Industrial projects require an efficient and secure system for air compression – one that makes the job both easy and safe. 220 Wire is an ideal choice to fulfil these requirements as it ensures maximum performance and safety. This wire offers extreme durability and amazing electrical conductivity that provide unmatched resistance to stretching and breakage. Plus, it’s flame-resistant and helps with optimal temperature control. Overall, 220 Wire is an optimal option for any air compressing project that needs an efficient and secure system.
Industrial applications demand optimal safety and productivity, which often necessitates specialized wiring. When it comes to powering air compressors and other power tools, 220 wire is typically the preferred choice for its effective performance. This guide will divulge exactly what 220 wire involves, explain why it is a standout option, and provide detailed instructions on how to properly install it.
What Lies Beneath the Surface of 220 Wire?
Electrical wiring with two 120-volt wires and a bare copper ground wire, 220 wire is frequently used in industrial settings such as air compressors. Its distinctive black, red, and green coloration designates the two insulated 120-volt wires and copper ground wire respectively. As the combined wattage of the elements is 220 volts, the wiring was named 220 wire.
Let’s Talk About the Role of 220 Wire in Air Compressors.
A malfunctioning air compressor system can be caused by a variety of issues, and one of the most dangerous is improperly wired components. 220 wire will ensure that the unit has enough current to power it correctly, as other wiring options aren’t strong enough to handle the power needs. Without 220 wire, users are at risk of having an unusable system or worse, a hazardous one. Consequently, it is imperative that this specific type of wiring is put in place upon installation.
Navigating The Installation Of 220 Wiring
In order to connect a 220 wire to an air compressor with accuracy and safety, the electricity must first be securely disabled at the breaker. Cutting the power stops any potential for electrocution, allowing the simpler steps of installation to be performed. For effective and sound wiring of an air compressor, one must take care and pay attention to the finer points.
Once the source of energy is shut off, it is essential to attach the wires in a certain way. The black cable needs to be linked to the circuit-breaker and the red one to the compressor. As for the ground wire, it should be fastened to the designated connection point which belongs to the compressor itself.
After connecting the cables, the circuit breaker must be restored to its original setting and the compressor needs to be put to the test. If all is functioning as it should, the installation can be declared finished.
For a safe wiring experience, installation steps need to be followed carefully plus extra protection needs to be put in place. To shield against shocks, donning protective gear such as gloves and safety glasses should be compulsory. An equally critical measure is to avoid overloaded circuits, as this could be disastrous.
220 wire is necessary for any air compressor setup as it is the only wiring option capable of properly handling the large amount of current the machine needs. To keep your compressor functioning safely and adequately, it is essential to properly install the wiring and to be cautious while dealing with it. Abiding by these instructions can ensure that your air compressor runs smoothly.
Wiring for a Breath of Fresh Air: A Guide to Compressors
When it comes to getting the best performance out of an air compressor, the wiring is absolutely essential. The type of connection used between the machine and its power source is of paramount importance. To take your air compressor to the next level and be sure you’re utilizing its peak potential, 220-volt wiring is the go-to choice.
Unravelling the Mystery of 220 Wire
220 wire is an essential component to connecting a power source to a compressor. It is the most preferred wiring electrodes for powering air compression systems, providing ample energy needed to energize most compressors in current use.
Two insulated conductors make up the two-wire 220 wire system. One of the wires has electrical energy running through it – the hot wire – while the other carries electrical energy in the opposite direction – the neutral wire. When combined, these two wires complete the circuit, ensuring a fully functional power supply.
The Benefits of Employing a 220 Wire for an Air Compressor
Finding a secure and reliable way to power an air compressor? 220-volt wiring is your best option. Not only does it provide the necessary power, but it also gives users an increased degree of safety and reliability. It goes without saying that this is the preferred method for powering an air compressor.
When contemplating the most financially viable wiring system, 220 volts stands in a league of its own. Not only does it provide ample energy, it also requires fewer components than other types of wiring for setup, making installation a breeze.
Are There Other Elements that I Should Ponder Before Deciding to Employ 220 Wire for My Air Compressor?
To ensure a suitable power supply for the air compressor, 220-volt wiring must be implemented that is able to bear up to the electrical load in terms of both amperage and wattage. In other words, choosing a wiring system that meets the power needs of the compressor is imperative.
When it comes to wiring, it is essential to ensure that it is installed in full compliance with local, state, and national electrical regulations. If ever unsure, enlisting an experienced electrician can help to ensure the wiring is correctly fitted.
To put the system in the right place, it is fundamental to make sure that the wiring is connected firmly to the ground. Doing so will keep the current circulating in the wiring regulated and evenly distributed.
For a firmly-linked, economically-savvy flow of electricity, 220 wiring is unbeatable in terms of powering an air compressor. To effectively meet your compressor’s energy requirement, it’s paramount to opt for the right type of wiring, then get a certified specialist to professionally set it up to guarantee maximum safety.
Post time: 2023-07-14Related Product
Warning: Use of undefined constant rand - assumed 'rand' (this will throw an Error in a future version of PHP) in /www/wwwroot/www.sunritamachinery.com/wp-content/themes/msk5/single.php on line 69
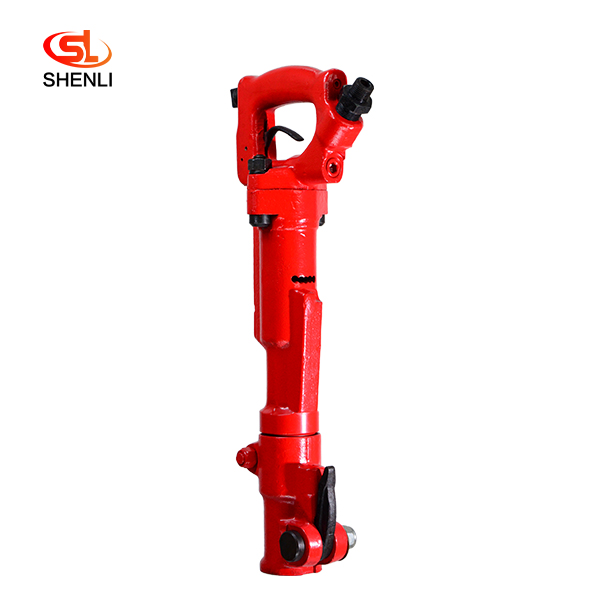
TCD20 Pneumatic Pick Air Shovel Cement Crusher Pneumatic Chipping Hammer
Product description: The TCD-20 pneumatic pick is powered by compressed air using Japan’s TOKU technology Crushing tools, features: lightweight, small size, large strike ener […]
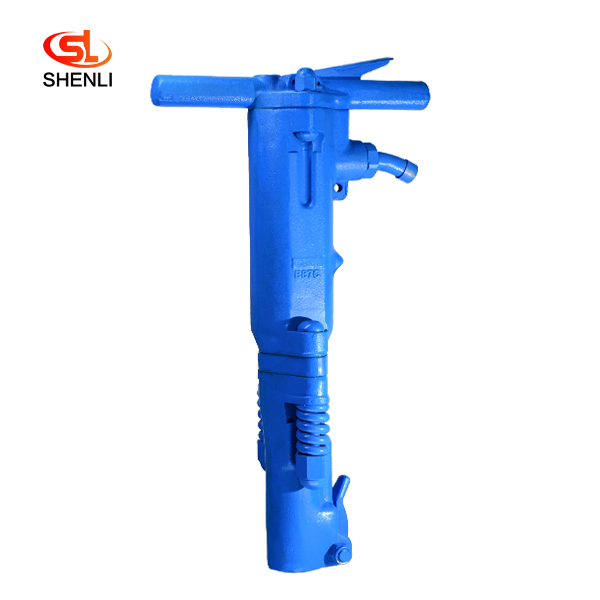
B87C Pneumatic Pick Air Shovel Cement Crusher
Product Description: The B87C crusher is made from Canada. Denver pneumatic Group company mature technology, with compressed air as a power crushing tool, can efficiently complete […]
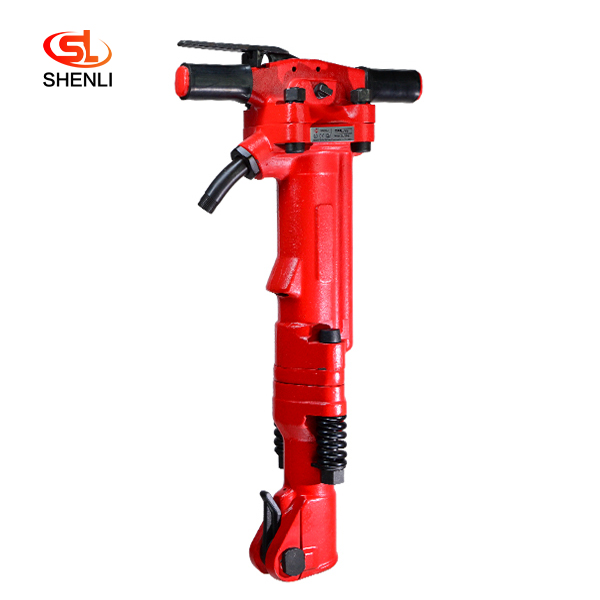
TPB90 Air Breaker Pavement Paving Breaker
Product introduction: TPB-90 crusher adopts the mature technology of TOKU Group, Is compressed air as the power of the crushing tool, can efficiently complete the reinforced concre […]
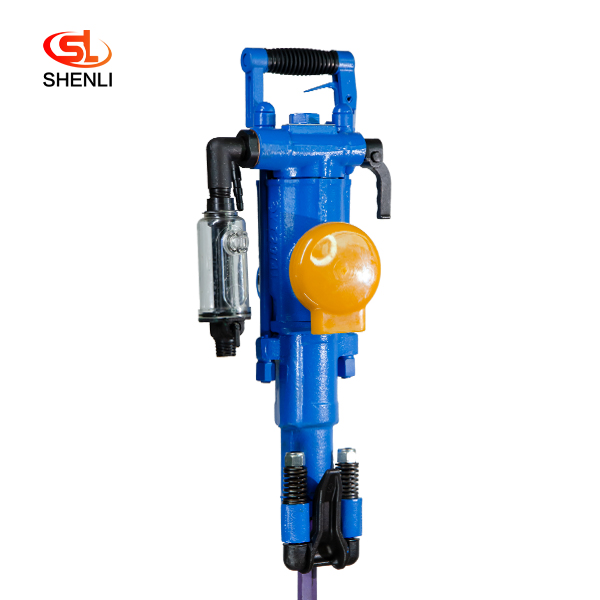
YT29A Air Leg Pneumatic Rock Drill
Short Description: YT29A air-legged rock drills are heavy-duty push-leg (air-legged) rock drills with low energy consumption, which are more suitable for drilling horizontal or inc […]
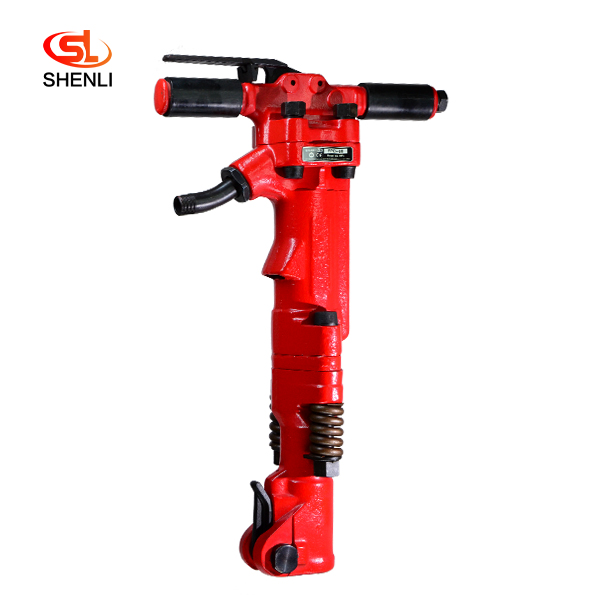
TPB6 Air Concrete Breaker Pneumatic Pick
Product introduction: TPB-60 crusher adopts the mature technology of TOKU Group, Is compressed air as the power of the crushing tool, can efficiently complete the reinforced concre […]
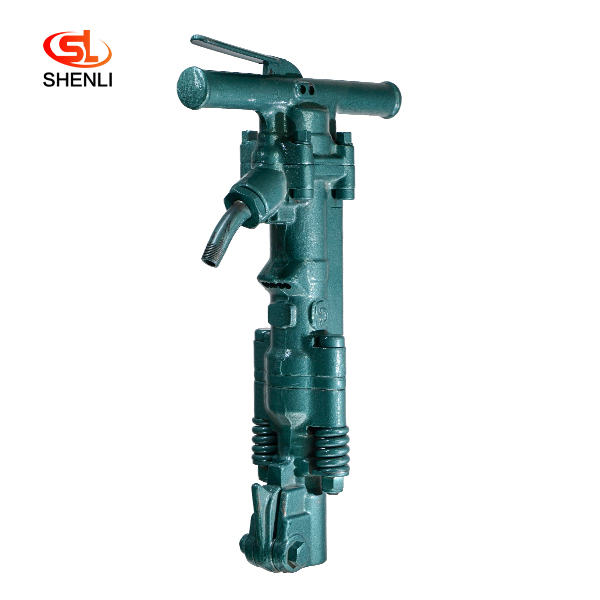
B47 Pneumatic Pick Air Shovel Cement Crusher Pneumatic Chipping Hammer
Product Description: B47 crusher adopts the mature technology of American Gardner Denver Pneumatic Group Company,It is a crushing tool powered by compressed air, which can finish r […]
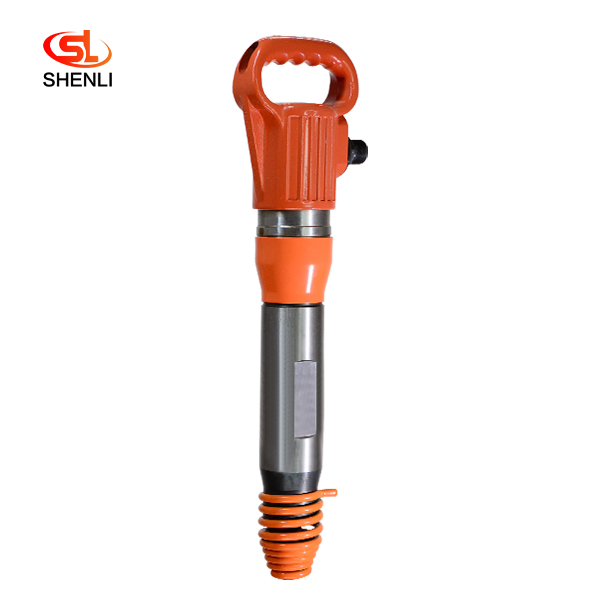
G10 Pneumatic Pick Air Shovel Cement Crusher
Product Description: The G10 air pick uses compressed air as the power tool, and the compressed air is distributed in two sections of the cylinder by the tubular distribution diver […]
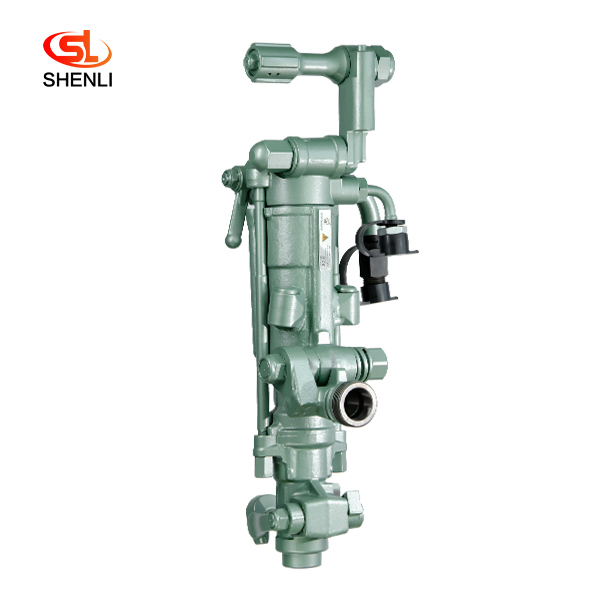
S250 Air Leg Pneumatic Rock Drill Pusher Leg Rock Drill
Product description: (S250 jackleg Drill) has been the preferred choice of miners who demand high performance, superior control and lasting reliability. the S250 jackleg allows ope […]
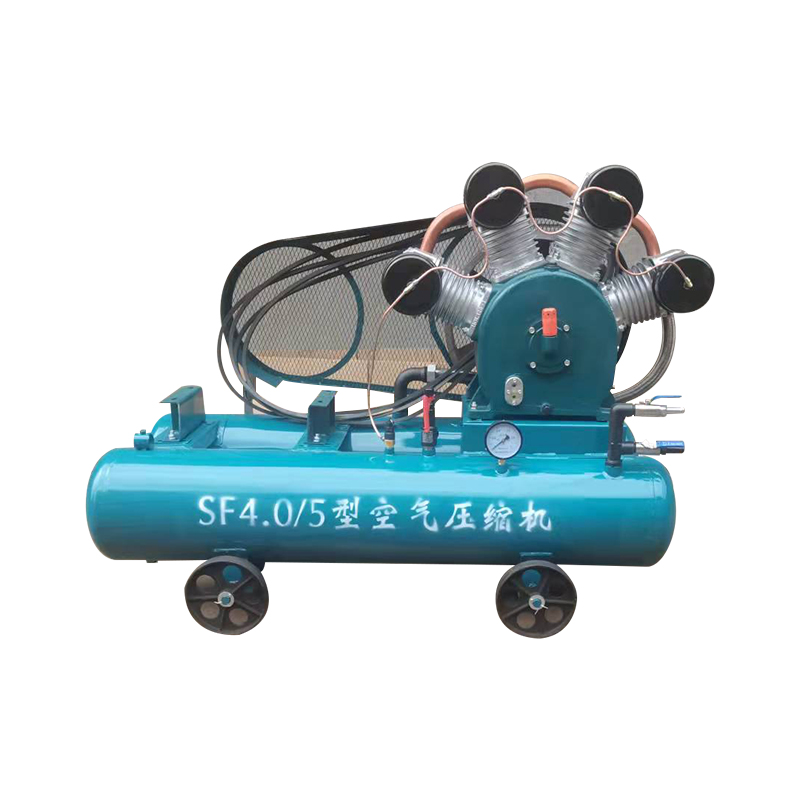
20KW Mining Diesel Piston Air Compressor SF4.0-5
Advantages Small in size,light in weight, easy to move Top material and superior technology Simple structure, high efficiency, good performance, and low price Adopt the most popula […]