An air compressor is a powerful machine that traps potential energy by compressing air in a storage tank. It works by taking energy, typically from an electric motor, a diesel engine, or a gasoline engine and compressing air particles within the tank until the pre-set pressure levels are reached. When this limit has been achieved the compressor will cease operation and the potential energy stored within the tank will remain idle until it is needed. Once it is released, the kinetic energy of the air will put to work at completing tasks. In other words, an air compressor transforms energy into pressurized air and utilizes this power when required.
In the first decades of the 19th century, the earliest air compressors were created for a very specific purpose – to facilitate ventilation in mines. Pneumatically-driven, these compressors used a hand-powered piston to fill an attached cylinder with pressurized air, which was then stored until the moment when it was needed.
In 1872, A. C. Hobbs revolutionized the field of engineering by introducing his patented air compressor to the United States. This notably effective design was continuously utilized for many years, proving its worth in times of need.
In 1876, a revolutionary innovation was unveiled upon the world – the portable air compressor, gifted to humanity by G. F. Swain’s patent.
W. H. Harrison endeavored to revolutionize the pipeline industry in 1884 when he constructed the first air compressor powered by electricity.
In 1885, the vision of C. A. Parsons became reality with the designing and building of the first ever rotary air compressor.
In the late 19th century, C. G. Gilman and E. H. Gilman made history by founding the first prosperous outfit that mass-produced and supplied air compression systems specifically for quarrying operations.
In the year 1892, the American Air Compressor Company left an indelible mark in the annals of history by producing the world’s first comprehensive air compressor.
Air compressors have become indispensable in a vast range of domains, ranging from:
The automotive industry utilizes sources of energy to operate air tools, pump up tires, and more.
Industrially, tools such as air weapons and conveyors can be powered up.
Home is the ideal place to handle all your automotive-related needs from topping off tires for a smoother ride to powering the tools needed for DIY jobs.
Let’s Unpack the Mystery of Air Compressors
A diverse array of air compressors can be found in almost any shape and size, and while their appearances may vary, each one operates according to the same fundamental concept.
The pulse of the air compressor is rooted in its pump, the central system that pumps air into the tank and generates pressure. The most frequently seen pump is the piston body.
An electric motor or gasoline engine provides the power for the crankshaft which moves a piston up and down inside a cylinder; this is the operating principle of a piston air compressor.
Drawing in air, the piston rises and falls rhythmically in the cylinder, compressing it as it moves upward. An intake valve allows the air to enter as the piston ascends.
When the pressure in the cylinder rises due to compressed air, the pressure switch trips and shuts off the compressor once it has reached its intended maximum threshold.
The air is kept secure in the tank until use is required.
From an outlet valve, air from the tank is directed via a channeled hose to whatever device requires it; allowing for the airflow to provide the necessary power.
The air compressor is engineered to build the pressure of the air within to a greater level than is necessary for the tool’s function. This allows for a steady flow of air to move through the hose despite any length or attachment points along the pathway.
Upon intake, the air is permitted to expand, delivering a cooling sensation and bringing down the internal pressure of the tool. As soon as the pressure in the tool drops below atmosphere levels, the automated air compressor activates to begin replenishing the tank.
Unravelling the Varieties of Air Compressors
The functioning of air compressors can be categorized into two distinctive designs: positive displacement and negative displacement.
The process of positive displacement air compressors is to capture a steadfast amount of air within an area and then decrease its dimension. In doing so, the atmospheric pressure within the room is magnified.
Piston air compressors are the most ubiquitous kind of positive displacement systems, but rotary screw and vane models also exist and are worth noting.
In the act of negative displacement, air is brought into a compressor and subsequently sealed in. The boundaries of the chamber then expand, in turn causing the air to be bound into a tighter space. This process results in the air being ‘squeezed’ together, creating compression.
For negative displacement air compression, the most widely used style is the diaphragm variety. However, there are also Roots blowers and centrifugal compressors available.
Selecting the Ideal Air Compressor
When it comes to picking an air compressor, several elements should be taken into account. You must contemplate features such as size, capacity, pressure, and noise levels of the device. Additionally, consider how often you intend to use the compressor; cost and convenience of purchase and maintenance should also be evaluated. Ultimately, selecting an air compressor depends on how you wish to use it.
When selecting an air compressor, its size should be a priority factor, as it determines the amount of pressure it can store to successfully run the desired tool for a desirable duration.
What type is crucial when it comes to your air compressor since it has to be compatible with the air tool that will be used with it.
Leveraging Strength: A Study of Might
Post time: 2023-06-12Related Product
Warning: Use of undefined constant rand - assumed 'rand' (this will throw an Error in a future version of PHP) in /www/wwwroot/www.sunritamachinery.com/wp-content/themes/msk5/single.php on line 69
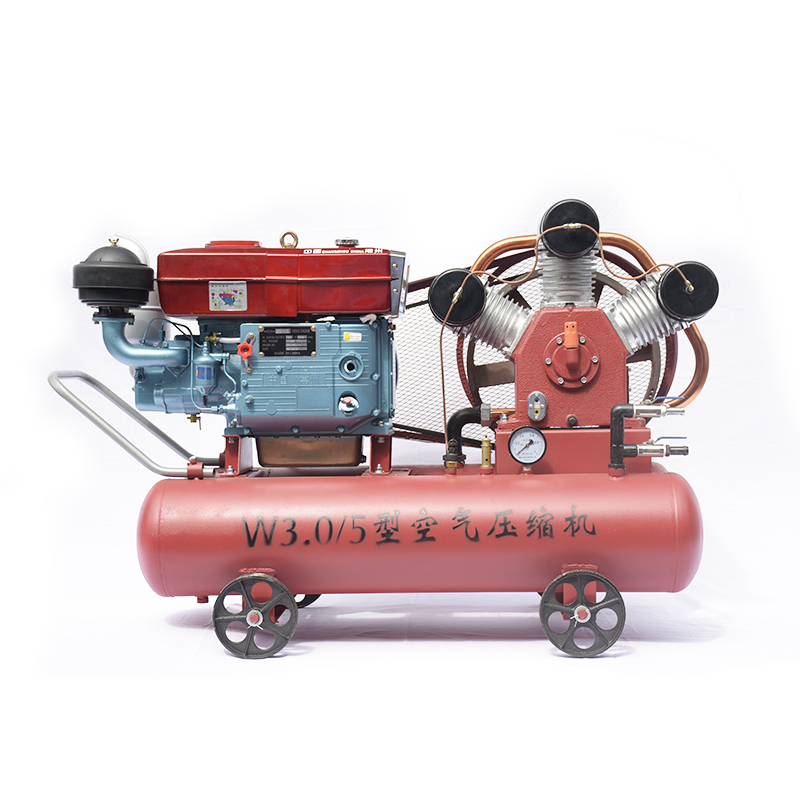
15kW Mining Diesel Piston Air Compressor W3.0-5
Diesel Portable Piston Air Compressor Mobile for Jack Hammer / Mining 1.Simple structure,light weight,easy to move . 2.Easy operating and maintenance. 3.High quality air delivery. […]
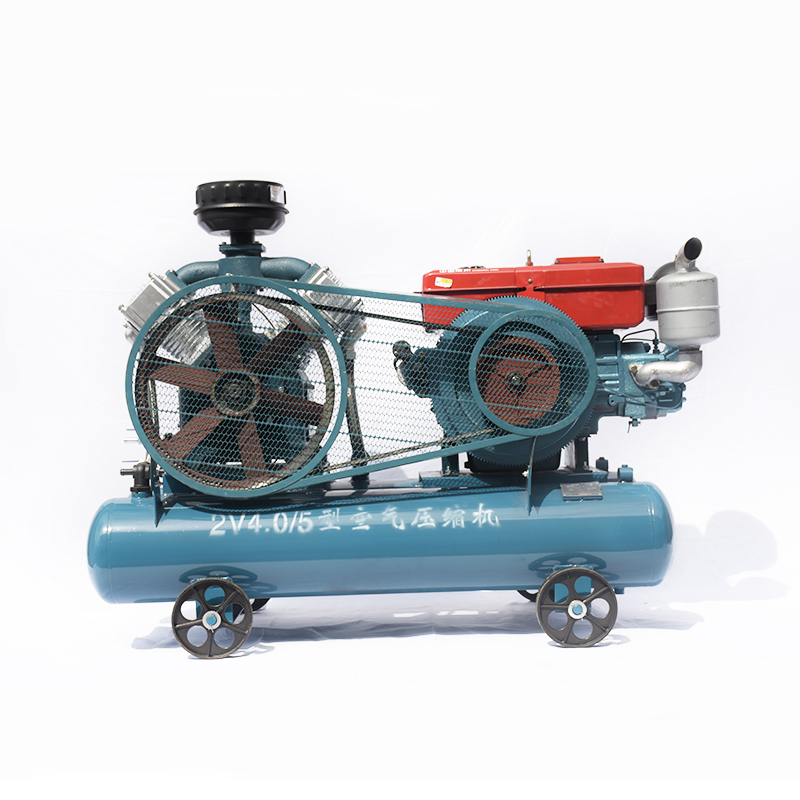
20KW Mining Diesel Piston Air Compressor 2V4.0-5
Double Air Tank Diesel Portable Best-Selling Engine Oil Piston Air Compressor are mainly used to supply stable and clean compressed air to the pneumatic tools and keep them working […]
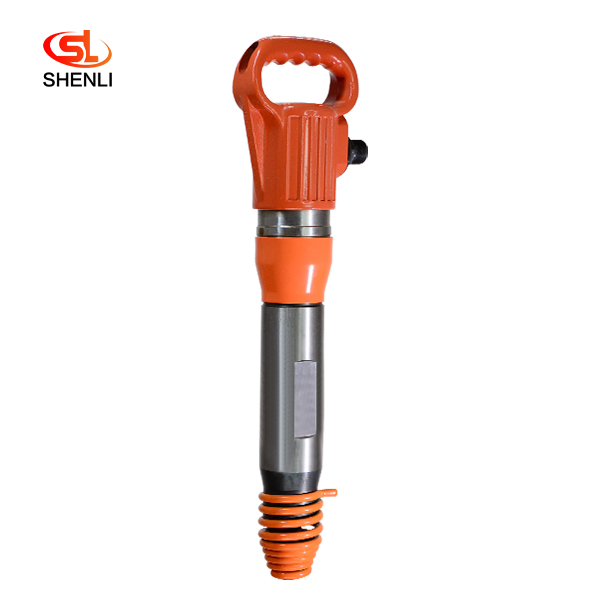
G10 Pneumatic Pick Air Shovel Cement Crusher
Product Description: The G10 air pick uses compressed air as the power tool, and the compressed air is distributed in two sections of the cylinder by the tubular distribution diver […]
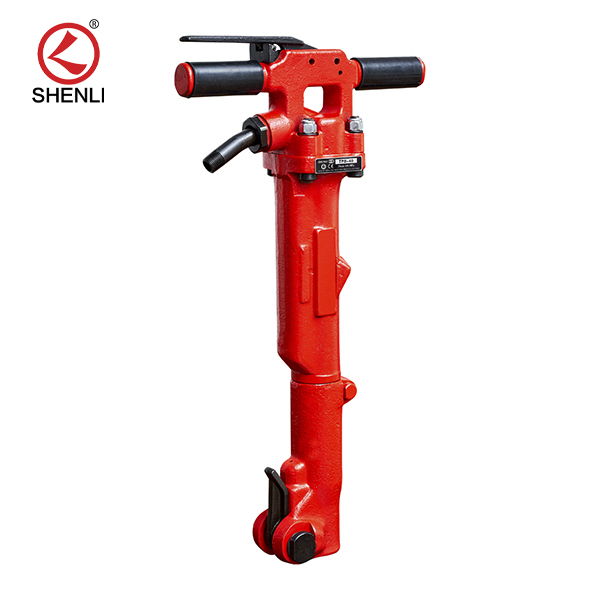
TPB40 Air Breaker Pavement Paving Breaker
Product introduction: Tpb-40 pneumatic crushing pick is a tool powered by compressed air.The compressed air is distributed to both ends of the cylinder block in turn to make the ha […]
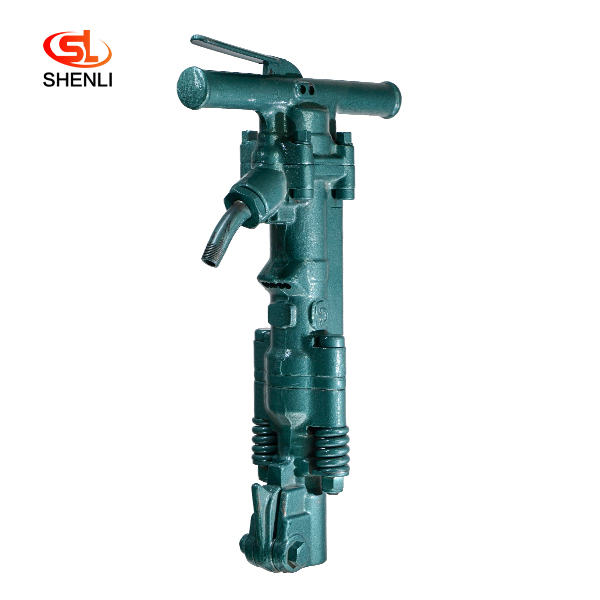
B47 Pneumatic Pick Air Shovel Cement Crusher Pneumatic Chipping Hammer
Product Description: B47 crusher adopts the mature technology of American Gardner Denver Pneumatic Group Company,It is a crushing tool powered by compressed air, which can finish r […]
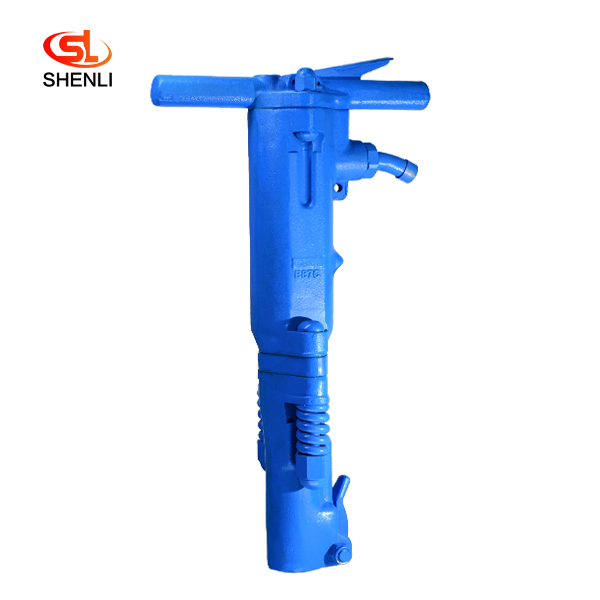
B87C Pneumatic Pick Air Shovel Cement Crusher
Product Description: The B87C crusher is made from Canada. Denver pneumatic Group company mature technology, with compressed air as a power crushing tool, can efficiently complete […]
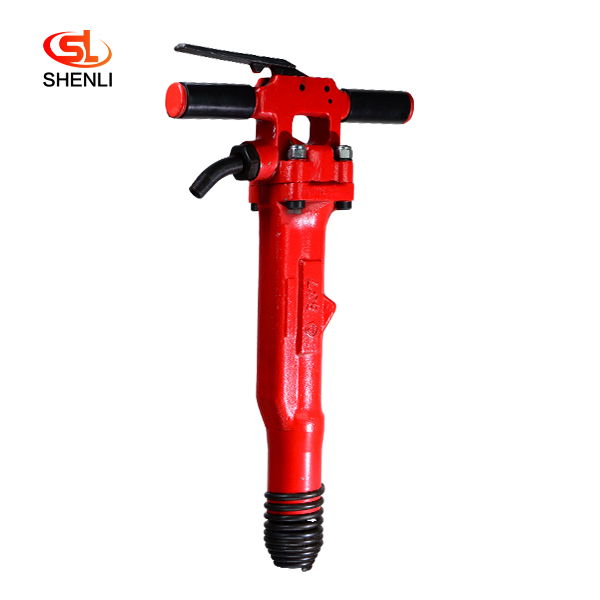
B37 Pneumatic Pick Air Shovel Cement Crusher Pneumatic Chipping Hammer
Product Description: B37 pneumatic crushing pick is a tool powered by compressed air. The compression the air is distributed to the two ends of the cylinder block in turn, so that […]
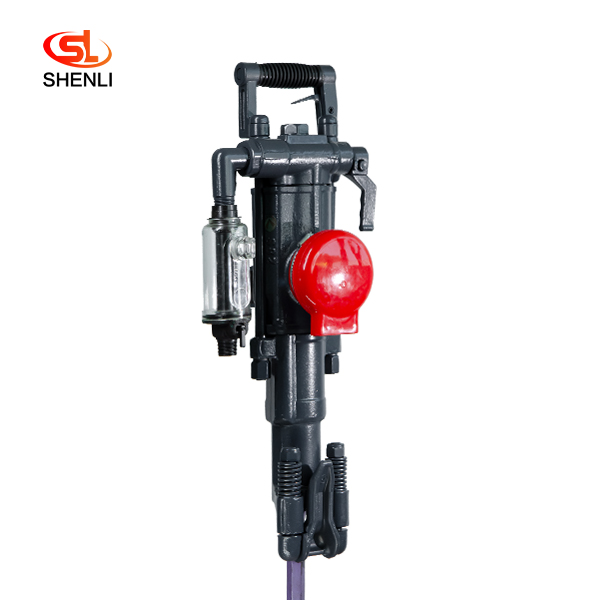
S82 Air Leg Pneumatic Rock Drill Pusher Leg Rock Drill
Scope of application: Model S82 air-legged rock drills are heavy-duty air-legged rock drills with high efficiency and low consumption, which are especially suitable for use in the […]
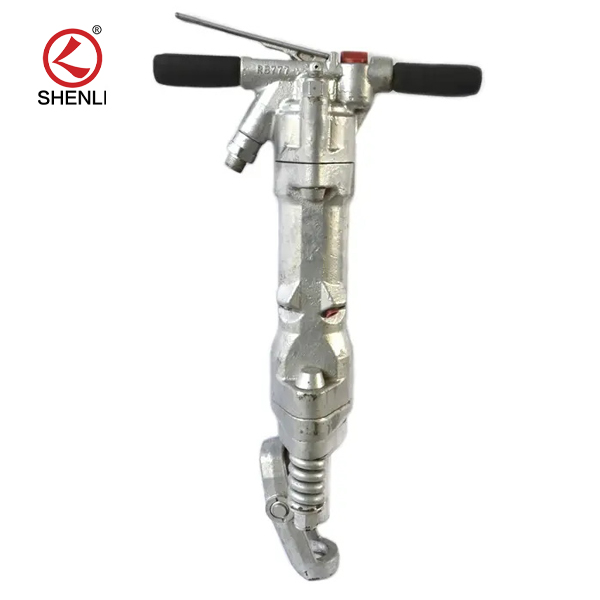
RB777 Pneumatic Pick Air Shovel Cement Crusher Pneumatic Chipping Hammer
Product description: RB777 pneumatic picks are used to build roads, install works of broken concrete and other hardens Hard object tools, the machine structure is simple, high effi […]