Condensation is a common issue when it comes to air compressors, but with an air compressor dryer, moisture can easily and quickly be evaporated. It’s a crucial tool for preventing corrosion, rust, and the freezing of certain components that can arise due to moisture buildup in the system.
When using an air compressor, a dryer will extract the moisture content from the air being processed. This is achieved by cooling the air rapidly so that any condensation is eliminated. Many different models of air compressor dryers exist, each offering exclusive advantages.
A dependable means of drying compressed air is the refrigerated dryer, which cools the air with a refrigerant prior to compression. As temperature diminishes, condensation forms and is expelled from the system. Yet, although effective and efficient, such dryers necessitate a significant amount of energy to carry out their task.
Often incorporated in air compression systems, desiccant dryers use specialized desiccant materials, such as silica gel, to eliminate any remaining moisture in the air. This process is heavily reliant on heat, as once the desiccant material has captured all of the moisture, it must then be heated to release it from the system. Although their initial costs and maintenance requirements are higher compared to that of their refrigerated counterparts, desiccant dryers offer more efficiency and consume less energy overall.
A membranous air compressor dryer is the last of its kind. This variety uses a semi-permeable membrane to extract moisture from the pumping air, acting as a sieve that permits water vapors to pass through while barring other molecules from the other side. Despite being more costly than the others, this dryer is quite efficient and consumes minimal energy.
The choice of an air compressor dryer for your system should not be taken lightly. You need to take into account the type of dryer, whether it is energy-efficient, and of course – cost. This is essential to guarantee a moisture-free environment, and thereby prevent corrosion, rust, and frozen parts of the compressor. Doing so will ensure you find the right air compressor dryer to meet your needs.
Working with a variety of equipment demands the use of an air compressor dryer. Designed to provide a clean and dry compressed air source, these machines are essential to completing operations all across different sectors, from automotive to manufacturing. Its purpose is to keep the air compressor free from moisture and other contaminants, thus ensuring tools and machines have an ample source of power and remain in pristine condition.
The air compressor dryer is a crucial mechanism which ensures the health and safety of the air compressor. By extracting moisture from the air drawn in from the environment, the air compressor dryer guards against corrosion and other damages. Additionally, it allays the risk of fire, since dry air lacks components that can be set ablaze. This valuable tool safeguards both the air compressor and its environment by removing moisture to maintain optimal conditions.
The humidity of compressed air can be decreased with two common approaches: a refrigerant-based mechanism and a desiccant process. Refrigerant-based air compressor dryers cool the air to separate the moisture, while desiccant dryers use absorbent materials to draw out the excess water from the air. Depending on what you intend to use your compressor for, one of these two approaches may be more suitable than the other.
Refrigerant dryers are the go-to choice for removal of moisture from air in automobile air compressors. By cooling air to temperatures beyond the dew point, water content condenses and is separated from the air. This condensate then gets stored in a container which must be emptied periodically. In terms of performance, these sorts of dryers are preferred over desiccant ones as their effectiveness is much higher when it comes to removing moisture.
Utilizing desiccant materials- such as silica gel- desiccant dryers effectively liquify airborne moisture, which is then collected in a container for containment. Unfortunately, due to the finite capacity of these materials, the desiccants must be replaced frequently and tend to be less efficient than their refrigeration dryers counterparts when extracting humidity from the air.
Keeping an air compressor system in top condition is largely dependent on its dryer. A refrigerant dryer is ideal for most automotive applications, although a desiccant dryer tends to be more suited for industrial demands. It is important that these vital components undergo regular maintenance and servicing, as failing to keep an eye on them can lead to corrosion or other issues arising from moisture and contaminants.
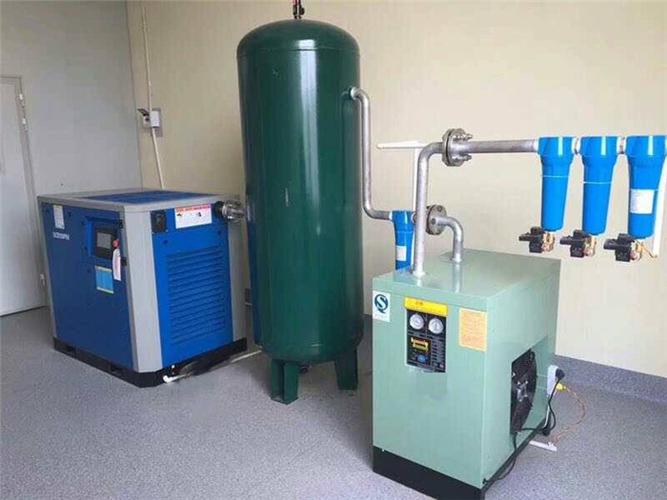
Related Product
Warning: Use of undefined constant rand - assumed 'rand' (this will throw an Error in a future version of PHP) in /www/wwwroot/www.sunritamachinery.com/wp-content/themes/msk5/single.php on line 69
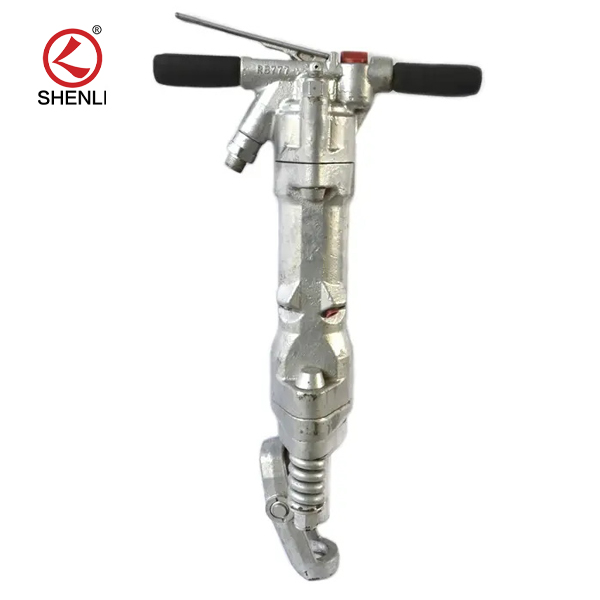
RB777 Pneumatic Pick Air Shovel Cement Crusher Pneumatic Chipping Hammer
Product description: RB777 pneumatic picks are used to build roads, install works of broken concrete and other hardens Hard object tools, the machine structure is simple, high effi […]
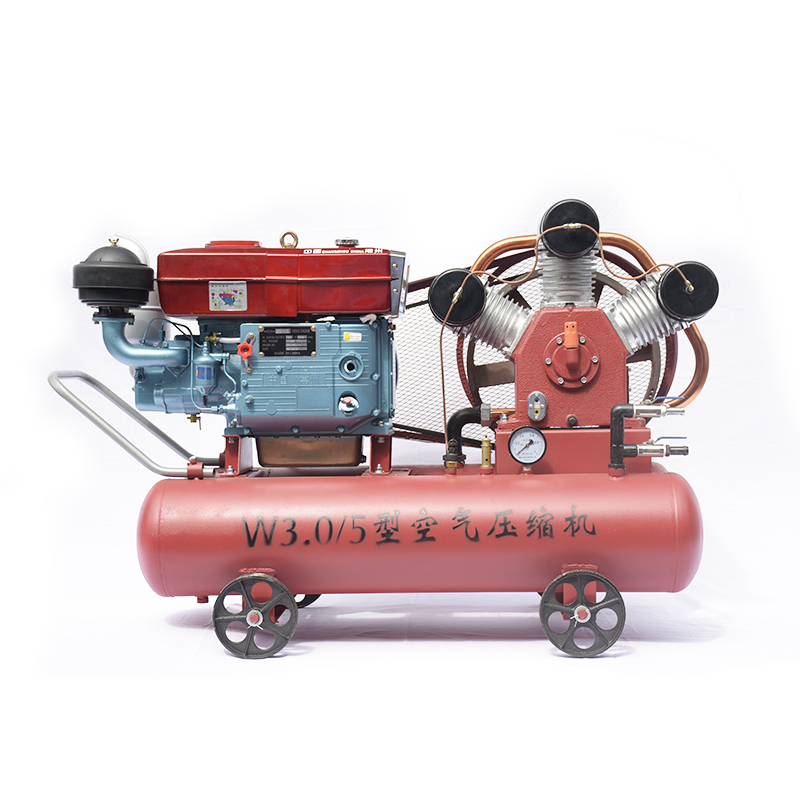
15kW Mining Diesel Piston Air Compressor W3.0-5
Diesel Portable Piston Air Compressor Mobile for Jack Hammer / Mining 1.Simple structure,light weight,easy to move . 2.Easy operating and maintenance. 3.High quality air delivery. […]
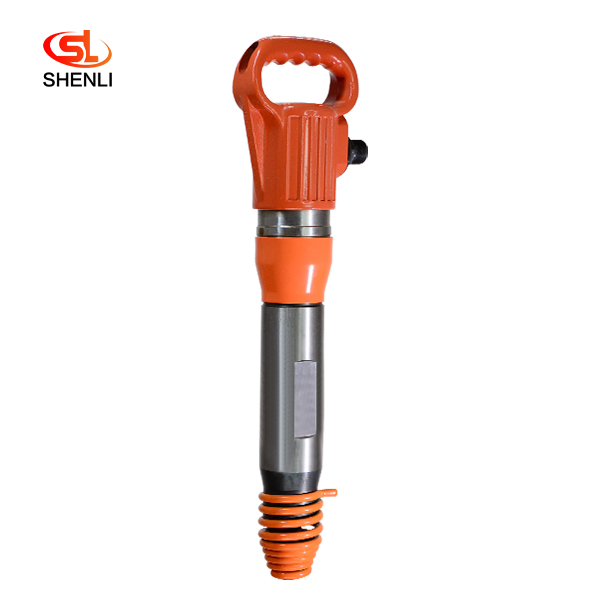
G10 Pneumatic Pick Air Shovel Cement Crusher
Product Description: The G10 air pick uses compressed air as the power tool, and the compressed air is distributed in two sections of the cylinder by the tubular distribution diver […]
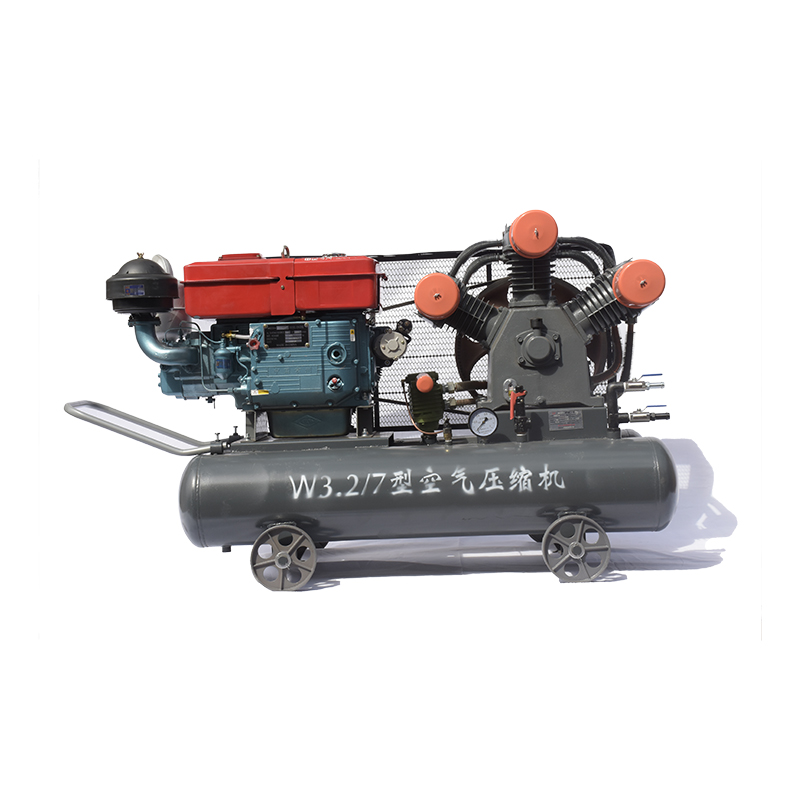
20KW Mining Diesel Piston Air Compressor W3.2-7
Advantages Small in size,light in weight, easy to move Top material and superior technology Simple structure, high efficiency, good performance, and low price Adopt the most popula […]
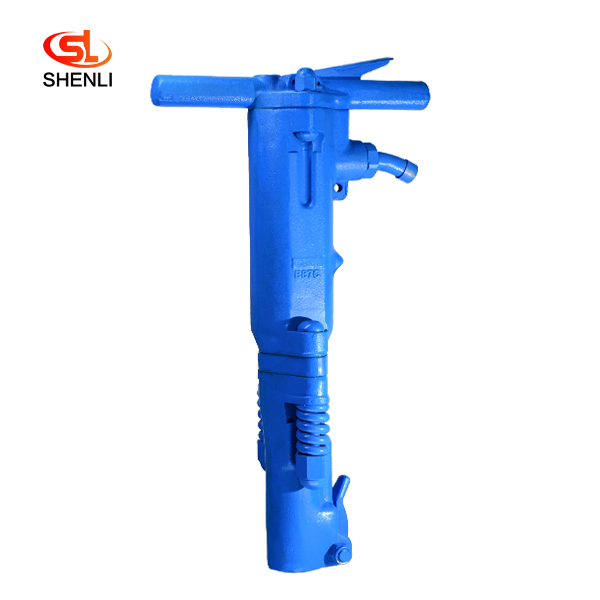
B87C Pneumatic Pick Air Shovel Cement Crusher
Product Description: The B87C crusher is made from Canada. Denver pneumatic Group company mature technology, with compressed air as a power crushing tool, can efficiently complete […]
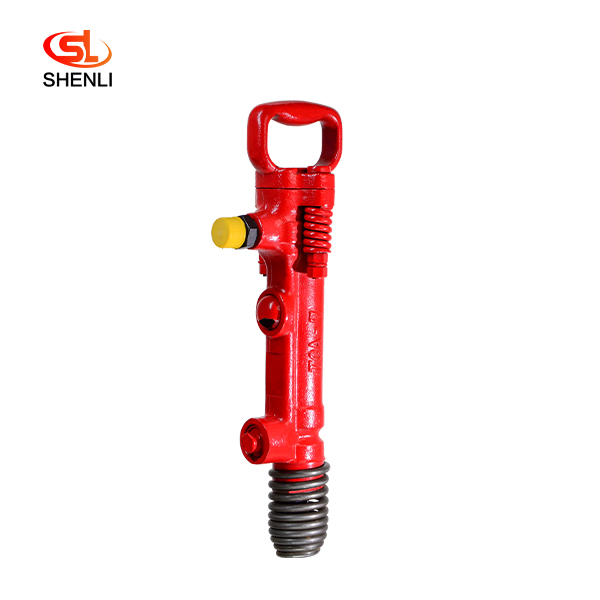
TCA7(G7)Pneumatic Pick Air Shovel Cement Crusher Pneumatic Chipping Hammer
Product introduction: Adopted Japan’s Toku technology, the air picks with proven forging technology are durable, lightweight and good performance, and easy to operate. Mainly […]
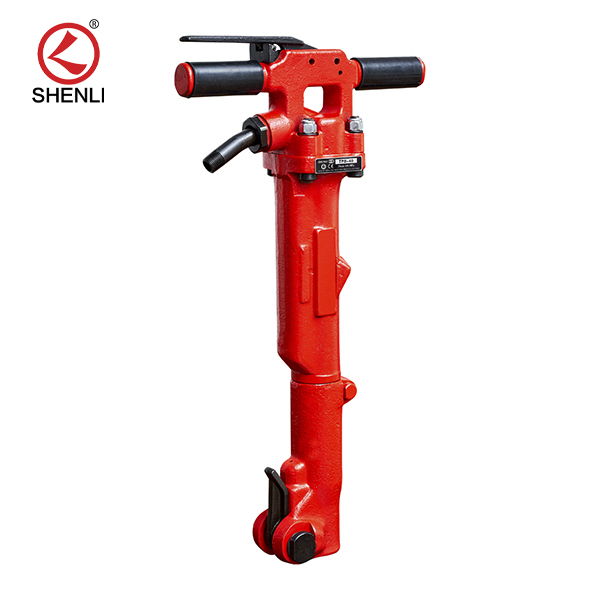
TPB40 Air Breaker Pavement Paving Breaker
Product introduction: Tpb-40 pneumatic crushing pick is a tool powered by compressed air.The compressed air is distributed to both ends of the cylinder block in turn to make the ha […]
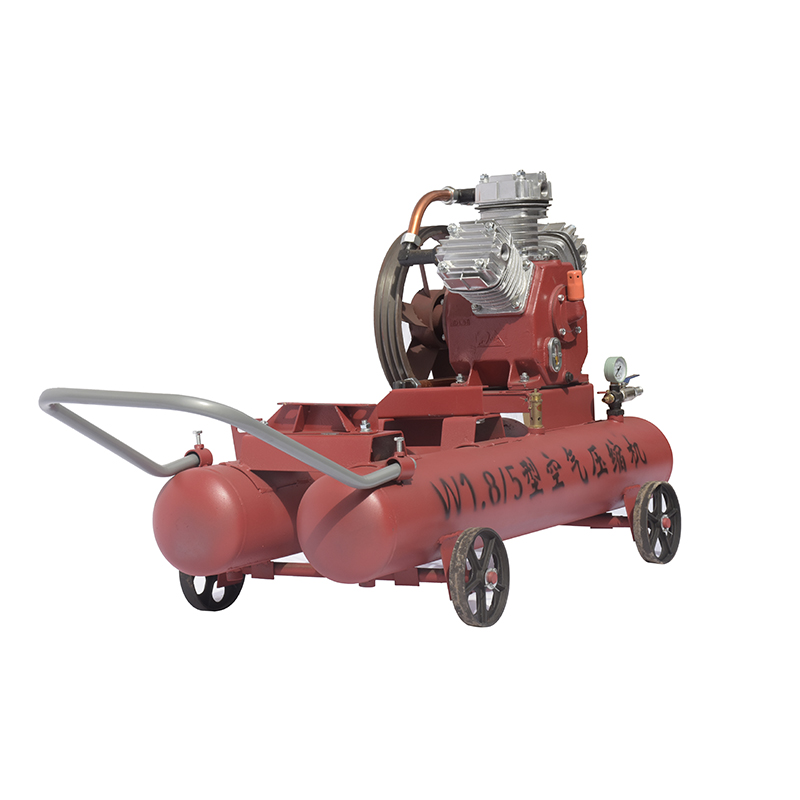
11KW Mining Diesel Piston Air Compressor W1.8-5
Diesel Portable Piston Air Compressor Mobile for Jack Hammer / Mining1.Simple structure,light weight,easy to move .2.Easy operating and maintenance.3.High quality air delivery.4.Su […]
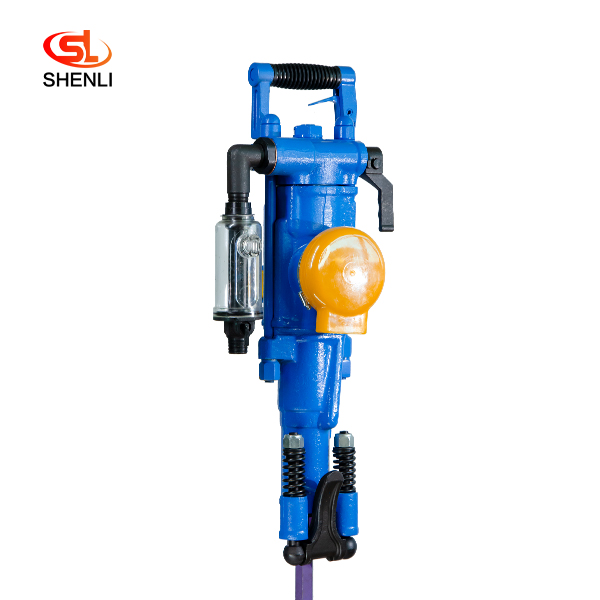
YT28 Pusher Leg Rock Drill
Short Description: The YT28 air-leg rock drill is a kind of high-efficiency, energy-saving and environmentally friendly rock drilling equipment. Compared with similar pneumatic pro […]