When Your Air Compressor Ceases to Function: Causes, Solutions, and Tips for Successful Maintenance
From factories to households, air compressors are used far and wide – they serve essential roles in powering pneumatic tools, filling tyres, and serving as a source of air for painting and other tasks. However, internal problems can cause these devices to fail and lead to costly delays, as well as extreme frustration. In this article, we delve into causes of air compressor failure, suggest easy fixes, and provide maintenance advice to help you keep your compressor running smoothly.
Unearthing the Source of Air Compressor Malfunctions
If you are experiencing problems with your air compressor, inadequate lubrication could very well be the cause. Without proper grease, wear and tear increases, the formation of rust expedites, and it becomes extremely difficult for any of the components to move as they should. An ignored oil change regimen endangers the condition of the entire pump and may even lead to an irreversible shutdown.
Without routine care and servicing, air compressors can suffer from the deleterious effects of accumulated dust, dirt, and debris. Such a buildup can lead to blockages inside the equipment as well as potential damage to its valves, pistons, and other parts. In extreme instances, a complete overhaul may be needed to recover the air compressor’s original condition.
Furthermore, the air compressor can face operational issues when confronted by an electrical fault. Not only can a power supply that is not steady reduce the machine’s overall performance, but it may halt abruptly or fail to generate enough pressure. Abysmal ventilation, considerable heat levels, and ill-suited fuses or circuits can have a pernicious influence on the compressor’s electrical system and its capability to operate correctly.
When functioning properly, the air pressure switch of an air compressor helps determine when to switch the machine on or off based on the pressure levels. Unfortunately, a faulty or aged pressure switch can cause the compressor to malfunction and can even lead to motor burnouts and pump failures. This is because if incorrectly calibrated or damaged, it may cause the unit to operate without pause, leading to overheating.
Strategies for Diagnosing and Resolving Air Compressor Dysfunction
Keeping an air compressor functional again may require a few solutions if the problem is found to be corrupted or lacking in oil. To start, replacing the dark, used oil with new, high-quality oil of the manufacturer’s specified formula should be done. Additionally, making sure to continuously monitor and supplement the oil levels is vital in order to avoid any further complications.
If your air compressor seems to be blocked, then chances are dirt has accumulated and is causing the issue. To solve the problem, a good cleaning is recommended – compressed air or a vacuum cleaner should do the trick. Take the time to properly clean the motor, intake filters, and any other components for optimal airflow.
Ensuring that the air compressor has sufficient voltage is key. Inspect the wiring, fuses, and circuits to verify that they are operational. Keeping the machine within its allotted capacity and avoiding overtaxing it is likewise vital to avoiding overheating and electrical problems.
To maintain the peak performance and longevity of the air compressor, a damaged or worn-out pressure switch should be promptly replaced with a new one that is compatible with the model and specifications of the air compressor. Otherwise, significant damage may be caused by a faulty switch.
Maximizing Air Compressor Performance Through Proper Upkeep
To maintain the longevity and efficacy of an air compressor, it is essential to carry out customary maintenance practices, like:
1. Monitoring Oil Levels and Quality – A Daily Necessity
Every 500 hours of use or according to manufacturer regulations, the oil in the machine needs to be replaced with freshly-drained oil.
It is important to ensure that the air compressor is kept in pristine condition on a regular basis- this includes wiping away dirt, dust, and other particles.
Examining the hoses, joints, and faucets for any dripping or seeping, and ensuring they are firmly tightened if necessary.
Keeping an eye out for dirty or clogged air filters and replacing them as and when needed.
Gauging the force of the pressure switch to make certain it is functioning appropriately.
Routinely tracking the heat and force of the air compressor is essential for its proper functioning.
Ultimately, neglected maintenance, lack of lubrication, faulty electricals, and a malfunctioning pressure switch can contribute to air compressor breakdowns. By being mindful of these issues and purchasing cleverly, downtime, repair costs and wear-and-tear can be minimized significantly. But don’t forget: the secret to a dependable air compressor lies in its maintenance. With the guidance in this article, operators can optimize performance and feel more protected against potential air compression bankruptcies.
Post time: 2023-05-28Related Product
Warning: Use of undefined constant rand - assumed 'rand' (this will throw an Error in a future version of PHP) in /www/wwwroot/www.sunritamachinery.com/wp-content/themes/msk5/single.php on line 69
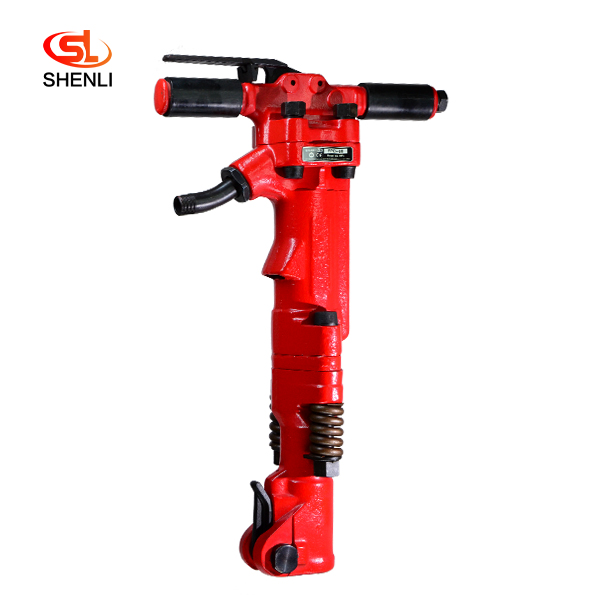
TPB6 Air Concrete Breaker Pneumatic Pick
Product introduction: TPB-60 crusher adopts the mature technology of TOKU Group, Is compressed air as the power of the crushing tool, can efficiently complete the reinforced concre […]
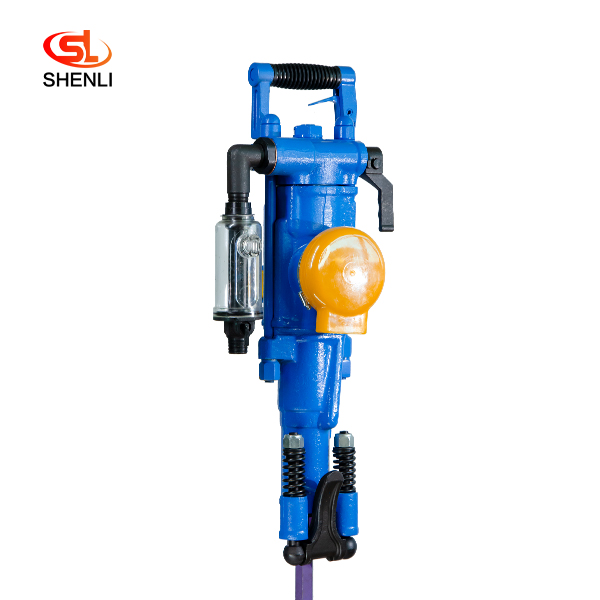
YT28 Pusher Leg Rock Drill
Short Description: The YT28 air-leg rock drill is a kind of high-efficiency, energy-saving and environmentally friendly rock drilling equipment. Compared with similar pneumatic pro […]
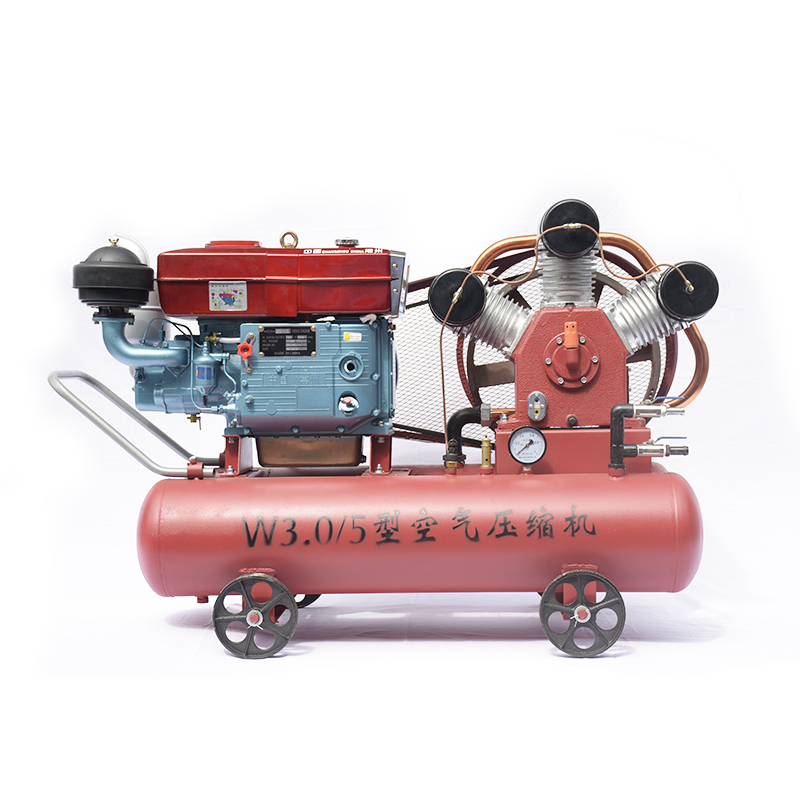
15kW Mining Diesel Piston Air Compressor W3.0-5
Diesel Portable Piston Air Compressor Mobile for Jack Hammer / Mining 1.Simple structure,light weight,easy to move . 2.Easy operating and maintenance. 3.High quality air delivery. […]
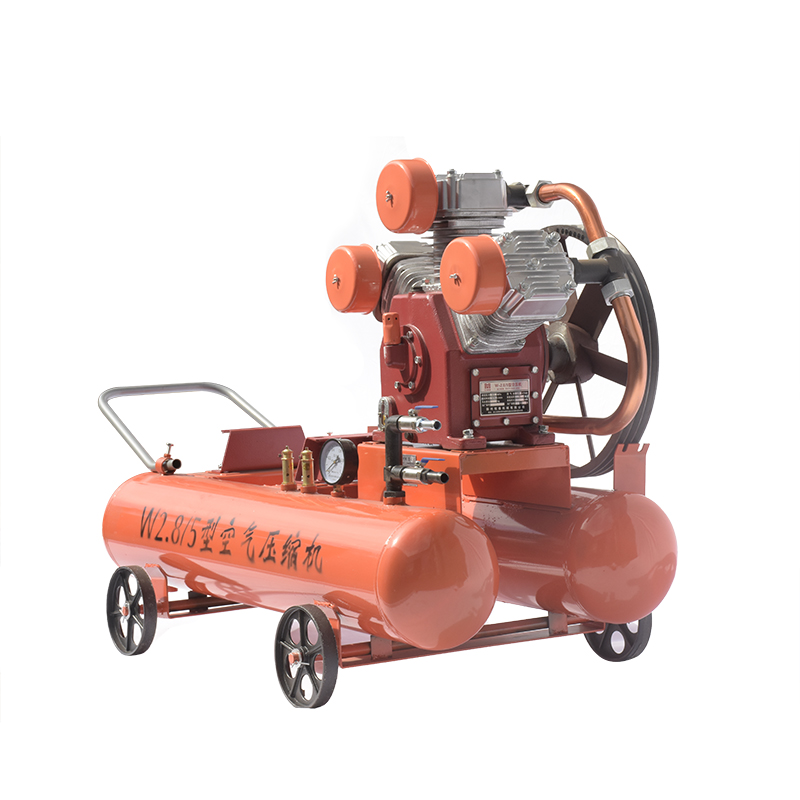
15KW Mining Diesel Piston Air Compressor W2.8-5
Diesel Portable Piston Air Compressor Mobile for Jack Hammer / Mining 1.Simple structure,light weight,easy to move . 2.Easy operating and maintenance. 3.High quality air delivery. […]
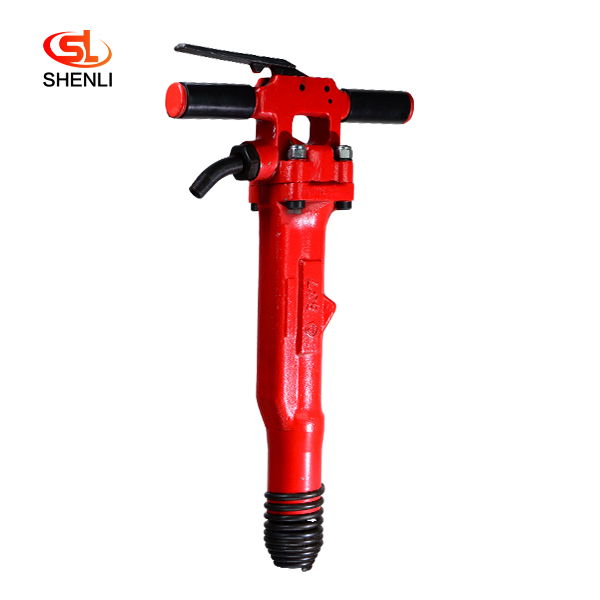
B37 Pneumatic Pick Air Shovel Cement Crusher Pneumatic Chipping Hammer
Product Description: B37 pneumatic crushing pick is a tool powered by compressed air. The compression the air is distributed to the two ends of the cylinder block in turn, so that […]
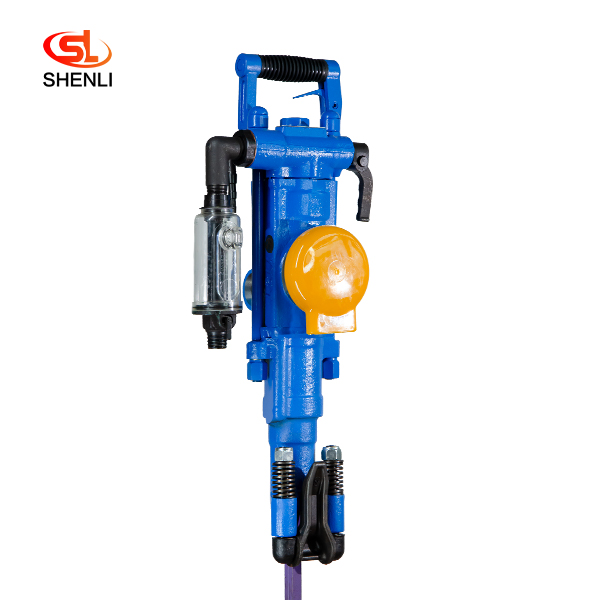
YT27 Air Leg Pneumatic Rock Drill
Short Description: The YT27 air-legged rock drill is a highly efficient lightweight rock drill suitable for downward or inclined drilling in medium-hard or hard (f=8 – 18) ro […]
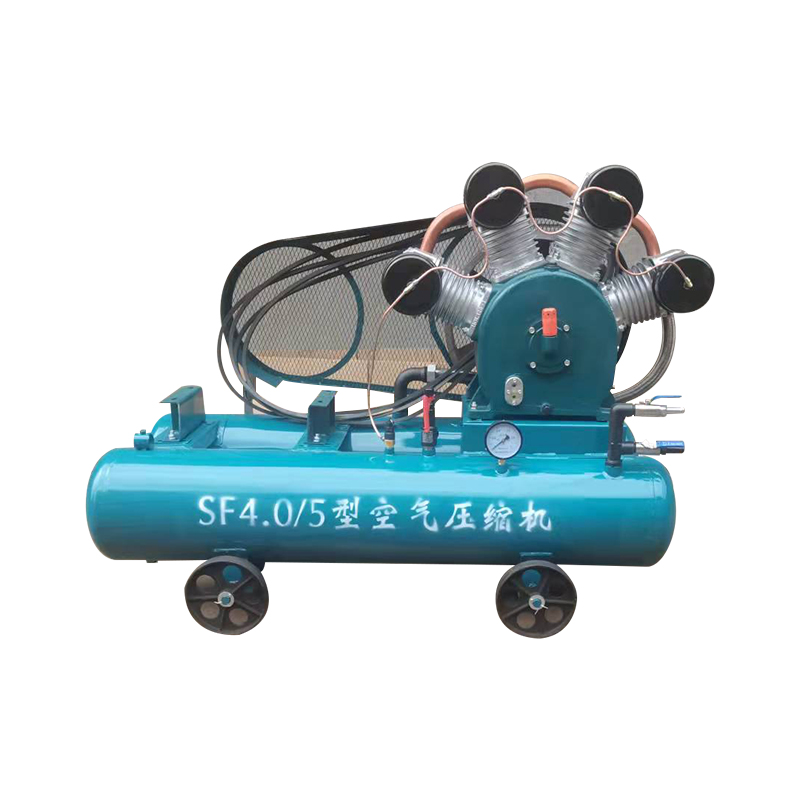
20KW Mining Diesel Piston Air Compressor SF4.0-5
Advantages Small in size,light in weight, easy to move Top material and superior technology Simple structure, high efficiency, good performance, and low price Adopt the most popula […]
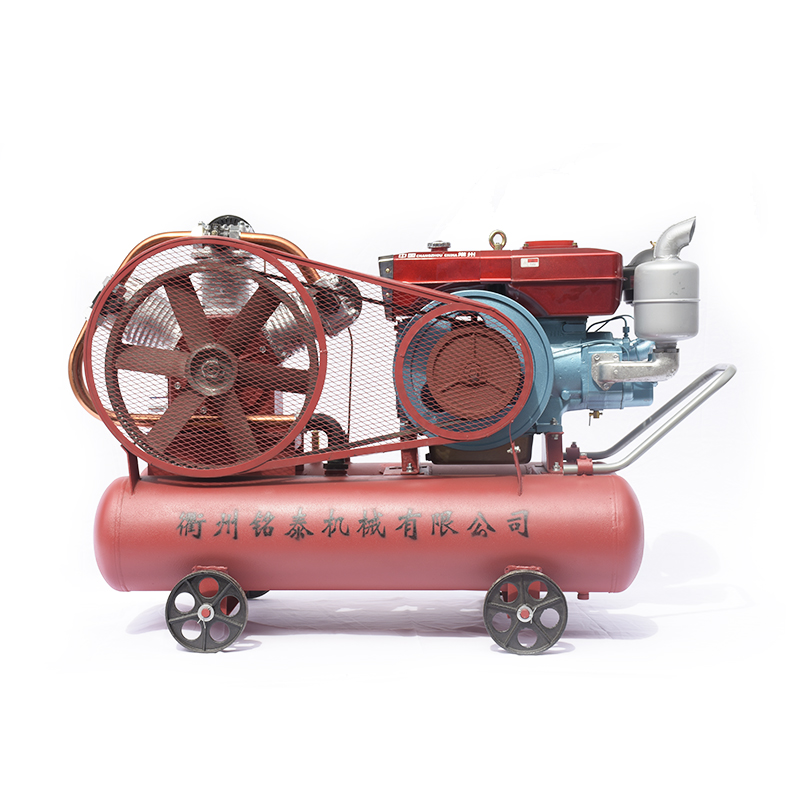
18.5KW Mining Diesel Piston Air Compressor W3.0-5
Advantages Small in size,light in weight, easy to move Top material and superior technology Simple structure, high efficiency, good performance, and low price Adopt the most popula […]
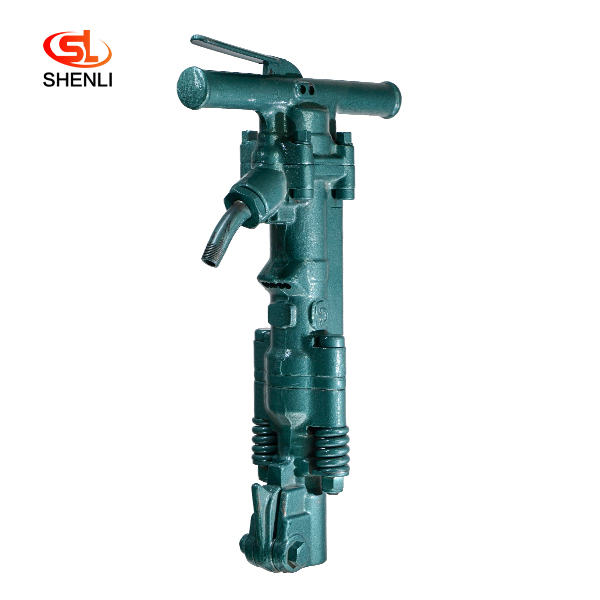
B47 Pneumatic Pick Air Shovel Cement Crusher Pneumatic Chipping Hammer
Product Description: B47 crusher adopts the mature technology of American Gardner Denver Pneumatic Group Company,It is a crushing tool powered by compressed air, which can finish r […]