A compressor is a machine that works by compressing sundry gases so that there’s an uptick in the pressure within, and an air compressor lives up to its namesake, increasing the pressure of air. Occupying a central role in providing potential energy, it harnesses power to force air into a storage tank until the pressure reaches an engineered upper limit, at which point, the device will halt and the concentrated air is primed and ready to power tools and machinery alike.
In the early years of the 19th century, pioneering minds crafted the initial air compressors for use in mining endeavors. It was not until 1849 that a much more convenient air compressor was created by Isaac Singer. This innovative design allowed blacksmiths and other craftspeople to benefit from the machine’s power. Nowadays, air compressors are fundamental in multiple trades, such as automotive repair and home improvement.
Air Compressors: An Explanation of Reciprocating, Rotary Screw, and Centrifugal Types.
The power behind reciprocating air compressors lies in their pistons that are driven by a crankshaft. A variety of models are available, such as single-stage and two-stage compressors. Single-stage designs are useful for air pressures that do not exceed 150 psi, while two-stage compressors are best for jobs that rely on increased pressure, usually up to 200 psi.
Employing a pair of intermeshed screws, rotary screw air compressors enable the compression of air for a range of uses. Ready to be deployed in either their oil-lubricated or oil-free iterations, they can cater to both industrial and critical purposes. The oil-lubricated kind, outfitted for pressures below 150 psi, is intended mainly for industrial undertakings. The oil-free model, meanwhile, has proved suitable for more delicate operations such as those faced by the food and beverage industry; plus, pressure demands exceeding 150 psi can also be met with this variant.
Through the dynamic force of centrifugal action, centrifugal air compressors are designed to draw atmospheric air toward the middle of an impeller as it rapidly rotates, successfully pressurizing it to a maximum of 100 psi.
The output efficiency of an air compressor is determined by two critical elements: CFM (cubic feet per minute) and PSI (pounds per square inch).
CFM is an indication of how much air can be displaced per minute, the most common measure of which is cubic feet per minute (cfm). Conversely, PSI depicts the amount of pressure created by the compressor and is normally provided in pounds per square inch (psi).
Meter readings vary, but the average air compressor size is 5 hp, delivering an output of 4 cubic feet each minute at 100 pounds per square inch (psi). But more horsepower can be achieved — with certain models capable of producing a remarkable 50 cfm with a significantly higher psi rating of 175.
When looking for an air compressor, one must examine the needs of the tools and devices that will be connected to it. For instance, a nailer might need 2 cubic feet per minute at 90 pounds per square inch (cfm &psi). Alternatively, a sandblaster would require 15 cfm and 80 psi.
It is essential to contemplate the duty cycle of the air compressor. This particular factor represents the proportion of time that the compressor can run while staying within the upper temperature restriction. Commonly, air compressors possess a maximum duty cycle of 50% or lower; thus, it must not be operated surpassing a 30 minute period for every 60 minutes.
When it comes to air compressors, options abound. From portable models for inflating tires to stationary systems for powering pneumatic tools and truck-mounted versions for tough applications like managing air brakes, the possibilities are seemingly endless. Each type of compressor is perfectly suited for its specific task, so it’s important to take into consideration the project you’re undertaking before choosing the right compressor for the job.
Depending on the application, air compressors can be powered by electricity, gasoline, or diesel. Electric-powered compressors are suitable for small tasks like tire inflation, whereas gasoline-powered models offer an efficient solution to utilizing pneumatic tools. Those which require more power to operate heavier duties, such as air brakes, may opt for a more powerful diesel-powered model.
Meeting the CFM and PSI requirements of the tools and equipment in use is an important aspect of picking an air compressor. Along with this, it is also critical to look into the duty cycle of the compressor. A plethora of sizes and layouts is available, each suitable for particular applications.
Post time: 2023-06-22Related Product
Warning: Use of undefined constant rand - assumed 'rand' (this will throw an Error in a future version of PHP) in /www/wwwroot/www.sunritamachinery.com/wp-content/themes/msk5/single.php on line 69
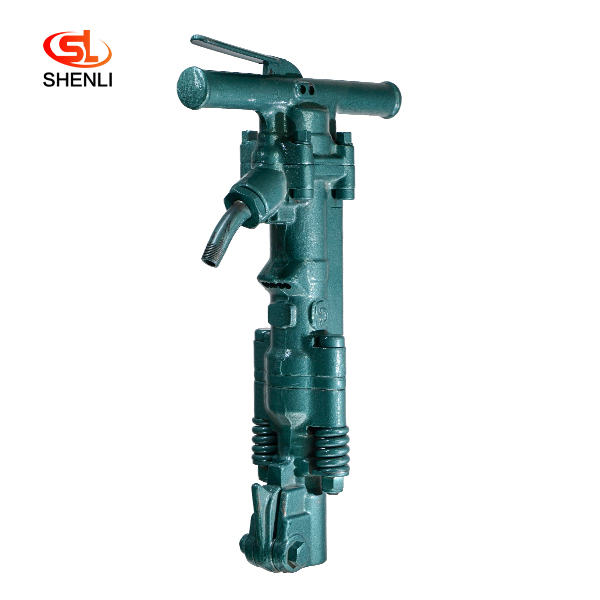
B47 Pneumatic Pick Air Shovel Cement Crusher Pneumatic Chipping Hammer
Product Description: B47 crusher adopts the mature technology of American Gardner Denver Pneumatic Group Company,It is a crushing tool powered by compressed air, which can finish r […]
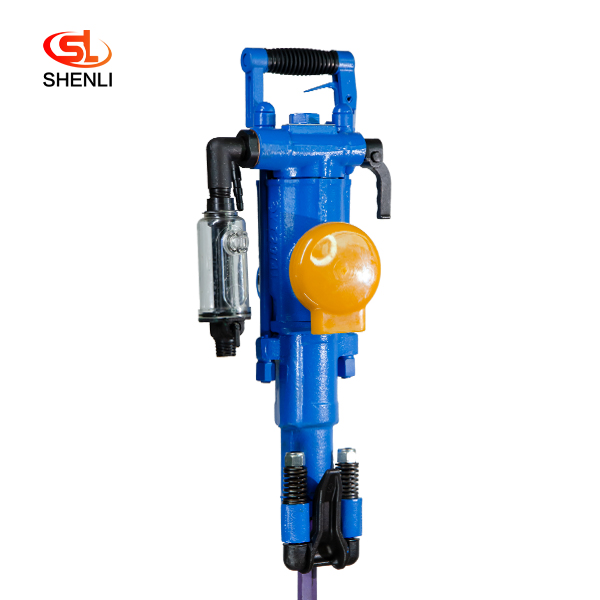
YT29A Air Leg Pneumatic Rock Drill
Short Description: YT29A air-legged rock drills are heavy-duty push-leg (air-legged) rock drills with low energy consumption, which are more suitable for drilling horizontal or inc […]
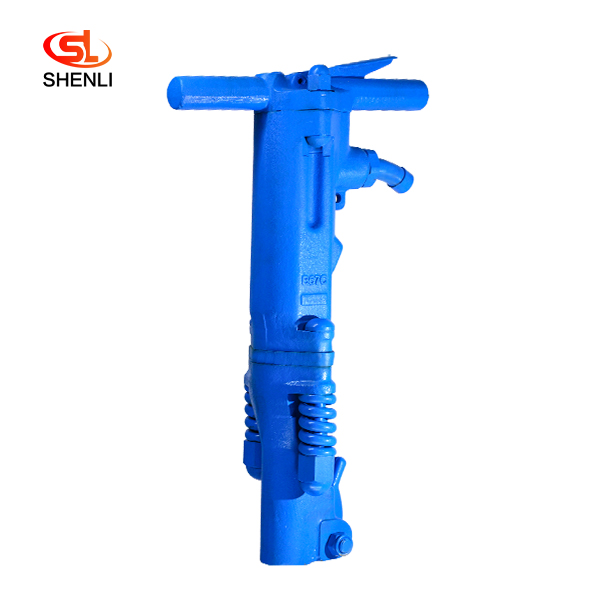
B67C Pneumatic Chipping Hammer
Product description: The B67C crusher is made from Canada. Denver pneumatic Group company mature technology, with compressed air as a power crushing tool, can efficiently complete […]
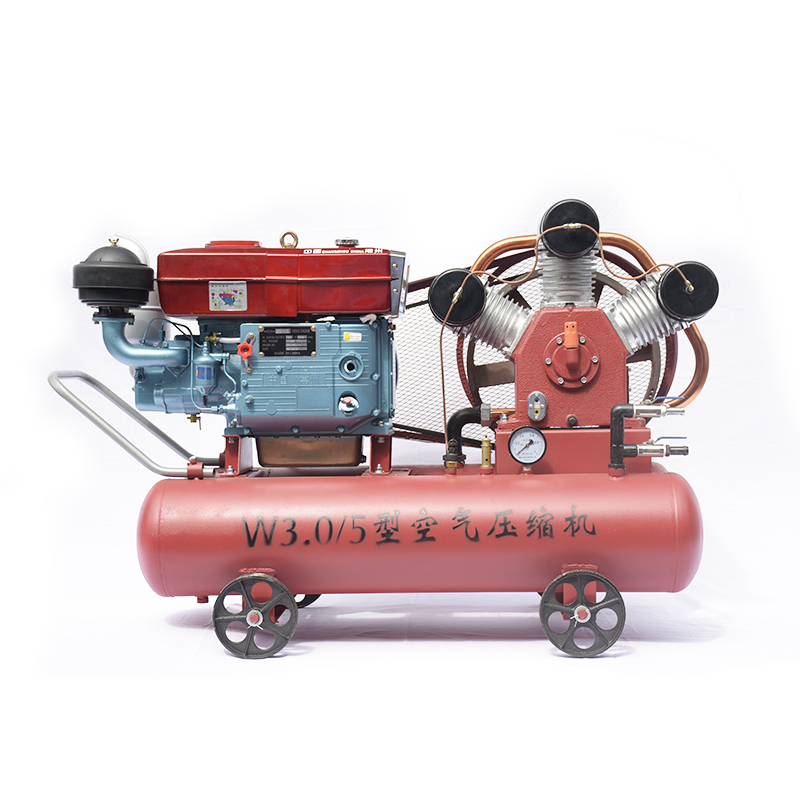
15kW Mining Diesel Piston Air Compressor W3.0-5
Diesel Portable Piston Air Compressor Mobile for Jack Hammer / Mining 1.Simple structure,light weight,easy to move . 2.Easy operating and maintenance. 3.High quality air delivery. […]
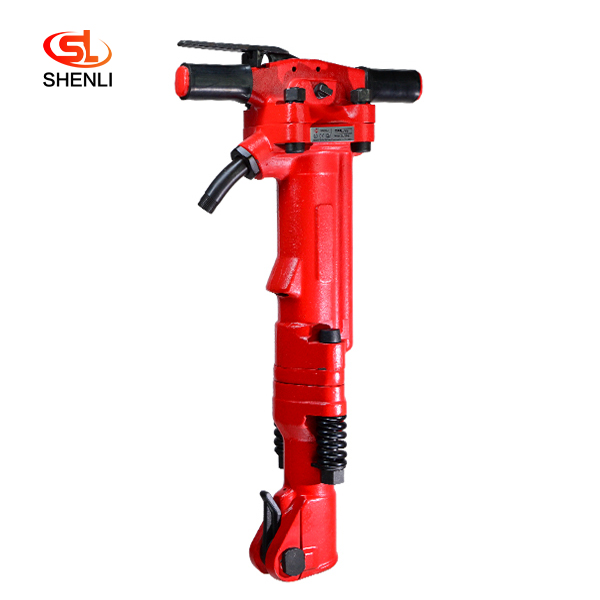
TPB90 Air Breaker Pavement Paving Breaker
Product introduction: TPB-90 crusher adopts the mature technology of TOKU Group, Is compressed air as the power of the crushing tool, can efficiently complete the reinforced concre […]
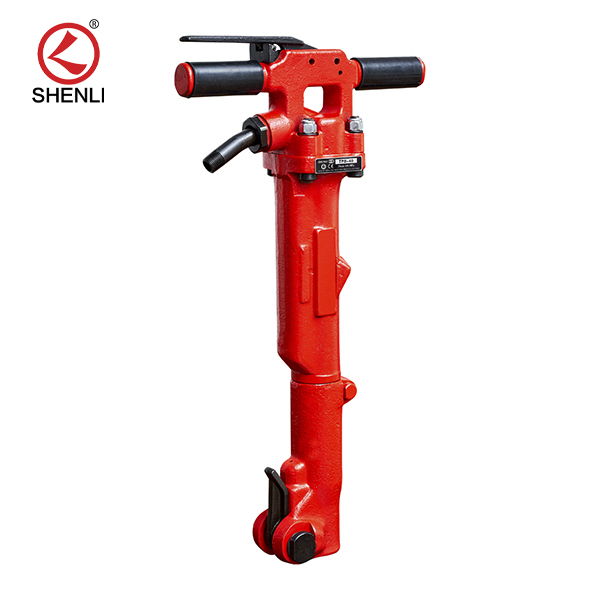
TPB40 Air Breaker Pavement Paving Breaker
Product introduction: Tpb-40 pneumatic crushing pick is a tool powered by compressed air.The compressed air is distributed to both ends of the cylinder block in turn to make the ha […]
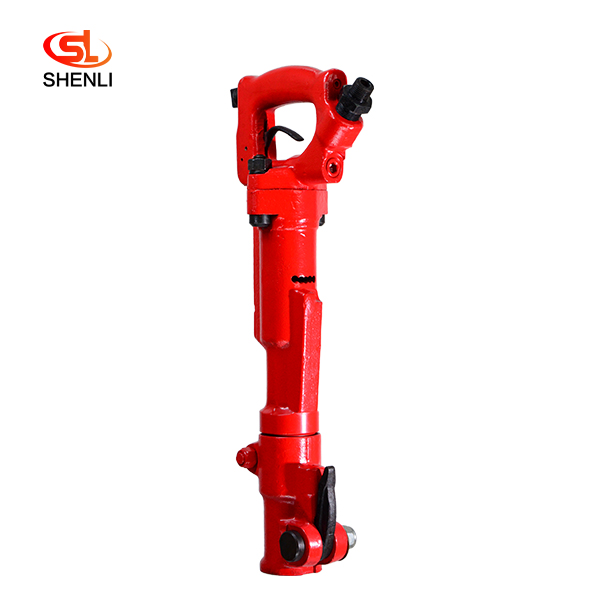
TCD20 Pneumatic Pick Air Shovel Cement Crusher Pneumatic Chipping Hammer
Product description: The TCD-20 pneumatic pick is powered by compressed air using Japan’s TOKU technology Crushing tools, features: lightweight, small size, large strike ener […]
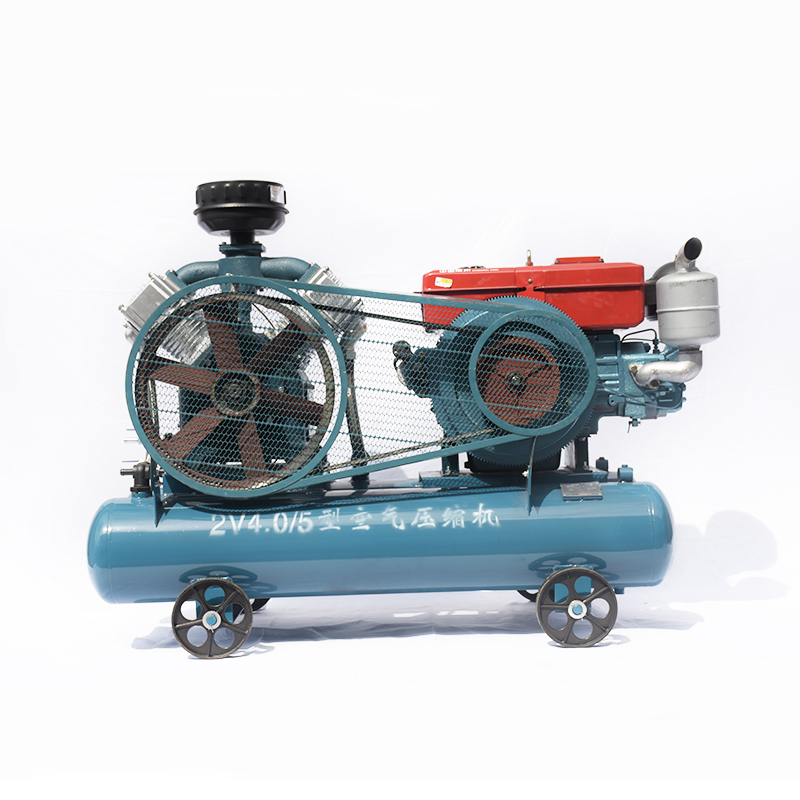
20KW Mining Diesel Piston Air Compressor 2V4.0-5
Double Air Tank Diesel Portable Best-Selling Engine Oil Piston Air Compressor are mainly used to supply stable and clean compressed air to the pneumatic tools and keep them working […]
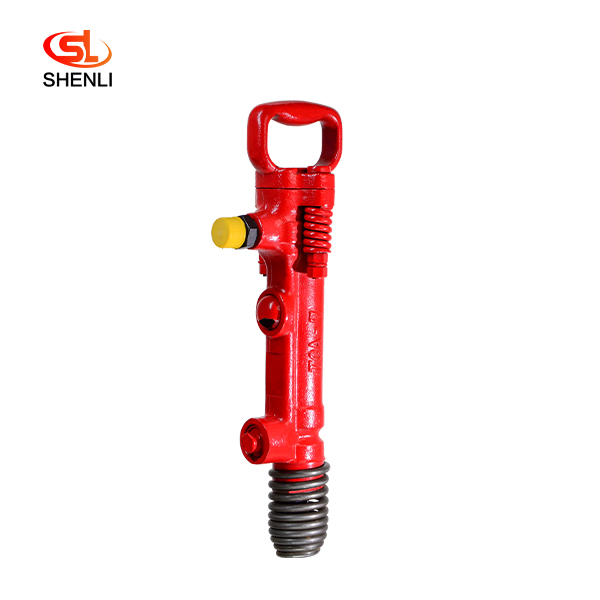
TCA7(G7)Pneumatic Pick Air Shovel Cement Crusher Pneumatic Chipping Hammer
Product introduction: Adopted Japan’s Toku technology, the air picks with proven forging technology are durable, lightweight and good performance, and easy to operate. Mainly […]