An air compressor is a mechanized contraption which, powered by an electric motor or engine, efficiently sucks in air and compresses it to occupies a much smaller space. This clever device is used in numerous everyday activities, for example, powering tools such as jackhammers and air ratchets along with other handy duties like filling tires with air and providing power to air conditioners.
Exploring the Power of Air Compressors.
At the core of the air compressor is the pumping mechanism, essential for squeezing the air. The typically employed reciprocating piston pump comprises a cylinder with a lone piston travelling up and down. During its ascension in the chamber, the piston permits air to enter through an intake valve. The subsequent subsidence forces out that same air, allowing it to pass through an exit valve.
The degree of compression a pump can reach is limited by how much the cylinder’s volume decreases and increases during its up- and downstroke respectively. For instance, a compressor with a cylinder that decreases to one cubic inch on its downstroke and increases to half a cubic inch on its upstroke can only manage a compression ratio of 2:1.
Achieving a higher compression ratio can be done through the use of a multi-cylinder air compressor. These air compressors can be divided into two distinct groups: single-stage and two-stage.
Through a communal crankshaft, two or more cylinders join forces in a single-stage air compressor, enabling air to move from one cylinder to the next as it gradually gets compressed.
Two banks of cylinders in a two-stage air compressor create a consecutively increased pressure with each cylinder. From each bank, the first cylinder pulls in air and over compress it to a low pressure, then it continues on to the second cylinder where it is further compressed to a higher pressure.
The cylinders of both single and two-stage air compressors are capable of releasing air into a storage tank with the help of a discharge valve.
Air compressors possess cooling systems to alleviate the heat built up from compression of air. Two potential solutions that often come into play are air-cooled and water-cooled processes.
To keep the compressor from becoming too hot, an air-cooled systemdirects a flow of air over its cylinders. Essentially, the system harnesses the potency of air to regulate the temperature of its compressor.
In much the same way a vehicle’s engine is cooled, a water-cooled system depends on the circulation of water to maintain an optimal temperature inside the compressor. Water moves through the cooling jacket, encircling the cylinders, and is then directed into a radiator which reduces its heat. It’s a simple yet effective method that keeps the compressor functioning at its best.
How powerful your air compressor is indicates how much air it can pump and what size projects you can take on. This power is typically represented in horsepower (hp) and cubic feet per minute (cfm). A higher rating for either unit makes the compressor more capable of powering larger projects while a lower rating places the machine in a capacity for smaller tasks. In essence, the hp rating signifies the strength of the motor while cfm denotes the volume of air that can be provided at a given pressure.
The amazing power of a 1 horsepower air compressor can be best understood by its ability to fill a car tire in just two minutes. 90 psi of air can be produced from it, which is roughly four cubic feet per minute. To interpret this with more clarity, the average car tire contains 22 psi of air.
Most compressors used in home settings have been constructed with a purpose in mind – to operate under a pre-specified pressure. This pressure level is typically defined by pounds per square inch (psi) units, for instance, 120 psi for regular domestic air compressors.
A compressor, for all its robustness, faces a limit when it comes to the air pressure it can produce. The amount of atmosphere the pump can transfer and the durability of the materials in the compressor determine how much force can be generated. Heat can also influence air pressure; as compressed air temperatures rise, the pressure weakens.
To boost the amount of pressure produced by an air compressor, air can be chilled between its stages of compression. This is commonly done utilizing an intercooler, which serves as a radiating system for routing air flow.
The ability of an air compressor to exert the full force of its pressure is regulated by the discharge valve. This valve is responsible for controlling and managing the flow of pressurized air from the compressor to the storage tank.
The pressure within the compressor fills until it matches the setting of the discharge valve, which then allows for a flow of air to enter the storage tank. In other words, when the pressure has compressed to a specific point, the valve opens up and a rush of air is permitted to move onward.
The discharge valve is what shapes the performance of the air compressor as it works to fill the tank; the speed at which it opens dictates how quickly it will accomplish its task. The quicker the valve is activated, the briefer the time in which the compressor can load up the storage tank.
When the force within the storage tank reaches a threshold, the pressure relief valve – a security measure – springs into action, gently releasing the tension and averting any hazardous outcomes.
The pressure relief valve safeguards the reservoir from building up undue force, protecting it from intense strain and possible damage. It functions by managing the pressure levels within the tank, averting potentially hazardous high pressure build-up.
Post time: 2023-06-23Related Product
Warning: Use of undefined constant rand - assumed 'rand' (this will throw an Error in a future version of PHP) in /www/wwwroot/www.sunritamachinery.com/wp-content/themes/msk5/single.php on line 69
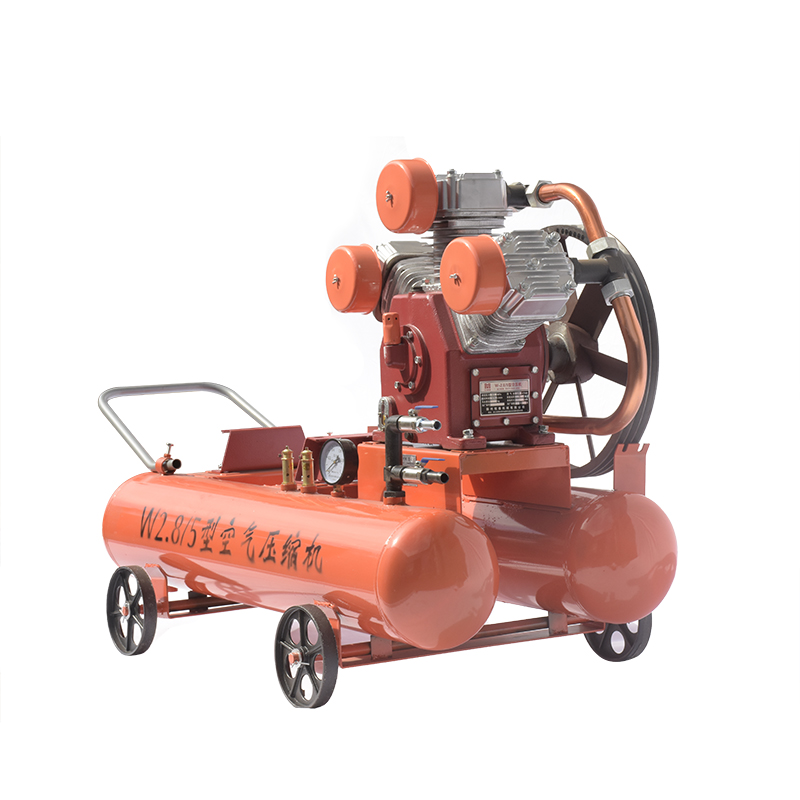
15KW Mining Diesel Piston Air Compressor W2.8-5
Diesel Portable Piston Air Compressor Mobile for Jack Hammer / Mining 1.Simple structure,light weight,easy to move . 2.Easy operating and maintenance. 3.High quality air delivery. […]
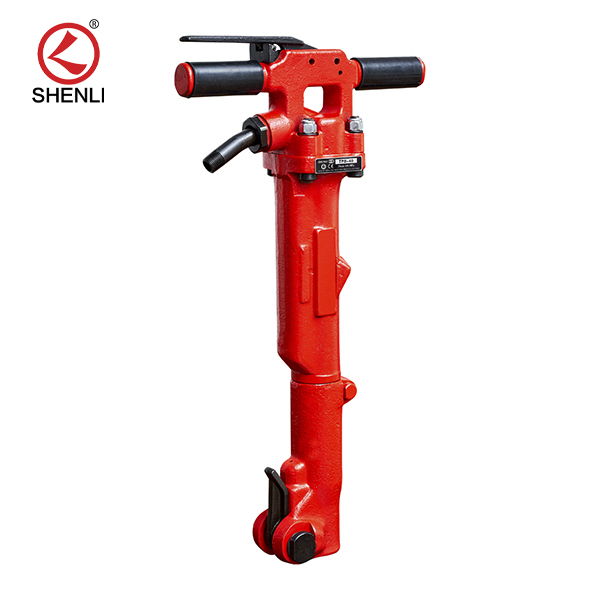
TPB40 Air Breaker Pavement Paving Breaker
Product introduction: Tpb-40 pneumatic crushing pick is a tool powered by compressed air.The compressed air is distributed to both ends of the cylinder block in turn to make the ha […]
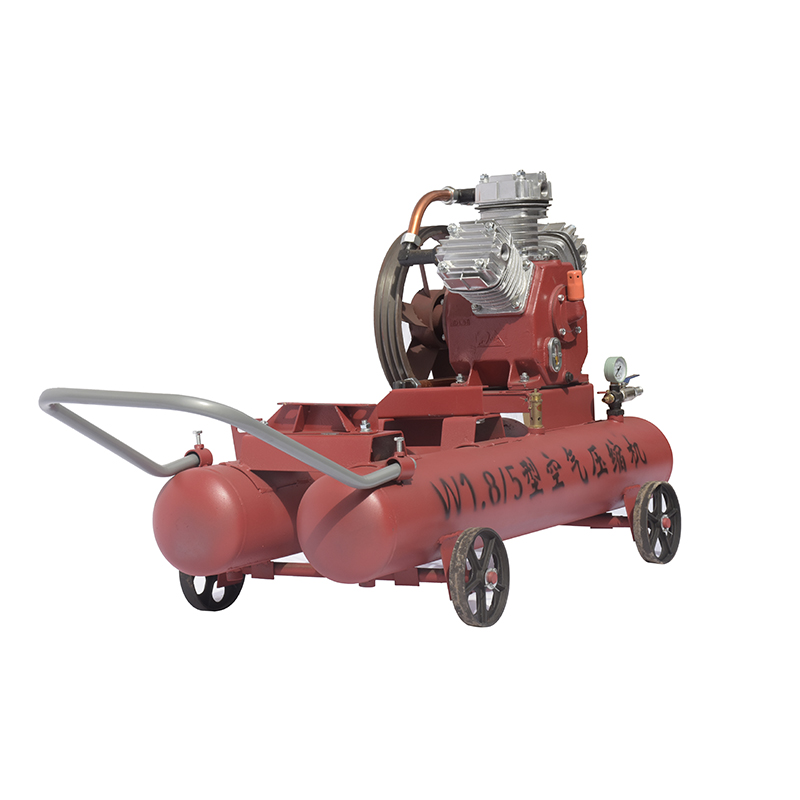
11KW Mining Diesel Piston Air Compressor W1.8-5
Diesel Portable Piston Air Compressor Mobile for Jack Hammer / Mining1.Simple structure,light weight,easy to move .2.Easy operating and maintenance.3.High quality air delivery.4.Su […]
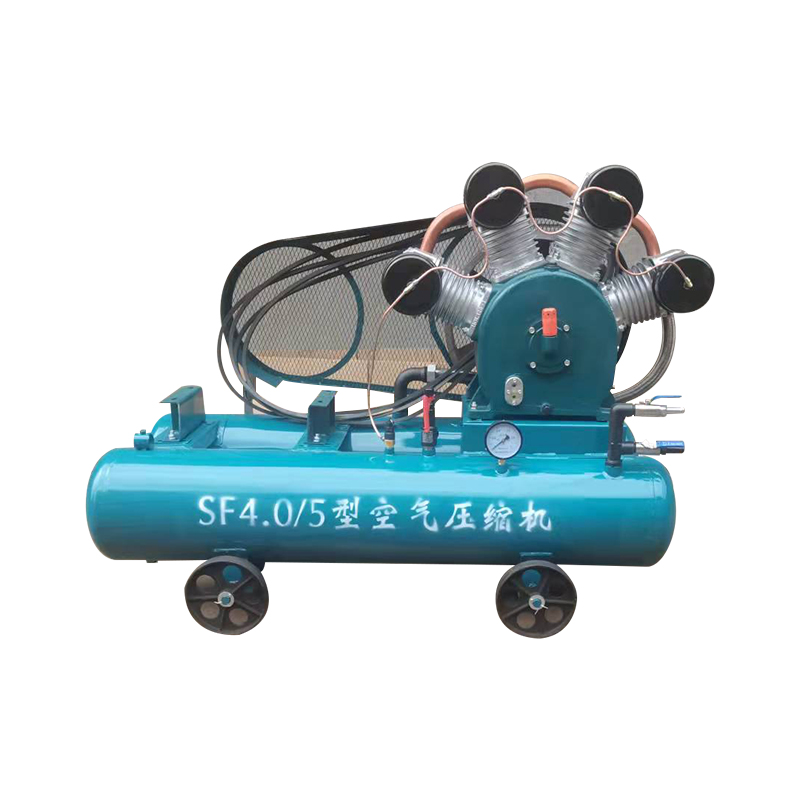
20KW Mining Diesel Piston Air Compressor SF4.0-5
Advantages Small in size,light in weight, easy to move Top material and superior technology Simple structure, high efficiency, good performance, and low price Adopt the most popula […]
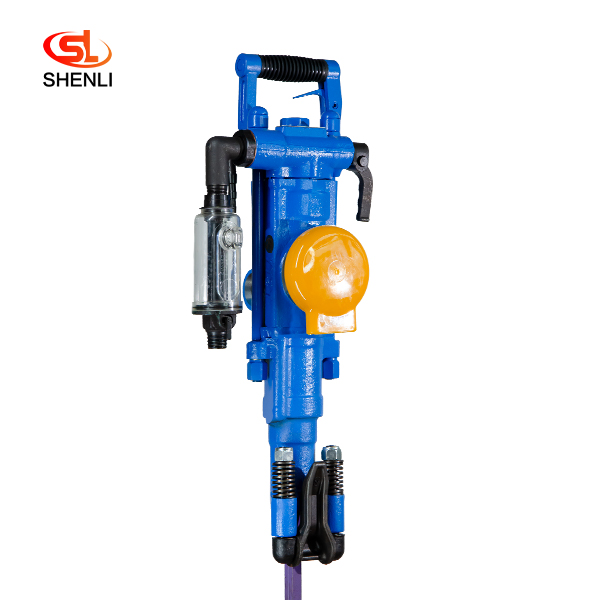
YT27 Air Leg Pneumatic Rock Drill
Short Description: The YT27 air-legged rock drill is a highly efficient lightweight rock drill suitable for downward or inclined drilling in medium-hard or hard (f=8 – 18) ro […]
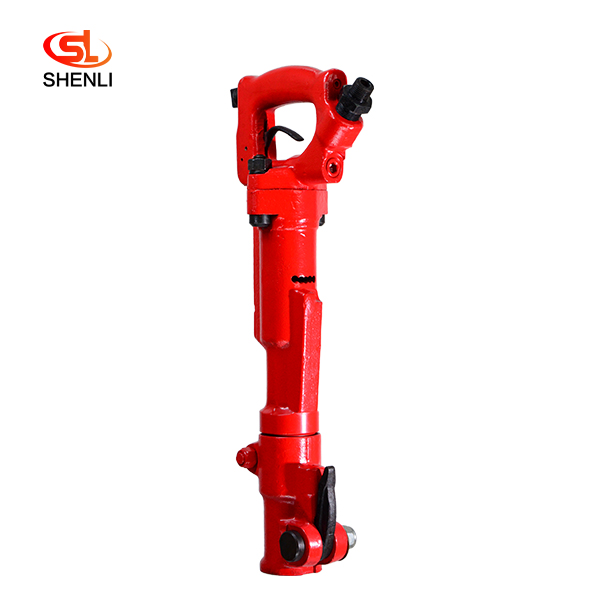
TCD20 Pneumatic Pick Air Shovel Cement Crusher Pneumatic Chipping Hammer
Product description: The TCD-20 pneumatic pick is powered by compressed air using Japan’s TOKU technology Crushing tools, features: lightweight, small size, large strike ener […]
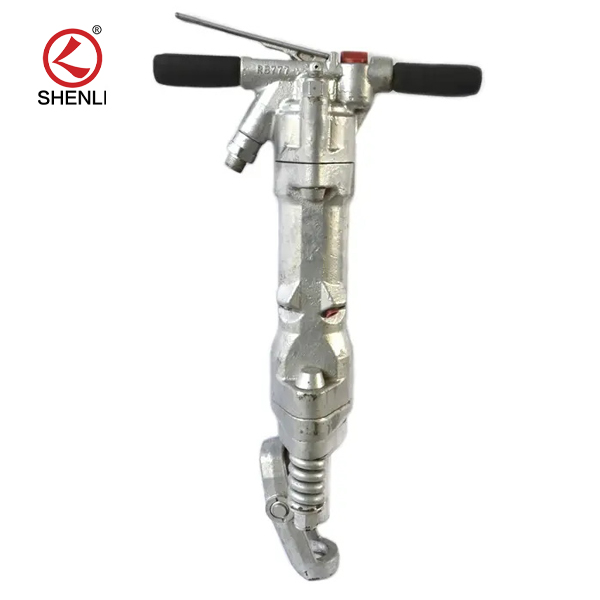
RB777 Pneumatic Pick Air Shovel Cement Crusher Pneumatic Chipping Hammer
Product description: RB777 pneumatic picks are used to build roads, install works of broken concrete and other hardens Hard object tools, the machine structure is simple, high effi […]
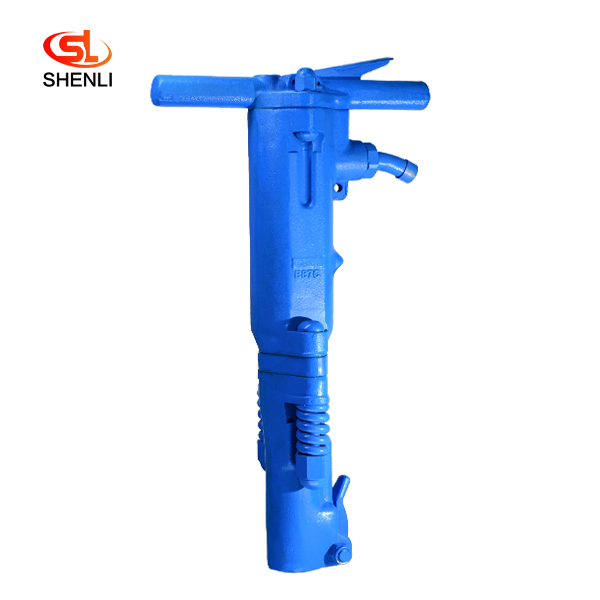
B87C Pneumatic Pick Air Shovel Cement Crusher
Product Description: The B87C crusher is made from Canada. Denver pneumatic Group company mature technology, with compressed air as a power crushing tool, can efficiently complete […]
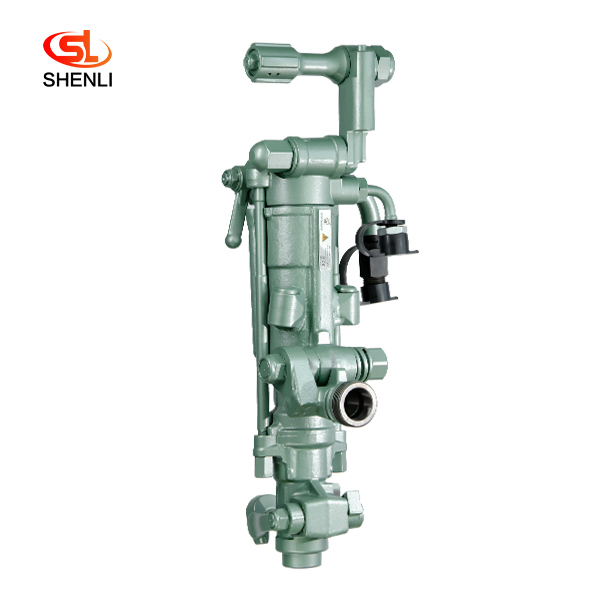
S250 Air Leg Pneumatic Rock Drill Pusher Leg Rock Drill
Product description: (S250 jackleg Drill) has been the preferred choice of miners who demand high performance, superior control and lasting reliability. the S250 jackleg allows ope […]