An air compressor check valve is an essential item utilized in dissimilar industries, from the automotive world to the industrial domain. This component is critical in guaranteeing that pressurized air is converted, stored, and sustained at a given level. This article intends to explain what an air compressor check valve is, how it functions, various kinds of types that are accessible as well as the importance of employing the right kind for your compressor.
Stored air within a compressor can be effectively controlled by the strategic utilization of an air compressor check valve. Placed at the end of the compressor’s output pipe or at the intake manifold, this device opens during the running of the compressor to allow atmospheric air into the intake manifold to subsequently be fought through and pushed out of the machine. By hindering any reverse flow, a consistent pressure is maintained and is safeguarded from being pulled back to the intake manifold.
If you have ever ventured to purchase an air compressor, then you are likely familiar with the different types of check valves available. The most popular ones are swing check valves, ball check valves, and diaphragm check valves. Swing check valves have a flap that can open against the pressure of air passing through it and then close upon its sudden release. Ball check valves have a weighted ball that is pressed open against a seal when airflow is pushed through and releases when the pressure drops. When it comes to diaphragm check valves, they utilize a flexible rubber diaphragm which allows air to pass over an aperture and shuts tightly when the airflow lessens.
Ensuring the proper functioning of your compressor is essential, for which the appropriate type of check valve must be selected. Depending on the compressor type – low or high-pressure – the right kind of valve must be determined: either a ball check valve or a diaphragm check vessel. Of course, installation should be taken into account too, making certain it is modernly made and functioning accordingly.
All in all, a check valve for an air compressor is a critical component to ensure it runs smoothly. The right type of valve for your compressor and its correct installation are indispensable measures to guarantee the safety and effective operations of your machine. With the right precautions, you can rest easy knowing your compressor is up to the egg.
In ensuring the effective operation of an air compressor system, the check valve functions as an integral element. This valve maintains a controlled stream of air between the compressor and connected components, enabling air to only travel in one direction while simultaneously prohibiting air from reentering the compressor on pressure drop.
Located in the conduit between the compressor and the exit, the check valve is strategically positioned to open when there is greater pressure in the line compared to what is present within the compressor. Flow from the compressor to the output is allowed while pressure dissipates; as soon as it dissipates, the valve closes to avoid air from flowing into the compressor.
Without the check valve, air would have the capability to flow backward into the compressor. This undesirable consequence would result in the compressor becoming exceptionally hot which could lead to it failing. In addition, the regulator and filter components of the system might be adversely impacted by backflow as well. The check valve is undoubtedly essential, as it disables any such incursions and helps maintain a steady working order.
When selecting a check valve to be compatible with an air compressor system and fluid, be sure to consider the working pressure, rate of movement and temperature in the system. The most common materials for check valves are brass, stainless steel, or plastic. Ensuring you select the right valve is crucial in guaranteeing functionality.
The arrow etched onto the check valve should be aligned with the intended direction of the airflow–this is a critical step when installing the valve. Seeing to it that this is done correctly will help to ensure that the valve is functioning as intended and that the air is moving in its designated flow.
To protect your compressor and other components, it is essential to routinely inspect the check valve for any wear and tear or damage. If the check valve is not up to operating conditions, it can cause the compressor to run too warm or lead to peripheral system failures. Disregarding any harm or wear on the check valve and not replacing it could impede performance, thus a prompt replacement is recommended.
Keeping the air compressor system functioning and running optimally requires a critical piece: the check valve. Without it, backflow of air to the compressor, damage to the other components, and improper operation could occur. Thus, it is vital to select the correct check valve for the system, install it properly, and examine it periodically to guarantee everything is functioning as expected.
Post time: 2023-07-22Related Product
Warning: Use of undefined constant rand - assumed 'rand' (this will throw an Error in a future version of PHP) in /www/wwwroot/www.sunritamachinery.com/wp-content/themes/msk5/single.php on line 69
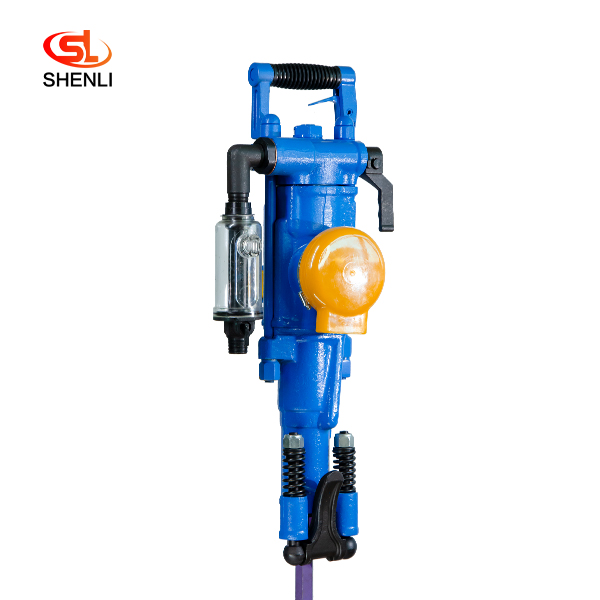
YT28 Pusher Leg Rock Drill
Short Description: The YT28 air-leg rock drill is a kind of high-efficiency, energy-saving and environmentally friendly rock drilling equipment. Compared with similar pneumatic pro […]
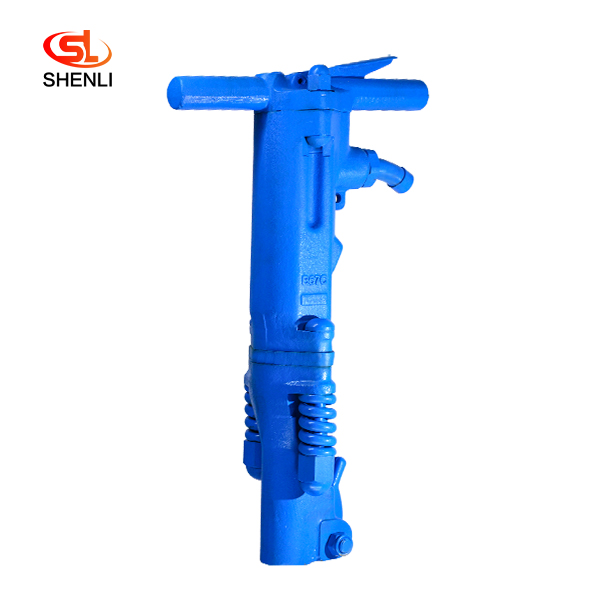
B67C Pneumatic Chipping Hammer
Product description: The B67C crusher is made from Canada. Denver pneumatic Group company mature technology, with compressed air as a power crushing tool, can efficiently complete […]
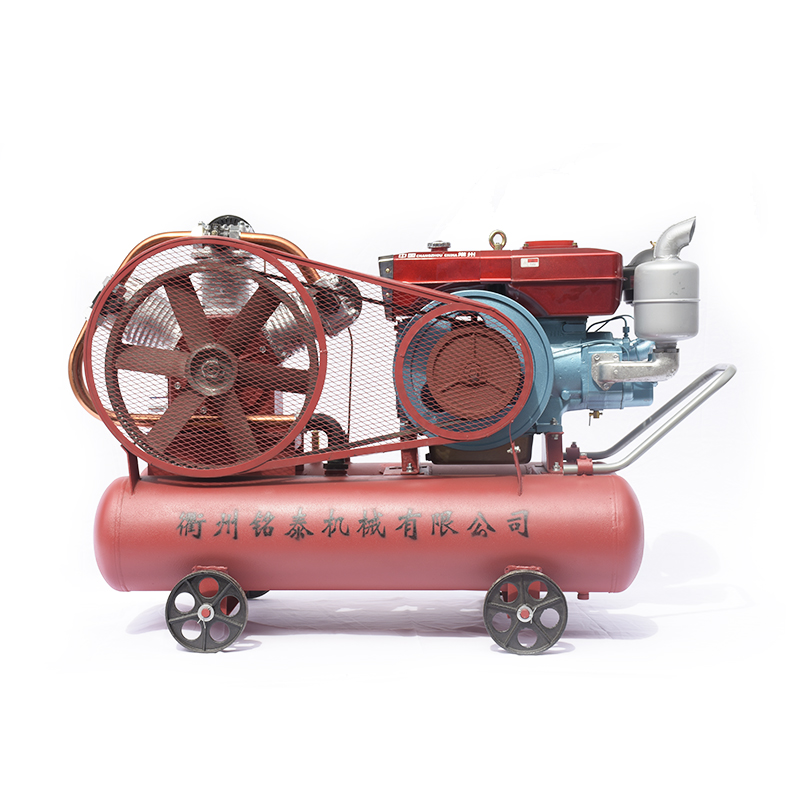
18.5KW Mining Diesel Piston Air Compressor W3.0-5
Advantages Small in size,light in weight, easy to move Top material and superior technology Simple structure, high efficiency, good performance, and low price Adopt the most popula […]
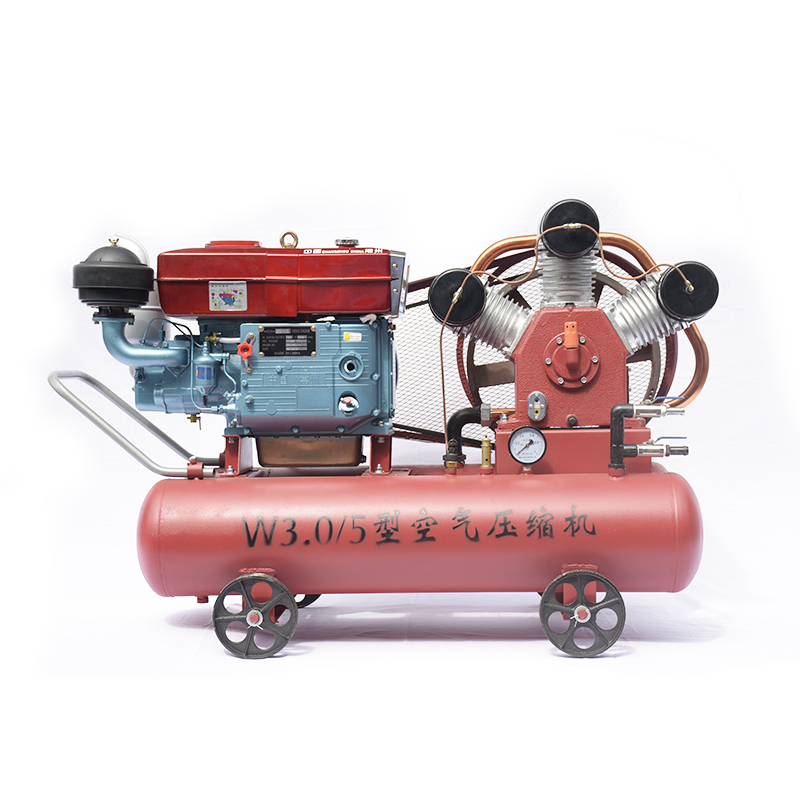
15kW Mining Diesel Piston Air Compressor W3.0-5
Diesel Portable Piston Air Compressor Mobile for Jack Hammer / Mining 1.Simple structure,light weight,easy to move . 2.Easy operating and maintenance. 3.High quality air delivery. […]
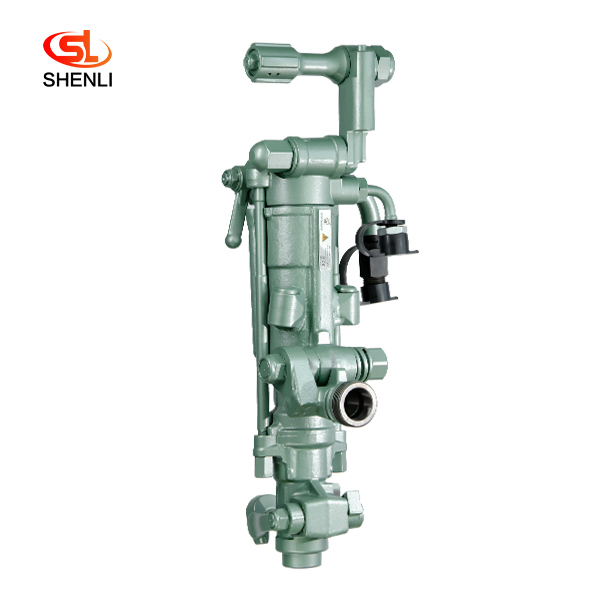
S250 Air Leg Pneumatic Rock Drill Pusher Leg Rock Drill
Product description: (S250 jackleg Drill) has been the preferred choice of miners who demand high performance, superior control and lasting reliability. the S250 jackleg allows ope […]
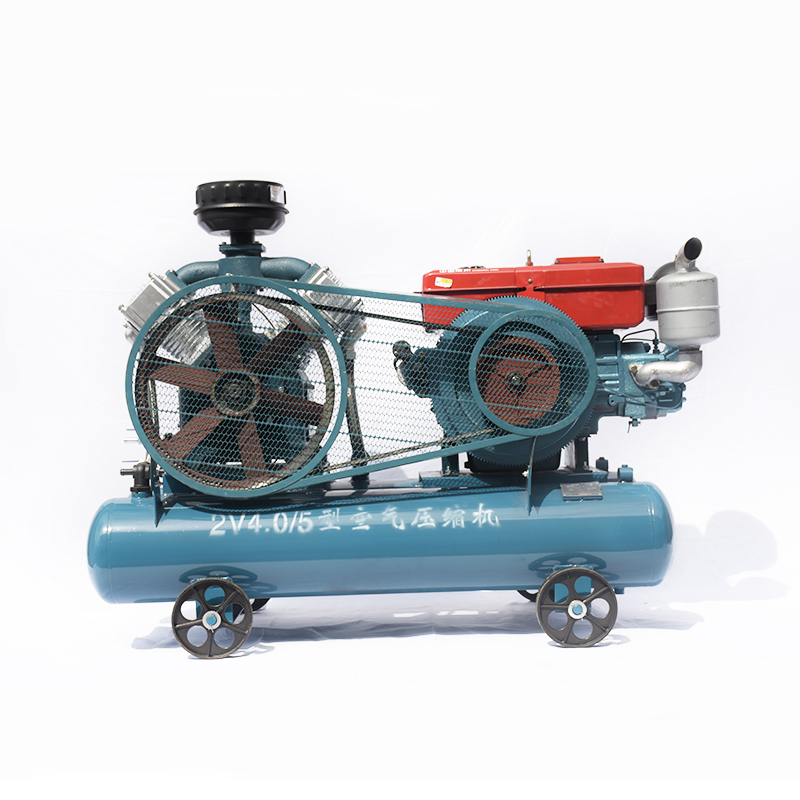
20KW Mining Diesel Piston Air Compressor 2V4.0-5
Double Air Tank Diesel Portable Best-Selling Engine Oil Piston Air Compressor are mainly used to supply stable and clean compressed air to the pneumatic tools and keep them working […]
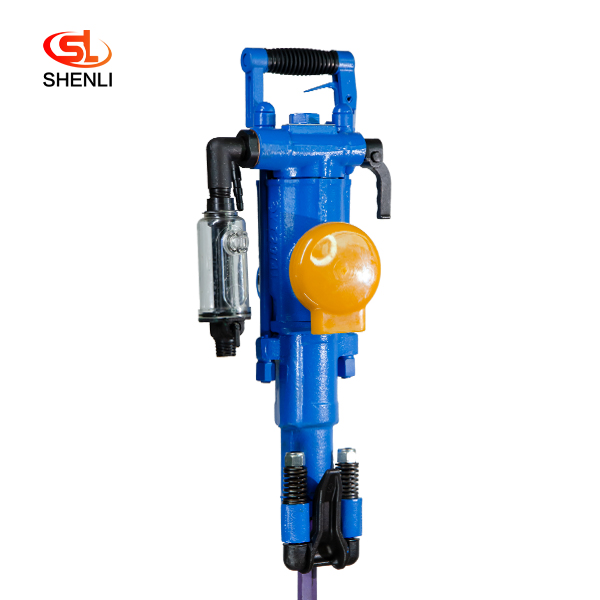
YT29A Air Leg Pneumatic Rock Drill
Short Description: YT29A air-legged rock drills are heavy-duty push-leg (air-legged) rock drills with low energy consumption, which are more suitable for drilling horizontal or inc […]
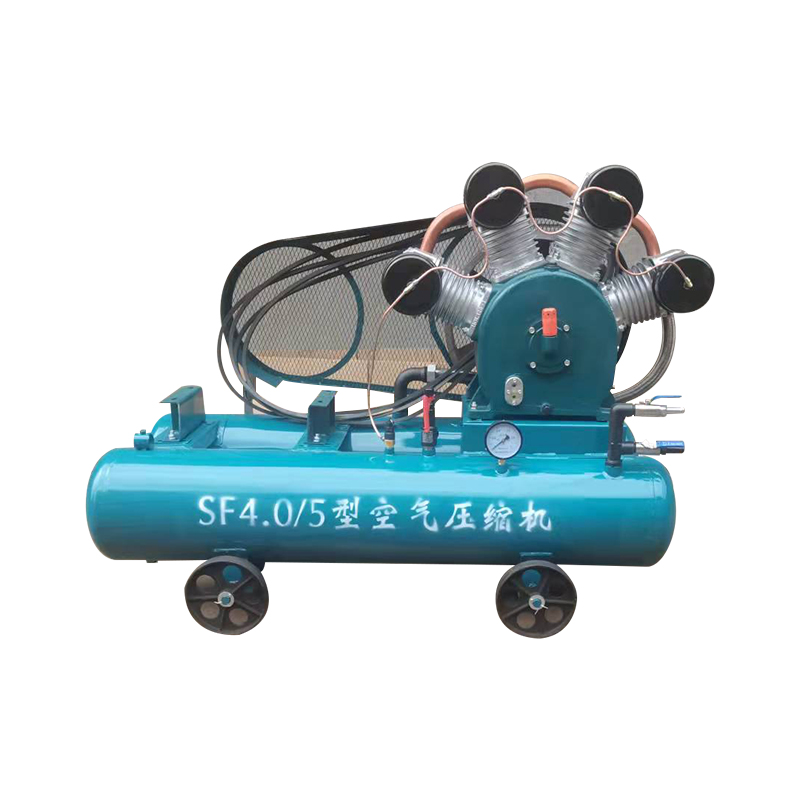
20KW Mining Diesel Piston Air Compressor SF4.0-5
Advantages Small in size,light in weight, easy to move Top material and superior technology Simple structure, high efficiency, good performance, and low price Adopt the most popula […]
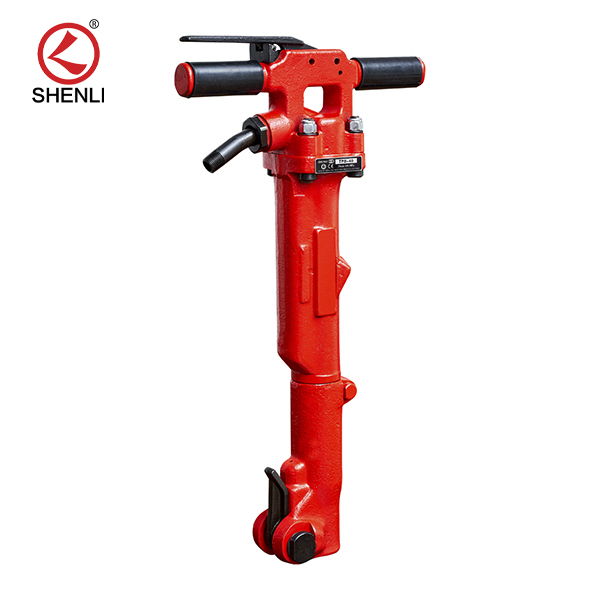
TPB40 Air Breaker Pavement Paving Breaker
Product introduction: Tpb-40 pneumatic crushing pick is a tool powered by compressed air.The compressed air is distributed to both ends of the cylinder block in turn to make the ha […]