An air compressor can be thought of as a powerful mechanical assistant that uses an electric motor or gas engine to draw in air and highly compact it. The generated pressure from the compressed air can then be used to operate machines like nail guns and air wrenches with ease.
The air compressor holds its power in two essential pieces, the pump and the tank. The task of compressing the air is taken on by the pump, while the recipient of all that compression is the tank.
When deciding on a compressor, its tank capacity is a major factor to consider as this controls how much air it can store. A sizeable tank will ensure the equipment will remain in use for an extended period before needing re-fueling.
When needing compressed air, many turn to piston-driven units. This style of compressor relies on a cylinder filled with a piston that moves back and forth, compressing the air before it is housed within a storage tank, ready for use when needed.
The rotary-type air compressor employs a spinning wheel to pressurize the oxygen, which is then contained in a container until it is required for usage.
When needing a supply of pressurized air, the screw type of air compressor can provide an invaluable function. With this mechanized system, a specially crafted screw is put into motion, thus compressing the air before storing it in a designated tank for future use.
A diaphragm-powered air compressor stores compressed air in a tank, providing an alternative method of compressing air. Pressure exerted by the diaphragm forces air molecules closer together, increasing their density and creating a volume of pressurized air. This stored air can then be switched on as needed.
Centrifugal force is the key to the fifth type of air compressor, acting as a means of compressing the air before it’s sequestered in a tank for later use.
The sixth model of air compressor is the spiral-design. Its operation involves using a spiral structure to compress the air, which is then stored in an integrated tank until demand for it arises.
Appropriately termed as turbo compressors, the seventh style of air pump relies on a turbo for pressurizing oxygen. Once pushed to the desired capacity, the oxygen is temporarily stockpiled in the tank, awaiting its purpose.
The eighth variant of air compressors is the positive displacement type, which uses a pushing mechanism to collect and store air until it is required. It works by compacting the air into a designated receptacle.
To complete the list, the variable speed air compressor stands as the ninth kind. This specific model employs a phased speed rotation to force air into the tank, where it will remain until put into use.
The core feature of the air compressor is without a doubt its pump. Without it, the air would remain uncompressed and unusable. This pump is synonymous with the machine – transforming nothing into something, in a mechanical sense.
The range of air compressors available today includes piston, rotary, screw, diaphragm, centrifugal, scroll, turbo, positive displacement, and variable speed systems.
Air is known for its complexity and versatility; a trait that is highlighted when discussing piston air compressors, the most ubiquitous type of compressor. This type of machinery utilizes a piston to drive the air, harnessing its power and compressing it until it becomes advantageous. Once the force of the air has been gathered in this fashion, it can then be contained within the tank – patiently awaiting its use.
Compressed air is produced in rotary air compressors by means of a rotating wheel, which is stored in the tanks until required.
A screw air compressor utilises a rotary screw mechanism to create compression. The resulting compressed air is then placed in a tank until its necessary deployment.
The diaphragm air compressor leverages a diaphragm to compress air, which is subsequently housed within a tank until utilization is required.
An intense centrifugal force is harnessed by centrifugal air compressors to pressurize and subsequently store the air in a tank until it is put to use.
Compressed air is kept in reserve with a scroll air compressor. Here, a scroll works to condense the oxygen before storing it in the container until utilized.
When the need for air arises, turbo-powered compressors step in and swiftly furnish pressure-driven flow from an enclosed storage tank. On demand, the turbo tool compresses air and stores it in its chamber until called upon.
Using a technique of positive displacement, air is packed into the tank until required by the application. This system of compressing air is referred to as a positive displacement air compressor.
In the process of air compression, variable speed air compressors employ a unique and effective technique of varying their speeds. The resultant air is stored in the vessel until its utilization becomes necessary.
Post time: 2023-06-29Related Product
Warning: Use of undefined constant rand - assumed 'rand' (this will throw an Error in a future version of PHP) in /www/wwwroot/www.sunritamachinery.com/wp-content/themes/msk5/single.php on line 69
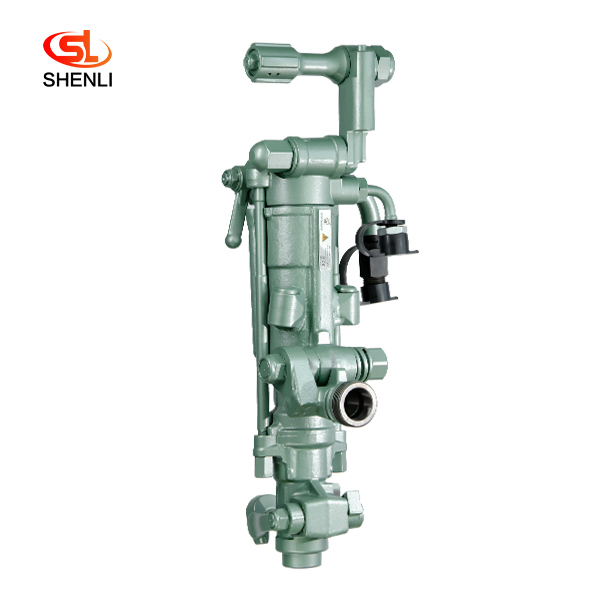
S250 Air Leg Pneumatic Rock Drill Pusher Leg Rock Drill
Product description: (S250 jackleg Drill) has been the preferred choice of miners who demand high performance, superior control and lasting reliability. the S250 jackleg allows ope […]
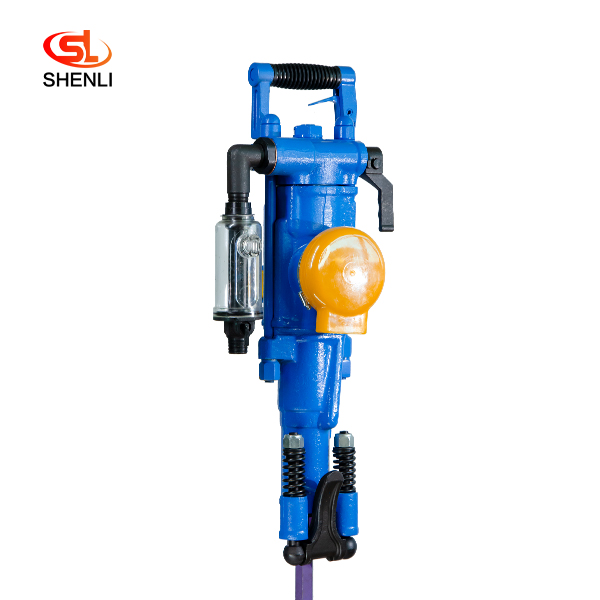
YT28 Pusher Leg Rock Drill
Short Description: The YT28 air-leg rock drill is a kind of high-efficiency, energy-saving and environmentally friendly rock drilling equipment. Compared with similar pneumatic pro […]
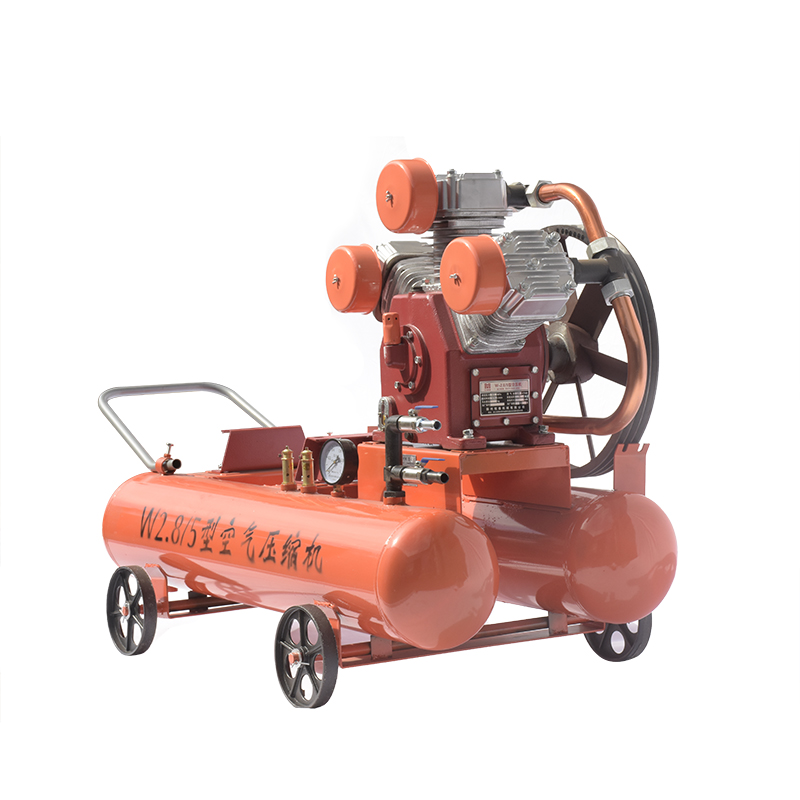
15KW Mining Diesel Piston Air Compressor W2.8-5
Diesel Portable Piston Air Compressor Mobile for Jack Hammer / Mining 1.Simple structure,light weight,easy to move . 2.Easy operating and maintenance. 3.High quality air delivery. […]
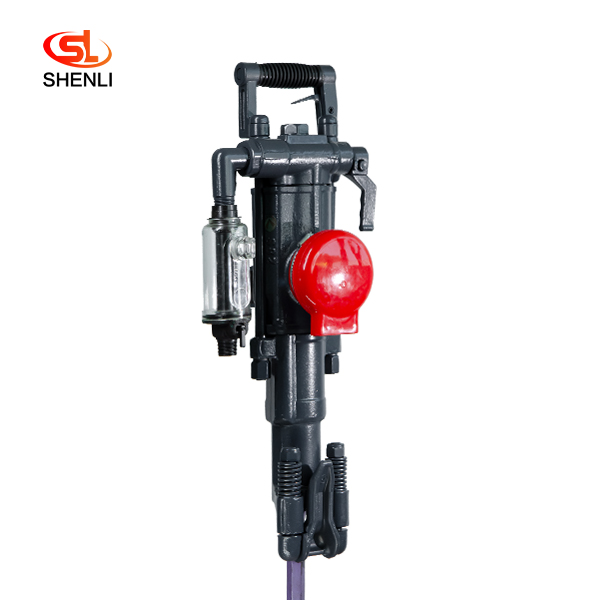
S82 Air Leg Pneumatic Rock Drill Pusher Leg Rock Drill
Scope of application: Model S82 air-legged rock drills are heavy-duty air-legged rock drills with high efficiency and low consumption, which are especially suitable for use in the […]
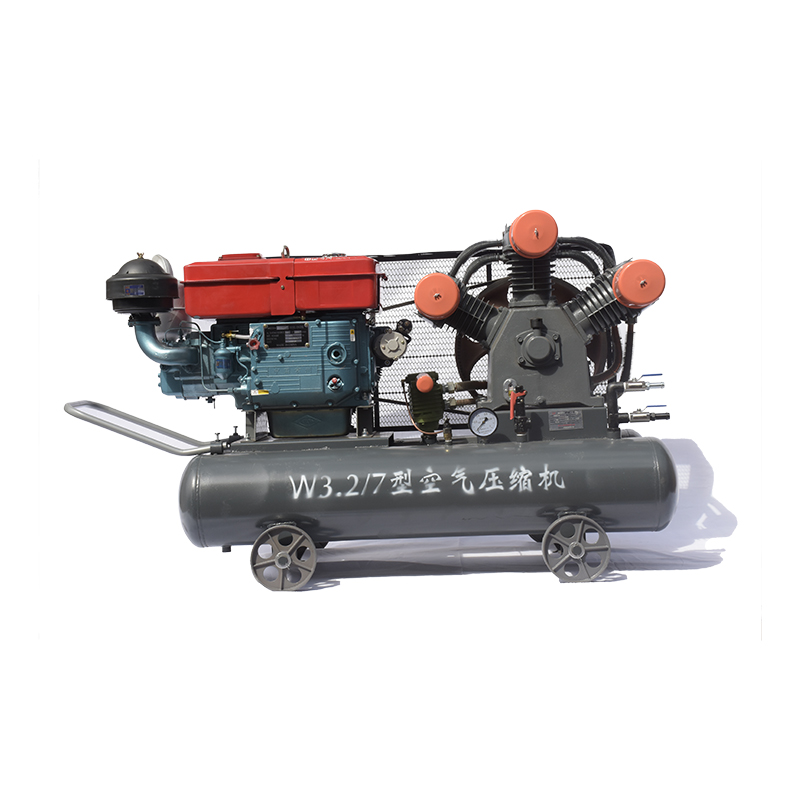
20KW Mining Diesel Piston Air Compressor W3.2-7
Advantages Small in size,light in weight, easy to move Top material and superior technology Simple structure, high efficiency, good performance, and low price Adopt the most popula […]
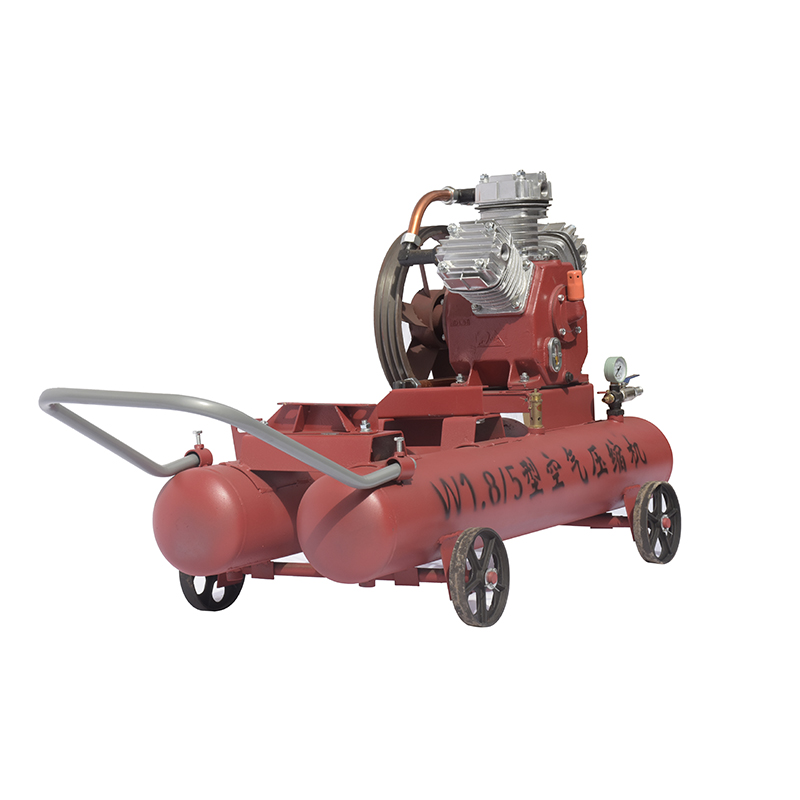
11KW Mining Diesel Piston Air Compressor W1.8-5
Diesel Portable Piston Air Compressor Mobile for Jack Hammer / Mining1.Simple structure,light weight,easy to move .2.Easy operating and maintenance.3.High quality air delivery.4.Su […]
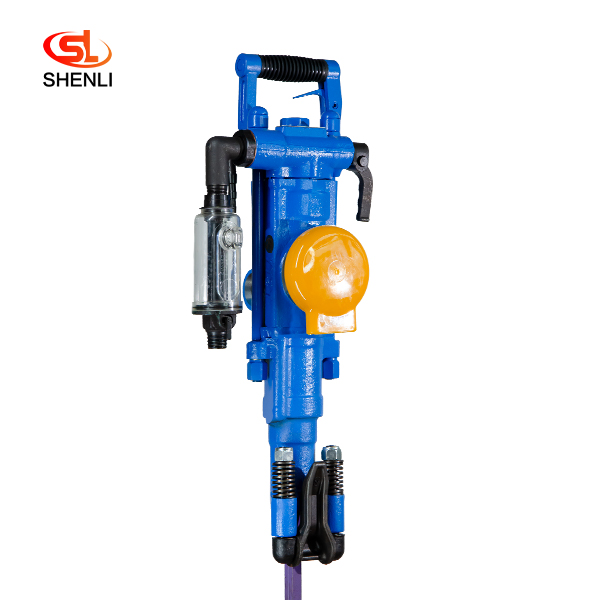
YT27 Air Leg Pneumatic Rock Drill
Short Description: The YT27 air-legged rock drill is a highly efficient lightweight rock drill suitable for downward or inclined drilling in medium-hard or hard (f=8 – 18) ro […]
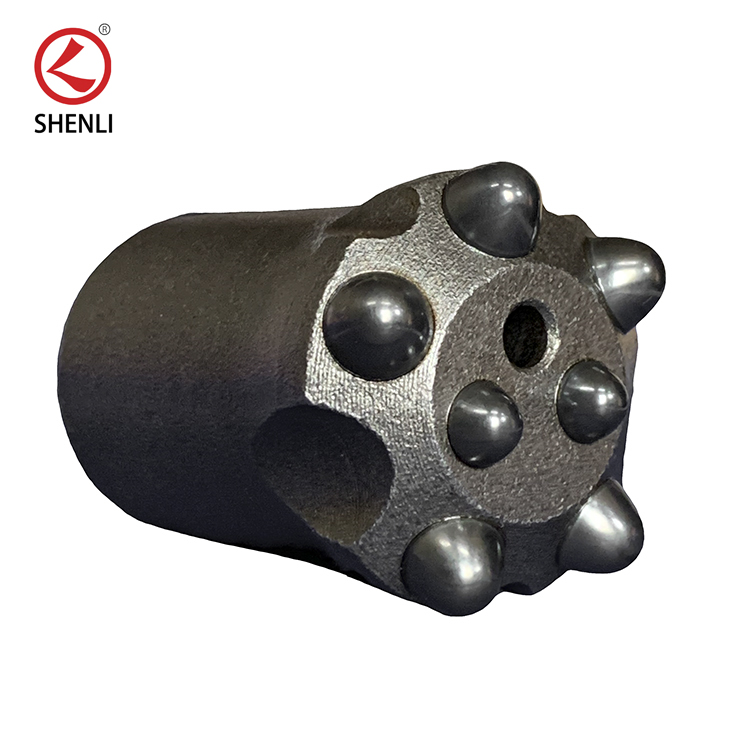
Rock Drill Button Bit
Product introduction: Taper bits, especially Tapered button bits are the most popular tapered drill bits with a wide selection of head diameters from 26mm to 48mm. With carbide but […]
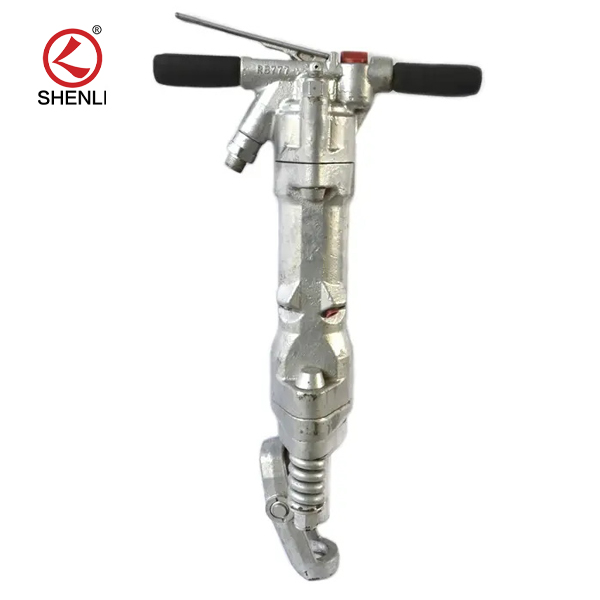
RB777 Pneumatic Pick Air Shovel Cement Crusher Pneumatic Chipping Hammer
Product description: RB777 pneumatic picks are used to build roads, install works of broken concrete and other hardens Hard object tools, the machine structure is simple, high effi […]