rock drills with high efficiency and low consumption, which are especially suitable for use in the […]
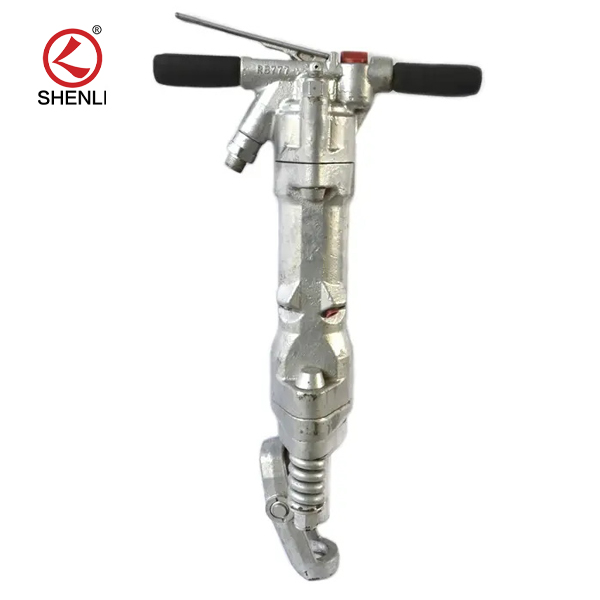
RB777 Pneumatic Pick Air Shovel Cement Crusher Pneumatic Chipping Hammer
Product description: RB777 pneumatic picks are used to build roads, install works of broken concrete and other hardens Hard object tools, the machine structure is simple, high effi […]